For more download this story from the electronic issue here
On the surface, India’s triennially held plastics show, Plastindia, seems to have closed on a successful note with exhibitors praising the new venue in Gandhinagar, even though they were barely given a few months’ notice about the move from Pragati Maidan, Delhi, last year. The organiser, Plastindia Foundation, said the show had 1,600 exhibitors from 32 countries. Despite the reservations, it also confirmed that the show will return to Gandhinagar in 2018.
Venue well received but improvements needed
India’s largest plastics show, Plastindia 2015, was held in a new venue at Gandhinagar, Gujarat, from 5-10 February. Though the spanking new exhibition halls were well received, exhibitors lamented the inadequate onsite facilities like logistics, toilets, food outlets as well as labour issues in the setting up of booths while transportation to the centre and accommodation for visitors proved to be a bane.
Though Gandhinagar is Gujarat’s new capital city, it is located 30 km from Ahmedabad, the nearest city with an airport and hotels of international standards. Thus, the scarcity of taxis and private cars for hire from Ahmedabad to Gandhinagar also frustrated the transportation issue further, added to the 1 to 1.5 hour ride to the exhibition centre.

The 9th edition of the show was moved from Delhi’s Pragati Maidan, where it has been held for more than 20 years, to Gujarat last year. The reasons given were that Pragati Maidan was out-dated and lacked modern facilities. The organiser did reduce the rental for the exhibition booths “but did not offer any other benefits,” according to an exhibitor.
An official from Indian woven machinery maker Lohia Group said the exhibition halls lacked proper supply of high tension power distribution, water supply and drainage system, which is important for running live demonstrations of machinery. “The outdoor advertising was also not very impressive to attract visitors. Since the facility is new, considerations should have been made for hanging branding and fascia options, which allow the exhibitors to have better branding options,” said the official.
Meanwhile, Khushboo Doshi, of Gujarat-based extrusion machinery maker Rajoo Engineers praised the new venue but said that being "just a good venue does not ensure the success of an exhibition of this magnitude. The onus also lies with the show organisers and we feel there was much more that could have been done.”
The move was undertaken to boost the economic status of Gujarat, which also houses a majority (60%) of India’s plastics processors, as well as major Indian machinery makers for the plastics sector.
Subhash Kadakia, President of Plastindia, announced rebates on purchases of machines at the show. When asked if any of Rajoo’s customers took up on this, Khushboo said, “Many of our existing customers and new prospects planning to start their units in Gujarat have taken up the assistance.”
Plastindia claimed that the event had 35% more visitors over the 2012 show, with 200,000 visitors in total, thus making it the third largest plastics exhibition globally, after the K and Chinaplas shows.
Even so, exhibitors lamented the quality of visitors especially from overseas markets that were less impressive compared to the previous show held in Pragati Maidan. According to Khushboo, “Rajoo did receive an overwhelming response and in terms of numbers, it was more or less what we would normally get in Pragati Maidan, but many overseas visitors did not attend.
Nascent stage, hence the exposure
India does need the international exposure, given that its plastics sector is still at a fledgling stage.
According to Kadakia, "Currently, India's per capita plastic consumption is 9.7 kg/year and likely to triple over the next decade. Also, plastic consumption in 2013/14 was 10.2 million tonnes and it is likely to reach 17 million tonnes by 2016/17, with revenues of US$25 billion.”
India also exports plastics and other products worth US$7.5 billion a year, albeit, making up only 1% of the global share of the market.
With an upwardly mobile middle class of 400 million people, the country’s per capita of GDP currently well over US$1,500 is expected to double by 2020, thus pushing for further sector growths.
According to Khushboo, "The volatility in polymer prices is expected to end this year givng rise to increased processing volumes. We strongly believe the need for flexible and semi-flexible packaging will keep increasing to meet the demand of growing organised retail sectors in India. Moreover, the focus by the current government for infrastructure and agriculture, for which we have solutions now, will also drive growth.“
Lohia’s spokesperson Anvita Sarkari says, "Application of plastics in automobile, agriculture and infrastructure should drive the growth, in addition to packaging of consumer goods and pharmaceuticals.”
Industry sectors to demand better plastics
In view of the growth for better healthcare, Solvay Engineering Plastics has expanded its PEEK capacity at its Panoli plant, targeting the medical devices sector. "We expanded capacity by 25% and we are already underway to reach our target of more than 1,000 tonnes/year in the third quarter of 2015,“ said Jitender Bharihoke, Commercial Director.

