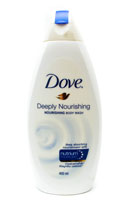
The sale of plastic extrusion products made using MuCell Extrusion technology has exceeded US$100 million in sales over a 12-month period, according to Mark Lindenfelzer, President of MuCell Extrusion. “We measure our success based on the success of our licensee customers in generating top line sales of products using our microcellular physical foaming technology. We have been closely tracking our progress toward the goal of US$100 million annual sales by our customers for several years now. A surge in sales of blow moulded automotive ductwork by our customer Kyoraku in Japan, combined with growth in the packaging industry, really pushed us over the top as we wrapped up the first half of 2014.”
MuCell Extrusion first achieved the milestone of US$10 million in annual sales of products made using its technology in 2009. The firm says the rapid acceleration its technology to achieve this ten-fold increase in only 5 years has come across many processes and applications around the globe.
According to Mark, “Many of our largest customers will not publically disclose the use of MuCell technology in achieving the type of cost savings and increased product performance that gives them a competitive advantage in their markets.”
Currently 80% of sales of products using MuCell Extrusion technology come from customers outside the packaging market in a wide range of applications including seals and gaskets, automotive ductwork, pipes, wire coating, profiles and tubing, as well as other unconventional applications, including some outside of the plastics industry.
In the packaging industry, agreements with Dow Chemical and Styron for exclusive rights to certain blown film and flat sheet extrusion foaming patents have speared headed growth in the use of the extrusion technology. Key customers in this market driving volume growth include Mondi Group (formerly Nordenia) in the blown film market, as well as Coveris (formerly PACCOR) a producer of sheet for form-fill-seal packaging applications.
Most recently, Unilever has announced the successful launch of blow moulded Dove Body Wash bottles using the technology. This new wave of packaging applications is further accelerating growth. “As our business expands into the packaging market we are seeing a paradigm shift in 2 ways: applications are more readily translated and more scalable from one market to the next and our customers are more open about the use of our technology as part of their overall corporate sustainability strategies” commented Mark.
MuCell Extrusion licenses technology and sells related equipment for the production of microcellular foam products. Applications include extrusion and extrusion blow moulding for bottles, sheet and film for consumer packaging.
MuCell Extrusion is 100% owned by Zotefoams, a world leader in cellular material technology. Using a unique manufacturing process with environmentally friendly nitrogen expansion, Zotefoams produces lightweight foams in Croydon, UK, and Kentucky, US, for diverse markets worldwide. Zotefoams also owns and licenses patented MuCell microcellular foam technology from a base in Massachusetts, US, to customers worldwide and sells T-Tubes advanced insulation systems made from its patented ZOTEK fluoropolymer foams.
The MuCell microcellular foam technology was pioneered by US firm Trexel for injection moulding technology.
(PRA)