Also, download this story from the electronic issue here
As China strengthens its “green fencing”, European countries are pressured to push for recycling effectiveness. Meanwhile, brand owners are improving their recycling efforts, by conducting further studies to push the frontiers.
China no more a dumping ground for plastic waste
With China increasingly concerned over degradation to its environment, it has implemented “green fencing” regulations to curtail the dumping of plastic waste in the country. The country, once the final destination for more than 70% of the world’s plastic waste, is strengthening its “green fencing” regulations to restrict types of plastic waste materials it will accept.
While China is the world’s largest consumer of recycled plastics, it relies heavily on imports, having imported 10.3 billion tonnes in 2012, according to research firm IHS.
Jim Glauser, speciality chemicals analyst at IHS Chemical and author of a report on plastics recycling, says, “The country has rejected shipments of waste deemed contaminated or unsuitable and officials are cracking down on hazardous materials that eventually go to Chinese landfills.”
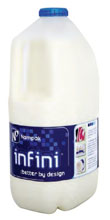
China’s Green Fencing initiative, Glauser said, has turned the global recycling industry on its head.
“Much of the plastic scraps once destined for China are now being exported elsewhere, and the global recycling equipment industry is working to expand its automation to improve waste sorting. Plastic manufacturers and producers of plastic goods are evaluating design guidelines to increase recyclability. One idea is the concept of resin markers, which would help recyclers assess contents of plastic waste to make sorting easier. China also has an opportunity to grow its domestic recycling.”
Europe steps up efforts
And now Europe, along with many other industrialised regions, such as the US, Canada, Japan, Brazil, Mexico and Australia, have to step up their recycling effectiveness for plastics, since China no longer wants to be the world’s dumping ground for plastic waste.
In 2012, European plastics recycling and energy recovery reached 61.9%. Of this, 26.3% accounts for plastics recycling and 35.6% goes to energy recovery; the remaining 38.1% ends up in landfills. From 2006-2012, said IHS, the average amount of plastics post-consumer waste generated in Europe was 25 million tonnes.
However, there are huge discrepancies in Europe with regard to plastics recycling. Seven European Union (EU) countries, plus Norway and Switzerland, have introduced landfill bans for plastic waste, while another ten EU member states landfill more than 60% of their plastic waste, according to the European Chemical Industry Council. Many Eastern European countries rely entirely on landfills to dispose of plastic waste.
In 2012, according to IHS, 82% of recycled plastics in Europe were plastic packaged products and the recovery of waste was more than 69%. In total, approximately 34% of plastic packaging waste was mechanically recycled, while 0.5% went to feedstock recycling and nearly 35% was used for energy recovery. The 5.4 million tonnes destined for energy recovery went to both incineration plants and as refuse-derived-fuel. In the same year, around 26% of total post-consumer plastic waste in Europe was collected for mechanical recycling, 0.3% went to feedstock recycling and nearly 36% went for energy recovery.
PlasticsEurope, an association of plastics manufacturers, is advocating for a ban on the landfilling of plastic waste by 2020, which would prevent nearly 10 million tonnes/year or EUR9 billion/ year of plastic waste from going into a landfill each year. Initially, the countries of key focus for the project would be the UK, Italy, Spain, France and Poland.
Since the increasing global substitution of plastics for other types of materials will keep plastic waste in the public spotlight for many years to come what will likely happen, “is that incentives must be made or more laws must be passed to stimulate higher quality recycling by extending collection and sorting services, and by keeping both recycling and energy recovery as viable alternatives to landfill.”
For this to happen in Europe and elsewhere, Glauser said, “recycling processes must improve.” This includes the collection, sorting, and processing; while plastics that cannot be sustainably recycled should be used for energy recovery rather than sent to a landfill.
Europeans to conduct recycling studies
Meanwhile in the UK, a consortium including retailer Tesco and consumer brands Nestlé and Coca-Cola, and waste management company Sita have received a Department for Environment, Food and Rural Affairs (Defra) funding to explore ways to increase the amount of flexible laminate packaging that is collected and recycled. Laminated packaging recycler Enval is also be involved in the project.
The initial study, led by LRS Consultancy, will assess the feasibility of a range of collection systems for households and commercial premises. It is estimated that more than 160,000 tonnes of flexible laminate packaging enters the UK marketplace each year, including such items as food and beverage pouches, toothpaste tubes and pet food sachets.
Over in Norway, Nofir, which runs a nationwide recycling system for fishing and fish farming industry, has organised a large European campaign to target discarded equipment from the fishing and farming industry.
