Also, download this story from the electronic issue here
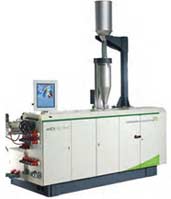
At a time when energy costs, carbon footprint, and economics are crucial issues across manufacturing industries, there is no other important technology than the one that is energy efficient. Battenfeldcincinnati (Foshan) Extrusion Systems, the Chinese arm of Austrian machinery maker battenfeld-cincinnati, has tweaked its machinery to offer energy efficiency.
Focus on efficiency
According to the International Energy Agency (IEA)’s 2013 report, energy efficiency is the world’s important fuel. Energy efficiency holds the spotlight in the International Energy Efficiency Scorecard report by the American Council for an Energy Efficient Economy (ACEEE). This year, ACEEE’s second edition report cites Germany as leading the top 16 largest economies worldwide, which comprise more than 81% of global GDP and about 71% of global electricity consumption.
Energy efficiency is unquestionably a defining factor in today’s industries. It is also topmost in extrusion specialist battenfeld-cincinnati’s agenda.
In a recent interview with PRA, Mark Feng, General Manager of battenfeld-cincinnati (Foshan) Extrusion Systems, said, “We place emphasis on energy efficiency in our machines and processes by optimising the screw and die design, and using AC main motor as a standard offering.”
Feng went on to say that the company’s machinery is able to achieve about 30-50% energy savings per tonne for PO pipe processing when compared with locally produced machines.
“In addition, we offer an inner cooling system for large diameter/high output PO pipe extrusion and green pipe/profile downstream equipment for more energy savings. The energy saving feature is definitely one of the most important selling points for our machinery besides the high output, high stability, automation and long life span,” he adds.
Stable sales
Formerly known as B+C Extrusion Systems (Foshan), the company changed its name in 2010 as a result of a rebranding exercise. It was founded in 1996 and is based in Foshan, China.
“We produce around 150 extrusion lines a year and have a turnover of US$45 million, 85% of which is from the local market, and 15% is from exports,” according to Feng.
The Foshan operation now has a production space of 130,000 sq ft and a workforce of 180. Nevertheless, the company does not see itself expanding over the next five years.
Feng explains, “This is because the plastic extrusion machinery market is, comparatively, not a very big market, yet the competition is quite high. On the other hand, by optimising the production/ management, we can manage to double the sales volume with the existing factory.”
New to the market
The company manufactures and markets extrusion equipment and systems. It offers single and twin-screw, parallel twin, and conical twin extruders. Additionally, the company provides control and automation systems.
At the Chinaplas show, held in Shanghai this year, battenfeldcincinnati showcased the top billed solEX single-screw extruder series.
Following the success of the demonstration of a PE gas pipe extrusion line in September 2013 and the display of the soIEX60 series at Chinaplas last year, the solEX 75-40-C extruder was shown at Chinaplas 2014.
At battenfeld-cincinnati’s open house last year, on display was a line with a solEX extruder and the company’s green pipe downstream equipment. A PE gas pipe with a diameter of 250 mm was produced in co-operation with some long-term partner companies.
“The solEX extruder series for high-performance PE-HD and PP pipe extrusion was shown for the first time at an exhibition in China. At our open house in Foshan in September 2013, we realised there was a lot of interest from our customers on the topics of energyefficiency and energy savings,” said Feng.
The highlights of the solEX extruder series are the higher throughputs with smaller screw diameters, a smaller footprint and improved melt homogeneity with low energy input.
Feng also says that the solEX 40 L/D ratio series PO pipe extruders have the highest output, compared with extruders with the same screw diameter from other suppliers.
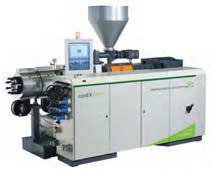
Other products on display
Another exhibit at the booth was the conEX 63 R-C conical twin-screw extruder. This series is characterised by cost and material savings, especially in profile production. The conEX extruder series comprises four models, featuring screw diameters ranging from 38 to 72 mm, with energy efficiency due to the barrel insulation system and vacuum aggregate pumps, with reduced water volumes and a new vacuum filter complete with filter sump.
The series constitutes the sixth generation of conical twin-screw extruders from battenfeld-cincinnati, based on the proven predecessor series of konos extruders.
The screw geometry has been further optimised to enable an output of up to 10% in both pipe and profile extrusion (for pipes up to 550 kg/hour and for profiles up to 280 kg/hour).
Patrons of the new lines include chemicals and building supplier Wuhu Conch Profiles and Science (Anhui/China), which installed 24 extruders in 2012 to expand its PVC processing capacity.
Another product on display was the helix VSI 250 pipe head. Battenfeld-cincinnati says the VSI dies are the only dies on the market with a two-step distributor concept consisting of a spiral mandrel for preliminary distribution and a lattice basket distributor for fine distribution. This, thus, allows for homogenisation, high outputs, a wide processing window and consistent, high product quality across all pipe dimensions.
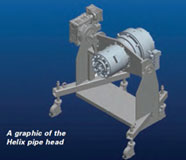
Further improvement comes for the Alpha singlescrew extruder for technical profiles and small pipes, which has been on the global market for over 12 years with more than 750 units sold.
In contrast to the predecessor models, the revised Alpha extruders are now equipped with a new compact drive system, which offers the benefit of small dimensions and substantially reduced oil requirements. Thanks to the smaller drive unit and a redesigned sub-structure, the extruder has also become more space-saving.
Other improvements include the high-quality frequency converters built in for a more accurate regulation of screw speed and torque, and the temperature controllers. The latter are equipped with a fast self-tuning function and have an integrated on/off function as well.
Another feature is the warning light in traffic-light colours. The green light signals that the extruder is operating trouble-free, orange stands for conditions requiring the machine operator’s attention and red indicates a need for immediate intervention.
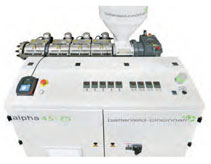
The improvements cover all models of the standardised Alpha range, available in sizes 45, 60 and 75 with either smooth or grooved feed zones.
Way forward
The Chinese firm is backed by the parent company’s more than 100 years of experience in the extrusion industry.
“In China, our main markets are infrastructure (all single-screw applications for pipes) and building/ construction (all twin-screw applications).”
Feng envisages the growth of the PO pipe market, thanks to the intensive investment in infrastructure by the government, especially in gas/water pipes as well as hot and cold water pipe markets.
“There is a vast potential in the pipe market since many residential and government buildings are updating their existing pipelines.”
Regionally, in China, he expects growth to come from north-west (Szechuan and Chongqing) apart from the traditional areas of Shandong, Guangdong and Zhejiang provinces.
He also noted that outside China, Southeast Asia and South America will provide the impetus for growth.
Nevertheless, China is an important market for battenfeld-cincinnati since it has a growing number of manufacturers who are starting to recognise the advantage of improving product quality and processes.
“In China, we will introduce the latest technology from Europe, localise more non-key parts to bring the costs down, develop machinery fit for the Chinese market and the overseas mid-market,” according to Feng, when asked about near-term plans for the Asian market.
A prime mover for promoting energy efficient technologies, battenfeld-cincinnati will continue to provide solutions that will meet the needs of its global customers.
“We have had a number of sales in China over the past few years and we expect to continue to grow as China’s demands for high output and energy efficient machinery continue to grow,” concluded Feng.
(PRA)