The acquisition of PI Polymer, the engineering plastics business of Indian company PI Industries, in 2011 has further strengthened Solvay’s presence in India, with a facility and R&D capabilities. “Until then, we were importing our Technyl polyamides. However, we rapidly expanded and today we have almost doubled capacity and are on target to capture 15% of the Indian polyamide compound market by 2016,” stated Jitender. The company has two lines running at its Panoli plant producing 10,000 tonnes/year of PA6 and 66, while Jitender says 6.10 may be added later.
Meanwhile, in expectation of the growth of the automotive sector, Solvay is working towards developing applications in the country at its R&D centre in Gujarat, said Jitender. "Almost 60% of our business is in the automotive sector, and we work closely with OEMs for lightweighting and metal replacement applications.”
Jitender went on to say, "By 2020, India will have 5 million cars, and it will be the biggest small car market.” India also has a strong domestic segment of two-wheelers that has made the country one of Asia’s four leading automotive export nations, he explained.
The emphasis, Jitender says, will be on more thermal management and heat temperature resistance applications.
This is echoed by Ivo Lansbergen, President of DSM Engineering Plastics Asia Pacific who says the automotive industry’s worldwide standards will drive the Indian plastic sectors growth. "With new features such as turbochargers and superchargers being added to vehicles, we offer a next generation grade of Stanyl Diablo PA46 for high temperature use.“
The LED market is another area the Dutch company is focusing on. "A key challenge that lighting manufacturers need to overcome with LEDs is thermal management. While aluminium heat sinks are widely used, designers are increasingly calling for alternative materials,“ said Lansbergen. DSM has introduced its Stanyl TC to specifically answer this call, he says, adding that lighting company Osram was able to reduce the weight of the LED housing by 50% by using the TC material.
Meanwhile, Lansbergen says DSM has operated a facility in Pune since 2009 that produces compounds of thermoplastic polyesters and polyamides.

Recent innovations include the set up of a technology centre. "We believe in the Indian market and are committed, thus we have invested not only in a facility but also a technical centre to undertake innovations locally.“
The technical centre will reduce the plant’s carbon dioxide footprint by using renewable energy generated by a solar plant to meet 25% of the site’s electricity needs and water management to process waster recycling. "Very few plant operators can attest to this,“ he said, adding that the facility had recently received an environmental management award.
Rajoo’s firsts for Indian machinery sector
Occupying a space of 720 sq m, Rajoo’s booth had a gamut of machinery. In collaboration with Meaf Holland, Rajoo presented, for the first time in Asia, a monolayer sheet line with an output of 600 kg/hour from a 75 mm extruder. It also launched what it says is India’s first tilting mould thermoformer, Dispotilt.
In its collaboration with Italian firm Bausano, it has introduced India’s first WPC (wood plastics composite) extrusion machine, with a range of capacity from 200- 1,200 kg/hour to manufacture profiles and boards with 80% of wood powder.
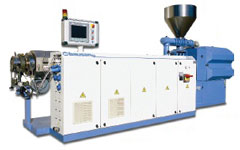
It also showcased an improved version of the five-layer Multifoil blown film line for barrier and non-barrier flexible packaging, lamination grade films and shrink films, with an output of 0.9-1.2 kg/hour/mm. A new feature is the elevated air ring from Germany that allows automatic thickness control.
Meanwhile, in its collaboration with Hosokawa Alpine it showed a patented X blown film die head with features such as: no port lines, quick purging, selfcleaning, low gauge variation and minimum bolts-tight fit for concentric parts ensuring a low melt residence time and ability to process a wide range of polymers.
Mamata boasts new converting machinery
In 2012, Mamata Machinery decided to buy out Canada-based Brampton Engineering in its blown film equipment joint venture, renaming the company Mamata Extrusion Systems. According to Apurva Kane, Senior Vice President, since then Mamata has been able to penetrate markets it was not able to before. “The affordablility factor has seen our lines taken up by not only the local market but also African countries.“
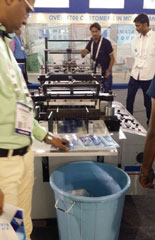
Furthermore, as India's largest manufacturer of machinery for making plastic bags and pouches Mamata is continuously evolving its converting machinery. At Plastindia, it introduced the Win centreseal pouch making machine boasting a higher productivity of 250 bags/minute, smaller footprint, no pneumatics and power usage of 1kw/hour. Since its launch, Kane said the company had sold 15 machines in Mexico and 20 in India.
Mamata has also now made improvements to the Vega 1200 Split dual draw roll bag maker, having first shown it at K2013. “It has a dual servodriven index with dual pneumatic-assisted dancers. This technology, offers the ability to process two printed bags at the same time, in two different sizes. Productivity is doubled with either two lanes for bags up to 590 mm width or a single lane bag with a width of up to 1,200 mm.“ Kane said the first machine had been sold to the US.
With the Indian packaging sector, moving at a fast speed, machinery makers have to keep pace. Thus, Mamata is working with Dow Chemical to introduce a machine for its PacXpert packaging technology, that enables the transition from larger traditional rigid containers to flexible stand-up pouches, said Kane. “Processors can save 20% of material since the packaging is of the same volume.“
Lohia ups the ante with new range
Lohia displayed its Nova series of 6 and 10 shuttle circular looms from the latest range. “High speed circular looms that were displayed covered a complete range of fabric to produce small bags to big bags to tarpaulins to geo-textiles, agro-textiles and many more. These machines have already been installed with our worldwide customers to produce better quality woven fabric at higher production speed more reliably,” said Anvita.

