Also, download this story from the electronic issue here
An extrusion coating die designed to reduce edge bead has enabled a producer of aluminium foil and foil-laminate flexible packaging to actually eliminate edge bead, as well as reduce coat width variation by half or more. After a die for applying LDPE on an existing production line for flexible food packaging had been causing problems with die lines and leakage, Korea Aluminium replaced it with the Nordson Extrusion Dies Industries Edge Profile Control (EPC) die.
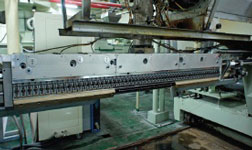
While the degree of edge bead reduction achievable with the manual EPC die depends on a number of factors, the reduction in the line was 100%, says the processor, adding that coat weight variation was reduced by 50% to 60%. An EPC die includes an external deckle as a secondary seal to prevent leakage and an internal deckle system that sets coat width and seals polymer at the die exit.
Meanwhile, Nordson Corporation has introduced a patentpending SmartGap technology for sheet dies. It uses a singlepoint adjustment mechanism that changes the lip gap while simultaneously modifying the length of the lip land to provide appropriate conditions for the newly adjusted thickness as the sheet exits the die. The lip land is the final gap in the die that forms the lip exit. By mechanically linking the adjustment of these two key process variables for the first time, the SmartGap system ensures a proper set-up of the die and takes substantial time and guesswork out of the process for achieving desired sheet properties.
The SmartGap system, available only on new dies, eliminates the extended shutdowns for changes in lip components that have often been necessary when transitioning to new job runs, reducing changeovers to less time. Also overcome are previous limitations on thickness range caused by the complexities of die modification; allowing for die gap adjustments over a range of 10.2 mm, enabling processors to run with multiple product changes per day.
(PRA)