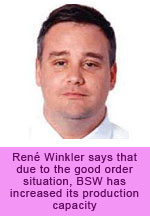
Austria-based woven bag machinery maker Bag Solutions Worldwide (BSW), a member of German machinery group of Windmöller & Hölscher (W&H), sees further growth in the Asian market. “Demand for BSW’s machines is increasing year by year in Asia Pacific and China. The two countries that have acquired the highest number of our machines are Indonesia and Thailand,” said Regional Sales Manager René Winkler, who covers sales in Asia Pacific and China.
He said that 2012 was the best year in the history of the W&H group in Asia “because it hit an order intake worth EUR100 million.”
“The close cooperation of BSW and W&H is a big benefit for all our clients, as flexible packaging is our world, while extrusion, printing and conversion are our passion,” he said.
Included in the W&H group range are woven bag processing machines; and W&H’s film processing machines (blown/cast film lines); paper converting machines, and FFS packaging systems; as well as both firms’ offerings that include flexographic and gravure printing presses and surface finishing machines.
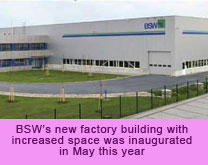
Early this year, BSW expanded its 8,000 sq m-Prostejov operations with a second factory. The new building has a 5,000 sq m floor space and 1,000 sq m office space that accommodate increased volume of assembly work, a visitor centre and a fully equipped woven sack technology centre.
The cement industry is a major consumer for the woven sacks that feature robust cross bottom valve bags made from coated PP woven fabrics. Using existing packers, they are as easy to fill as traditional paper bags, according to Winkler.
Pinch sacks made from high-quality printed and BOPP laminated woven fabrics are used for industrial and pet food packaging due to their good optical properties and unmatched durability.
Working alongside BSW, W&H has contributed key develop¬ments to the machinery side of this evolving market, adds Winkler.
The development of joining woven fabrics using hot air instead of glue has ushered in new applications, said Winkler. With laser perforation, the company has initiated the production of sophisticated woven sack structures based on stepped-end tubes.
“Both BSW and W&H complement in their work to innovating woven sack production process and outcomes,” he adds. While BSW specialises in systems for fabric manufacturing and finishing, W&H contributes its know-how in the design of converting machinery.
(PRA)