Nofir’s Eco-Innovation project expands from Norway to include Europe as well as finding companies or fisherman who want to get rid of material and arranging to transport for it to Lithuania, where it can be dismantled and, in most cases, recycled. The campaign has received EUR680,000 in funding from the EU.
Brand owners in the US take charge
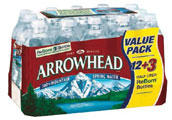
Nestlé Waters North America is rolling out its ReBorn bottles with 50% recycled PET for mineral water brands Arrowhead and Resource. The food contact grade rPET for these bottles is provided by PET recycling company CarbonLITE of Los Angeles and is produced using Vacurema bottle-to-bottle technology from Austrian machinery maker Erema.
CarbonLITE processes more than 2 billion plastic bottles collected from municipal curbside systems and deposit centres annually at its 20,000 sq m plant and supplies its rPET to PepsiCo, among other wellknown major international clients.
Erema has supplied two Vacurema Prime 2321 T systems, each designed for a capacity of 2,500 kg of material/hour, ensuring that decontamination is efficient and fast.
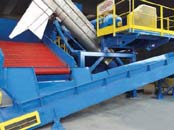
Meanwhile, CarbonLITE’s new US$60 million facility in Texas, with a capacity of 45,000 tonnes/year of rPET, will supply Nestlé’s bottling facilities near Dallas. It will be equipped with Italian machine maker Amut’s machinery.
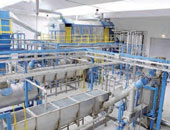
Amut says its machinery and technology will be utilised in many steps of critical areas for cleaning the PET bottle stream. The system includes the patentpending DLB-60 de-labeller for full-body shrink sleeve label-removal system and the patented PW-180/5 high friction whole bottle wash technology for cleaning the whole bottles prior to the wet grinding process.
For the final cleaning of the PET flakes, Amut has supplied its patented AX 150/5 hot flake friction washing technology machinery.
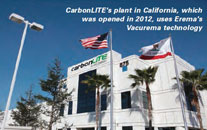
Since shrink labels represent up to 15% of the capacity of bottles in the US, Amut says its de-labeller is the best solution to solve the problem and not losing material. For food-grade purification and pelletising, it will use Erema’s technology.
Cradle-to-cradle programme
Danish brewer Carlsberg and selected global suppliers have joined forces to rethink the design and production of packaging material, to develop the next generation of packaging products that are optimised for recycling and reuse, while, at the same time, retaining or improving the quality and value.
The founding companies working together with Carlsberg in the up-cycling project include can maker Rexam; glass bottle coatings supplier Arkema; glass packaging supplier O-I; shrink wrap maker RKW; paperboard multipacks supplier MWV; and manufacturer of PET kegs for draught beer Petainer.
Earlier studies by the Ellen MacArthur Foundation and McKinsey & Co. project billions of Euros in savings from stimulating economic activity in product development, remanufacturing and refurbishment.
The companies will be using the cradle to cradle business platform for innovation and quality, with the aim of improving the quality of products so that they
- have an improved consumer quality for the user;
- pose no health risk for anyone who comes into contact with them;
- and, are of both economic and ecological benefit.
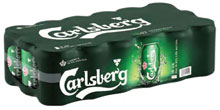
With this initiative, Carlsberg aims to have new products undergo an assessment for up-cycling potential using the cradle-to-cradle analysis, which will reveal if the products contain any chemicals or additives that would reduce the value and quality of the materials.
The targets are to include 15 partners and to have a minimum of three products certified by 2016.
Carlsberg says it is already using solutions that rely less on natural resources, such as refillable glass bottles, which in some markets are used more than 20 times, and the beverage can which is infinitely recyclable. One of the key challenges that the initiative will focus on is creating solutions that are both sustainable and appealing to the consumer.
Surmounting challenges
Part of the challenge for recyclers, is that there is an unrelenting introduction of new plastic packaging materials with unique compositions tailored to provide superior performance characteristics for specific applications, which contributes to the increasing technical complexity of plastics recycling.
Cost is also a big issue, said Glauser. “A big part of what facilitates recycling programmes is the cost of producing new materials versus recycled material costs. According to our Competitive Cost and Margin Analysis Service at IHS Chemical, in Europe, producers face some of the highest linear low-density polyethylene product costs, so the cost analysis of recycled plastic versus virgin chemical is comparable if not in favour of recycling.”
While the US relies heavily on landfills (75 to 80%), Japan disposes of more than half of its plastics waste by incineration and Western Europe uses a combination of both, including making the consumer pay for rubbish, as an incentive to recycling.
(PRA)