Also, download this story from the electronic issue here
The bioplastics industry sees companies and research institutes that are showing their commitment with investments and technology respectively to develop new materials that are biobased and biodegradable.
Merger and acquisition benefits production
Not all companies are content to produce solely in China. One such US bioplastics products maker Trellis Earth Products now expects to make 50% of its products in the US, having recently paid US$2.6 million for the assets of defunct bioplastics materials firm Cereplast, which was liquidated in bankruptcy court. Assets it has purchased include a 110,000 sq ft bioplastics production facility in Seymour, Indiana; patent portfolio, and inventory with a replacement value over US$8 million. It has also paid certain contract costs, as part of Cereplast's Chapter 7 liquidation proceedings.
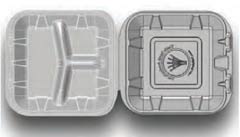
Trellis has three contract manufacturers in China and with Cereplast’s plant will allow it to manufacture in the US. Cereplast’s plant, which has the capacity to produce US$50 million worth of products, will also allow Trellis to fast track its large scale injection moulding and thermoforming operations in the US.
Trellis is a seven-year old company with over 500 customers in the food service industry and provides biobased cutlery, food containers, and shopping bags. It expects to post sales of US$8.5 million in 2015.
Elsewhere, PHA producer Meredian and sister company DaniMer Scientific have merged under Meredian Holdings Group to increase the size and market awareness of both companies and allow for vertical integration into their supply chain. Meredian manufactures PHA biopolymers using renewable resource and has recently harvested its first locally sourced canola crop to produce biopolymers.
Financing for investing into plants
Dutch biobased materials and packaging firm Avantium has received EUR36 million financing from a group that includes beverage maker Coca-Cola, Austrian blow moulder Alpla Werke Alwin Lehner, French food conglomerate Danone, and British investment firm Swire Pacific. Existing shareholders include Sofinnova Partners, Capricorn Venture Partners, ING Corporate Investments, Aescap Venture, Navitas Capital, Aster Capital and De Hoge Dennen Capital.
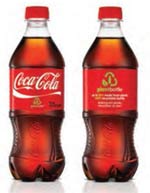
The investment will be used to advance the development of a biobased alternative to PET, polyethylene furanoate (PEF), as well as for industrial validation of PEF and finalising the engineering and design of the first commercial-scale plant.
The firm is already working with Coke to make bottles from PEF, which is said to be a 100%-biobased plastic with improved performance. Avantium currently makes PEF using the YXY technology at a 20-tonne pilot plant in Geleen, the Netherlands, and expects to start-up a 50,000-tonne/year commercial plant by 2017.
The firm says its partners “need larger quantities for both technical testing and market tests and thus, the need to scale up.” It says its ultimate goal is that the PEF bottle is made from responsibly sourced plant based materials, such as second generation feedstock.
Elsewhere, BioAmber’ s Canadian subs idiar y BioAmber Sarnia, a joint venture with Mitsui, has secured a CAD$20 million commercial loan from a financial consortium led by Export Development Canada as well as Farm Credit Canada and Comerica Bank. It will be used to complete the ongoing construction of the Sarnia plant and fund its start-up and commissioning.
When completed in early 2015, the Sarnia plant will be the world's largest biobased succinic acid production facility. The plant will convert Canadian agricultural products into biobased succinic acid, a value added building block chemical that is used in a wide variety of everyday products. BioAmber projects that over 90% of the 30,000 tonnes/year capacity will be exported.
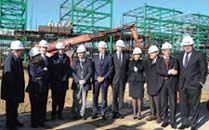
Italy-based Matrìca, a 50:50 joint venture between Italian petrochemicals maker Versalis and US-based Novamont, has opened the first of its three green chemistry plants for converting vegetable oils into monomers and intermediates in Italy.
Over the course of the year, the firm says it will open another two plants being bui l t at the new Matrìca complex. At these two plants, monomers and intermediates will be transformed into extensor oils for the tyre industry and other products such as bases for bio-lubricants, plasticisers for polymers and products for cosmetic formulations.
The company says the three plants will have an investment of EUR180 million and a total capacity of 70,000 tonnes/year of bio-products. A result of a 20-year research, the process is said to be different from competitors. It uses a proprietary technology that does not use ozone in the vegetable oil oxidative scission reaction and allows the production of intermediates known as azelaic acid and pelargonic acid, as well as new proprietary products, through a safe process with low environmental impact.
New research on starch for bioplastics
Researchers in Finland have developed a starch-based biodegradable plastic with a high degree of mechanical strength and good thermal resistance. This biomaterial is targeted at applications in food packaging and biomedical materials.
Starch is a polysaccharide consisting of two components: a linear glucose polymer called amylose and a highly branched glucose polymer called amylopectin. Most green plants store their energy as starch and it is present in large quantities in grains such as maize, wheat and rice, in addition to tubers like potatoes. A brittle polymer, starch can be treated with heat and water, via a technique called gelatisation, to make it suitable for traditional plastic processing techniques.
However, films prepared by this method rapidly recrystalise and degrade, leaving them amorphous and brittle again. Many small molecules have been used as plasticisers that hydrogen bonds with the glucose units in starch to prevent recrystallisation, however they are prone to migration and leeching, again degrading over time. Unfortunately larger compounds are typically less effective plasticisers.
Now, researchers from the Aalto University have used a star-shaped molecule called AEEP (aminoethoxy ethanol substituted phosphazene), the arms of which act as dynamic and mobile hydrogen bonding plasticiser molecules while being connected to a central core, effectively preventing migration and leeching of the starch molecules from the resulting plastic.
The researchers are now testing AEEP within a range of biopolymers, in addition to investigating the selfhealing properties of their starch-based plastic.
Biodegradable bottle project
Meanwhile, Spain’s institute of plastic technology, Aimplas, is coordinat ing a two-year research on developing a biodegradable material, in partnership with seven European partners, to reduce waste and increase recycling. The aim of the Biobottle project is to create multi-layer and monolayer plastic bottles, as well as bags for dairy packaging, which do not require to be separated from the rest of the organic wastes at the end of their brief lifespan.
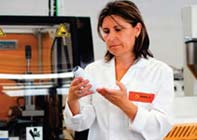
Aimplas says that Europe is the world’s biggest consumer of dairy products globally, with an average of 261 kg per year, according to data provided by FAO in 2011. But only 10-15% of the 2 million tonnes of HDPE milk bottles used are recycled.
According to Aimplas, one of the main difficulties of Biobottle is getting a biodegradable material that complies with the same requirements as traditional packaging, including resistance to thermal treatments such as the sterilisation or pasteurisation.
Biobottle is a European project in the Seventh Framework Programme and has received funding of EUR1 million.
(PRA)