Industry players have one ultimate goal, which is to expand to the world market. With this in mind, global machinery player Davis-Standard is harnessing efforts on its “The Global Advantage™” philosophy. Over the last few years, the firm has centred on its globalisation and transformation efforts. It is continuing with the global expansion trend, through its "The Global Advantage™" initiative, with the expansion of its manufacturing capabilities in China and ongoing development efforts for products to address the needs of the Chinese and Asian markets.
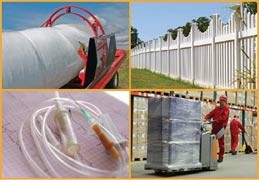
The Asia Pacific region, home to 60% of the world's population (according to the United Nations Population Fund or UNFPA), has a strong consumer base as well as industrial muscle. A cross-section of industries are being buoyed up by simply feeding and meeting the region’s consumer demands.
Furthermore, the region has China and India, the world’s most populous countries and undoubtedly major revenue feeders for the global market.
Ergo, the region is a befitting “home plate” for Davis-Standard’s forward moves. A leading manufacturer of extrusion and converting technology systems, Davis-Standard has anchored 30% of its business in the Asia Pacific region. The firm has also been expanding its manufacturing capabilities and after sales markets.
It selected China as its centre of regional expansion, starting off with the set-up of the 4,300 sq m-facility in Suzhou in 2012. The facility, which also produces Super Blue and Euro Blue extruders, was established to render sales, technical support, including R&D capabilities for customer trials; and aftermarket services. The latter encompass equipment upgrades such as total line and process control upgrades, feedscrew replacement and rebuilding, gear case retrofitting and others.
Bolstering service delivery for the region’s customers, Davis-Standard added on and recently opened a spare parts and service centre at its Suzhou facility. The new branch features a vast inventory of high usage maintenance items; shipment capabilities within 24 hours of order for stock inventory; local language support and, acceptance of payment in the Chinese currency RMB.
To move forward in Asia, last year, Davis-Standard inked a deal with China’s extrusion machinery maker Guangdong Jinming Machinery to sell Davis-Standard blown film lines in the Asian markets. Conversely, Davis-Standard has become the exclusive distributor of Jinming’s blown film lines in Europe, Africa, Australia/New Zealand, and North and South Americas.
Davis-Standard says that the tie-up with Jinming has spawned a one-stop shop convenience for its seven-plus-layer blown film lines that feature precision engineering to support wide and high-speed blown film processes, thus allowing for a wider range of top-notch machinery, service and support in Asia.
Getting a grip on the Global Advantage
Meanwhile, investments and ongoing expansion of service capabilities in the region are the firm’s precursor in line with its trademarked “The Global Advantage™” grip, and as furthering its lead amongst its league. Backing the philosophy is the firm’s large global base with 40,000 installations, six facilities, three R&D centres, and 14 sales offices to boot; and sales of over US$300 million in 2013.
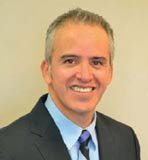
To highlight its global reach, Davis-Standard has also launched a new website (www.davisstandard. com), which gives its online visitors the “Global Advantage” feel.
“The new easy-to-navigate website reflects our global commitment and vision as one of the industry’s largest and most diverse suppliers of extrusion and converting technology,” says Carlos Flores, Davis-Standard’s Global Vice-President of Marketing. “It has an improved look and site visitors will be able to envision how we can serve them in terms of current products, new technology and global commerce.”
He adds, “The site is geared towards providing a broad range of essential information in a succinct format that shows the best we have to offer.”
The website carries information on Davis- Standard’s 16 product areas, innovation updates such as the new dsX product line, and service capabilities; global contact information; and features product videos and images.
A world-scale initiative
The Pawcatuck-headquartered firm has over ten extrusion/converting product lines to support manufacturing applications and customers within every major industry. Over the past several years, the company says it has been successful in consistently gaining global market share in the segments of packaging, automotive, medical, construction, technical and speciality as well as green market applications. It has also experienced substantial growth in new markets.
The company has four manufacturing and technical facilities in the US, as well as subsidiaries with facilities in Germany, the UK, and, as earlier mentioned, in China.
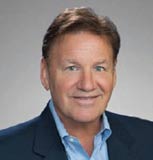
Following consolidation of its global sales and marketing groups, the 900-employee firm conducted an internal review to evaluate and improve business processes worldwide. The result is a globally-focused organisation that is committed to manufacturing investments to provide more localised support for customers as well as to make customers aware of the benefits of Davis-Standard’s quality, customer service and regional expansion.
“We have become a united company with a clear value proposition for our customers,” said CEO Bob Preston. He discloses that Davis- Standard is increasing its geographical and manufacturing footprint, while maintaining its strong presence in traditional markets, such as the US and Europe.
Three primary areas where customers will benefit from its Global Advantage initiative are identified in the areas of products, marketing and technology as well as global commerce.
With products, Davis-Standard will continue to develop global manufacturing capabilities, product consistency and quality and manufacturing excellence, according to Preston.
In the area of commerce, Preston adds that the firm will “pursue unparalleled service, application development, local fulfillment execution, and parts and aftermarket support.”
He goes on to say that along with these tangibles, an essential part of Davis-Standard’s strategy includes forming partnerships with top companies and making “smart investments that build upon best-in-class market leadership.”
For the marketing and technology segment, Davis-Standard will expand into new markets, add on additional industry segment support, and continue developing new products and applications.
