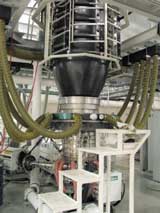
Canadian extrusion machinery maker Macro Engineering & Technology has developed and patented a new process to produce trash bags using high percentages of post-consumer materials.
With conventional methods for producing bags with high amounts of recycled material, the reclaim is normally buried in the core layer of a coextruded structure between skin layers of mostly-virgin material. The issue with this method is that defects, such as gels/pinholes, that may originate from impurities in the recycled materials of the core layer tend to migrate through all layers of the structure.
Macro says its process is to create a two-ply film by joining two films immediately after extrusion. This configuration adds strength to the overall film structure as weak spots in each layer are reinforced by the complimentary layer.
To block the film, Macro can employ two methods: The first is a conventional blown film extrusion setup where the bubble is collapsed before the melt cools (see image). This method creates a single sheet. The second is by extruding through a dual-orifice blown film die and having the two films join which form a collapsed tube.
Macro has tested blends of post-consumer recycled (PCR) materials with virgin resins as well as structures comprised of 100% in-house scrap. The tests found that both tear strength and tensile strength were consistently better, by 25% over a single layer film structure. The technology will allow a range of 0.5% to 100% reclaimed plastic material to make up the final film structure and is best suited for industrial applications that utilise thicker gauges.
Macro has begun to offer extrusion machinery, both new and retrofit. Retrofit projects are especially suitable for film manufacturers with low ceiling heights as the requirement to block the film is conducive to shorter towers.
(PRA)