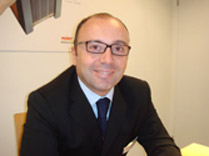
Canadian injection moulding machine and hot runner maker Husky Injection Molding says it boasts a complete suite of hot runner and controller products and services to support mould makers. To emphasise how important the hot runner business is for Husky, it has 250 people supporting the unit; of a total of 800 customer support personnel. “We have the strongest service network in the world,” claimed Gerardo Chiaia, President of Hot Runners, speaking at the Media Day event in Shanghai.
The firm reinvigorated the hot runner business in 2012 and, according to Chiaia, put together a complete team to ensure “we have a team and resources to focus on the main hot runner sectors of beverage packaging (closures), medical, consumer electronics and automotive.”
Hence, its Chinaplas booth is themed on hot runner and controller technology focusing on three main areas: hot runner thermal uniformity; precise temperature control and synchronised gate opening and closing.
It is showing the following new products:
- Ultra Side Gate hot rummer -- which it is reintroducing on account of its simplicity, elimination for the need of cold runners, increase in productivity and lower energy and scrap
- UltraSync-E servo valve gate system – it allows for 100% repeatability of valve stem movement and valve stem position; higher quality parts; 20% reduction of scrap
- Unify manifold system – a simple one-step installation of hot runner manifold, the main feature being that there is no need to preheat the system for installation
- Altanium Matrix2 temperature control -- with new operator interface and features. Building on Delta3 launch in 2013, it allows for flexibility with a modular design up to 26 configuration and can be integrated with UltraSync-E
Chiaia said, “2013 was a good year for the hot runner business. We are growing and will continue to grow in Asia and in the global market.”
Coming soon is a new valve gate solution, which purportedly “makes gate vestige disappear”, according to Chiaia.
Meanwhile, the HPP (HyCAP High Performance Package) system for high output beverage closure manufacturing shown at Chinaplas 2012, which was touted as the world’s fastest, has been redesigned to suit market needs.
At Chinaplas 2012, it was shown producing a 1.2 g 29/25 lightweight water closure at a 1.85 second cycle using a 72-cavity KTW beverage closure mould.
“Based on the response, we realised that high volume is not for all producers. We now offer the system in 72 and 48 cavities and for making 22-38 mm closure sizes.” With the new design, the firm has sold 30 units to closure moulders since 2012.
(PRA)