The bioplastics market is picking up a similar momentum as the traditional plastics markets, with volatility of suppliers’ activities. Meanwhile, a new bioplastic from shrimp shell is said to trump most bioplastics on the market, posing no threat to trees or competing with food supply.
Some expand, while others restrategise
A recent report by Germany's Nova Institute says that US-based manufacturer of proprietary biobased, compostable and sustainable bioplastics Cereplast has filed for protection from creditors under Chapter 11 of the US Bankruptcy. It is restrategising its operations toward traditional compounded products and recycling polyolefin and bioplastic made of diversified feedstock including algae and polylactic acid.
The company says it has taken this action to strengthen its balance sheet, clean up its capitalisation structure and gain financial flexibility as it continues to realign its operations. Cereplast reported a net loss of US$34 million against sales of US$2.1 million for the nine months that ended September 2013.
CEO Frederic Scheer said the company had taken a number of steps to improve its operations over the past few months, but added that “the lack of traction of bioplastics demand in the US, the repetitive delays in implementation of the bioplastic regulation in Europe, and especially in Italy, combined with the legal problems created by several of our lenders made clear to our Board that reorganisation was the proper path forward.”
Meanwhile in Australia, Cardia Bioplastics, the supplier of Cardia Biohybrid and Cardia Compostable resins, films, bags and custom-finished products, is expanding production to meet increasing demand for its film and bag products. It has added on three new film extrusion and bag making machines and is aiming to order a further three by end of June. Each production line is capable of producing an additional 1.5 million bags/month. It says that increased finished products capacity will enhance sales margins, as Cardia products will be made in-house.
Dr Frank Glatz, Cardia’s Managing Director, said, “The market dynamics are shifting. Over the past few years brand owners, retailers and packaging companies have commenced using bioplastic resins, films and packaging to replace conventional plastics. In parallel, Councils and waste management companies have started programmes to separate organics from landfill, using compostable bags to divert organic waste from households and industry to composting. Both developments offer growth opportunities for the Cardia Bioplastics business.”
Acquisitions/collaborations to boost market
Elsewhere, bioplastics maker Novamont has acquired 78% of Mater-Biopolymer, a subsidiary of PET resins producer Mossi & Ghisolfi (M&G), with an option to buy the remaining share capital by the end of 2016.
Under the agreement, the Patrica plant in Lazio, Italy, with 83 employees, will work exclusively for Novamont and M&G, with one line producing PET for M&G and another - already modified over the past four years using proprietary Novamont technology – will be used for production of Origo- Bi, the range of polyesters obtained from monomers partially or completely from renewable sources. These polymers are used to improve the characteristics of Mater-Bi, Novamont’s range of biodegradable and compostable bioplastics. The Patrica site will have the capacity for 100,000 tonnes/year of Origo-Bi polyesters.
Versalis, the Italian chemical subsidiary of Eni, and US-based producer of speciality chemicals from natural oils Elevance Renewable Sciences have signed an MOU to establish a strategic partnership to jointly develop and scale a new metathesis technology to produce bio-chemicals from vegetable oils.
Versalis and Elevance intend to focus on jointly developing and scaling new catalysts, leveraging the significant progress of this technology that has been already accomplished by Elevance. In addition, the partners will assess the design and construction of the first world-scale ethylene metathesisbased production that will utilise renewable oils at the Versalis Porto Marghera site. This will also take advantage of existing infrastructures and production streams. The market applications will be personal care, detergents and cleaners, bio-lubricants and oilfield chemicals.
Starting up its first commercial facility for the production of biobased succinic acid is Succinity, a joint venture between Corbion Purac and German firm BASF. The plant, located at the Corbion Purac site in Montmeló, Spain, has a capacity of 10,000 tonnes/year and is producing commercial quantities of biobased succinic acid for the global market. Succinity is also planning a second large-scale facility. The firm’s closed-loop process is based on proprietary microorganism Basfia succiniciproducens that allows for a flexible usage of different feedstocks.
Compostable shrimp shells for bioplastics
Researchers at Harvard’s Wyss Institute have developed a method to carry out large-scale manufacturing of everyday objects using a fully degradable bioplastic from chitosan, a form of chitin.
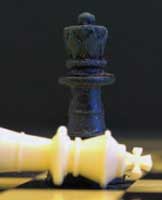
Chitin is a long-chain polysaccharide that is responsible for the hardy shells of shrimps and other crustaceans, armour-like insect cuticles, tough fungal cells walls and flexible butterfly wings.
The majority of available chitin in the world comes from discarded shrimp shells, and is either thrown away or used in fertilisers, cosmetics, or dietary supplements, for example. However, material engineers have not been able to fabricate complex 3D shapes using chitin-based materials, until now.
The researchers have fabricated large, 3D objects with complex shapes using traditional casting or injection moulding. What’s more, they say that the chitosan bioplastic breaks down when returned to the environment within about two weeks, and it releases rich nutrients that efficiently support plant growth, says the US institute.
After fully characterising in detail how factors like temperature and concentration affect the mechanical proper t ies of chi tosan on a molecular level , the researchers honed in on a method that produced a pliable liquid crystal material that was just right for use in casting and injection moulding.
Significantly, they also found a way to combat the problem of shrinkage whereby the chitosan polymer fails to maintain its original shape after the injection moulding process. Adding wood flour, a waste product from wood processing, did the trick. The material can also be modified for use in water and also easily dyed by changing the acidity of the chitosan solution. And the dyes can be collected again and reused when the material is recycled.
The next challenge for the team is to continue to refine their chitosan fabrication methods so that they can take them out of the laboratory, and move them into a commercial manufacturing facility with an industrial partner.
(PRA)