Also on display was its upgraded Valvomatic machine for the production of valve bags that are stitched on both sides, for cement packaging. The machine on display was producing 35 bags/minute instead of the 30 bags/minute output of previous models. “The machine has many other technical features for not only higher speed but also reducing wastages and lower manpower, thereby reducing the overall cost of production,” said Anvita.
Indian machine makers upgrade
Windsor Machines, which has blown film, pipe extrusion and injection moulding machinery, has entered the all-electric market. It displayed the Winelec 150-tonne injection machine. An official said, “We found that this was lacking in our portfolio. The model is on a four month-trial and we expect this type of machinery to take off in three to four years.“
Meanwhile, having taken over Italian machinery maker Italtech last year, Windsor was showing the KL550 dual platen injection machine, made using Italtech technology. “This is the first series to be made in India from this takeover,“ said the official, adding that the company intends to target the automotive market and build machines from 500-7,500 tonnage. Another new display was the Winpet 32L PET preform system, which is timely since the packaging market in India is on a growth path.
Ahmedabad-based Ferromatik Milacron, a part of US-based Milacron, has expanded its plant in an investment of US$20 million, to double capacity for injection/blow moulding machines, and launch an extrusion line. It also invested another US$10 million in hot runner maker Mold Masters (a subsidiary of Milacron) for expansion at its Coimbatore facility.
“Our order books are full for the next three to four months,“ said company spokesperson Neeraj Sharma, explaining the need for the increase in capacity from 1,500 to 2,000 injection/blow moulding machinery. The 55,000 sq m facility’s layout and manufacturing methods are in line with Cincinnati-based Milacron.

Also cashing in on the PET market, Milacron launched a 110-tonne preform system with post cooling, thus reducing cycle time. Another new launch is the UR70 blow moulder (from sister company Uniloy Milacron), while its entry into the extrusion market is sealed with the TC80 conical twin-screw for pipes/profiles. “It will be eight to nine months before we commercialise the blow moulder, while the extrusion line will be produced locally by middle of the year,“ said Sharma.
Meanwhile, Nissei ASB, the Indian arm of Japanese blow moulding machine maker, is further expanding its facility at Ambernath. “We have already invested US$20 million in the second phase that opened in 2013. Now, we are planning to purchase new land for a third phase. Our investments in India will total US$50 million, once we have finished,“ said CEO Kota Aoki.
At Plastindia, it introduced the ASB-12M injection blow moulder, a small machine targeted at the cosmetic and phamaceutical markets. Made in India, the machine features a vertical blow moulding method, allowing for more accuracy in preform and mould alignment.
The threads are held by the neck until ejection, while parting lines on the preform do not show up on the body of the container.
For more download this story from the electronic issue here
(PRA)