“This means we need to be the best in service, support and training and delivery. As a global company with a talented team and an excellent product portfolio, we are confident in our ability to transform our business and that of our customers,” states Preston.
New dsX s-tretch cast film line
In line with its strategy to launch new products, Davis-Standard has introduced the dsX s-tretch cast film extrusion line, which is touted as the first in-line pre-stretch system for mono-oriented films, thus providing converters with a costeffective option to meet the growing demand of today's global shipping market.
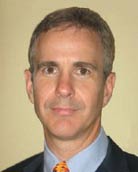
The system is available in three, five and seven-layer cast film options, which utilise the firm’s proprietary and patented technologies to produce film as thin as 6 microns at speeds up to 550-1,000 m/minute.
The pre-configured 2 m-line is said to be easy to install and operate. Film producers can choose between two and three-inch thin core and innovative coreless options for reduced material and disposable costs. Furthermore, the unique auxiliary lay-on roll also produces rolls with high-quality outer (tailless) wraps.
Thus, engineered to produce thinner and stronger films at higher speeds, the dsX s-tretch film line allows output to be maximised, pushes for an optimum level of energy efficiency and delivers a faster return on investment (ROI).
The system runs thin films at high speeds because it produces a thick film, then orients it three times in the machine direction. This allows the quick production of a high quality product with exceptional efficiency, according to the machine manufacturer.
The three-roll, machine direction orientation (MDO) unit and winder stretches the film in two stages. A relaxation mode follows in conjunction with a virtual zero-tension winder to eliminate internal stresses in the film. Running at a maximum speed, it can produce four rolls every 20 seconds, which is in essence 12 cores/minute or 720 cores/hour.
Steve Post, Davis-Standard’s Vice-President of Cast Film, confirms the line’s significant benefits, which sum up to helping processors maximise productivity and profitability.
“The line is ideal for delivering value to converters looking to upgrade their production lines and capitalise on a growing market need; for distributors looking to drive costs out of their process, enhance their efficiency and protect product through delivery; and for manufacturers looking to minimise losses from damaged goods through the supply chain,” he explains.
Because of extensive pre-engineering for multi-layer cast film manufacturing, Davis- Standard says it can deliver and commission a complete dsX s-tretch cast film extrusion line in accordance to user specifications in as little as six months, thus allowing for a competitive lead time.
Family of dsX lines
The dsX s-tretch cast film line represents the latest development in a series of new innovations in the dsX family product group.
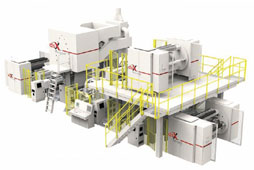
Last year, the firm launched the dsX flex-pack extrusion coating line. The line offers converters and packaging printers a competitively-priced system for a variety of applications, including snack bags, condiment packs, stand-up pouches and personal care packaging.
This flexible packaging line includes an unwinder, corona treaters, extrusion laminator, gravure primer coater dryer, pull roll with nip, electrically-heated winder, air-cooled Davis- Standard extruder with advanced feedscrew design and Siemens drives and controls.
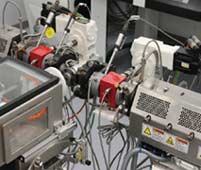
The line is available in two versions to accommodate almost any plant: one is a longer line with the auxiliary unwinder placed close to the floor; the other raises the auxiliary unwinder to a position just atop the winder to shorten both the length of the line and the path of the auxiliary web to the laminator.
Standard on the dsX flex-pack is an advanced computer technology that includes the APC (automatic profile control), which continually adjusts the product profile for optimum performance, and a DS5 computer that allows for remote access to the line for troubleshooting and updating over a secure internet connection. Performance data is exportable to factory systems for SPC and other analytical management tools.
Reiterating what Post emphasised above with the new dsX s-tretch cast film extrusion line, CEO Preston says that the overall focus of the extrusion technology is to increase productivity and profitability for customers worldwide.
Innovating medical tubing
Innovation-driven, Davis-Standard raised the bar to offer yet another technology geared towards the healthcare sector last year. The dsX med-tube medical tubing system is a variation of Davis- Standard’s broadly-used medical tubing systems.
This innovation is said to deliver value and versatility in one powerful, space-saving package.

The compact line, thus, ensures a smaller footprint for clean rooms. It is also featurepacked, including language-specific control and an advantage for fast delivery anywhere in the world, says the firm.
According to Wendell Whipple, Davis- Standard’s Vice-President of Pipe Profile and Tubing Group, among the line’s primary design advantages is a co-extruder arrangement for processing materials ranging from polypropylene (PP) to fluorinated ethylene polypropylene (FEP). The line includes a melt pump on each extruder for processing thermoplastic polyurethane (TPU), nylons and other medical-grade materials. What’s more, the new system is a cost-effective, clean room-oriented platform that is supported by regional engineering and service teams.
“With the constant changes in the medical marketplace, it is important that the most current technology be accessible to customers around the globe. This line hits the mark in terms of size, capabilities and return on investment,” Whipple explains.
Customers can run trials on the new line at Davis-Standard’s Suzhou facility. Meanwhile, it also offers a medical tubing R&D line at its Pawcatuck Technical Centre in Connecticut, US. The systems are available for single lumen, multi-lumen, IV catheter, corrugated drainage, integrated bump tubing and multi-layer tubing.
The firm says that the lines are the latest developments in a series of new innovations designed to help customers be more competitive, by optimising their ability to respond to the market and ever changing needs, which is appropriate and timely for the growing markets of China and Asia.
(PRA)