Packaging
High barrier MDO-PE/PE laminate for recyclable packaging
To address the growing demand for recyclable packaging options, US materials firm ExxonMobil says it has successfully collaborated with Hosokawa Alpine, Henkel, Nordmeccanica Group and Univel to develop a high-barrier, recyclable MDO-PE//PE laminate. This advanced packaging solution is engineered to provide excellent barrier properties against oxygen and moisture, and targeted at a range of food products, ensuring optimal product freshness and protection.
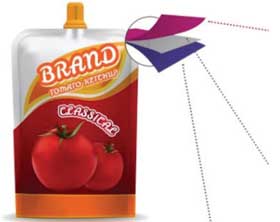
The duplex MDO-PE//PE laminate was produced from a high-barrier PE sealant film and MDO-PE printing web. The MDO-PE printing web incorporated ExxonMobil HDPE HD7165L that was specifically designed to produce MDO-PE films. The MDO-PE film was produced on machine supplier Hosokawa Alpine’s five-layer blown film line with inline MDO.
The blown PE sealant film was produced using ExxonMobil’s performance PE resins such as Exceed S, Enable and Exceed. Material supplier Evonik’s TEGOMER 6810, an organo-modified siloxane, was used to help control the coefficient of friction (COF).
Two thin barrier coatings (BC) were then applied on the blown PE sealant film to help deliver outstanding barrier properties: the first layer contains vacuum-metallised aluminium, while the second layer contains 1 gsm of technology firm Henkel’s newly developed barrier coating Loctite LIOFOL BC 1582 RE.
Both functional layers were applied using Nordmeccanica Group's Vacuum & Coating machinery (Nordmet 12F Plus/Super Combi 5000). The MDO-PE film was printed by Univel.
The combination of metallisation and barrier coating to produce a very high PE-content laminate provides ultra-high oxygen barrier properties (similar to aluminium foil3) and excellent moisture barrier properties.
The oxygen-transmission rate (OTR) of the PE-based film was almost two magnitudes lower than the PETmet-based film when measured at 0% relative humidity at room temperature, whereas water vapour transmission rate (WVTR) of both structure was very similar.
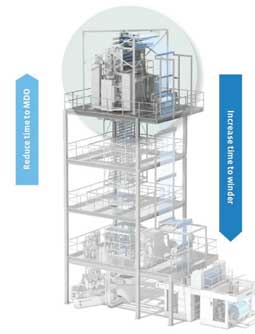
The new solution not only meets the functional requirements for a wide range of food packaging applications, from dry goods to liquids, but also offers outstanding stiffness and clarity. This makes it a viable alternative to traditional materials such as PET and BOPP. Additionally, the solution addresses the challenge of maintaining barrier properties while ensuring ease of recyclability, often a limiting factor in conventional packaging materials.
Meanwhile, German machinery maker Reifenhäuser Blown Film has also showcased what it says is the “world’s first’ 18-micron MDO-PE film”. It claims to reduce the thickness of previous films by 25% and enable companies to transition into fully recyclable, low-carbon mono-material flexibles.
The film has been produced on Reifenhäuser EVO blown film lines using the patented EVO Ultra Stretch MDO technology and has been developed and tested for practical suitability in collaboration with raw material manufacturer LG Chem and printing specialist Bobst.
Cost-effective solution as an alternative to ionomer vacuum skin packaging
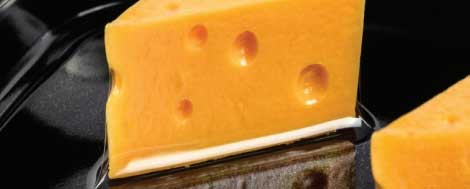
Elsewhere, ExxonMobil has collaborated with Brazilian packaging converter Videplast to develop a vacuum skin packaging (VSP) solution to replace an existing resin that does not contain ionomers, thereby reducing film thickness for food packaging applications.
VSP is a type of packaging where a product is placed on a piece of tray (plastic or cardboard) and a thin barrier film is softened by heat and draped over the product on the tray. Vacuum is applied to ensure the film will cover the entire surface of a product/tray, removing as much air inside the package as possible.
Utilising ExxonMobil’s Exceed XP 7052ML performance PE, the new solution hopes to meet market demands for high-performance, cost-effective packaging that provides protection from food spoilage, leakage, and contamination and extends the shelf life of perishable goods by removing air and providing a tight seal.
The process involves ‘optimal thermoformability’ and a high oxygen barrier, aiming for effective vacuum sealing.
The solution is said to be ideal for packaging small portions of meat, cheese, fish, seafood, and other products requiring high-performance and visually appealing packaging solutions.
Reusable PET packaging for cosmetic brands
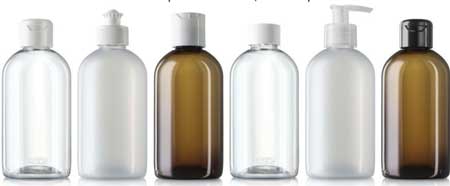
Together with packaging and recycling specialist Alpla, start-up Zerooo SEA ME has developed a standardised solution for cosmetics and care products and are now producing reusable PET packaging for bathrooms and kitchens. From September, the first brands will be presenting shampoo, shower gel, detergent, body lotion and dental care products in 300-ml PET bottles. This reusable and fully recyclable plastic packaging is available in three colours and is suitable for all caps. A laserengraved 2D data matrix code provides information on the contents of each bottle and its circulation.
Zerooo aims to create reusable packaging that fosters the circular economy in the cosmetics industry. The system from the German start-up SEA ME is said to offer brand manufacturers safe, affordable and sustainable PET bottles, in addition to glass bottles, for the first time. stands for reusable packaging that fosters the circular economy in the cosmetics industry. The reusable PET bottle is available in clear, milky white and brown versions.
The company states it has created a fully recyclable solution in collaboration with Alpla and ten brand partners. It adds that the reusable PET bottle can be used as a shatterproof alternative for toiletries in the shower, and further formats are planned.
From September, the first manufacturers in Germany will present cosmetics and care products in PET containers from the Zerooo reusable system, with Austria following suit in October. In addition to SEA ME’s own brand, these include sodasan, i+m Naturkosmetik, Speick, Denttabs, 4 people who care and Aveo from Müller.
Each Zerooo reusable PET bottle has a laserengraved 2D data matrix code – the zerooo ID – which provides information about the content and circulation history.
“The digital labelling enables transparency and ensures the quality of the bottles. By combining it with the information from the label, it can also be complemented with further product data,” explains Jörg Schwärzler, senior technology manager at Alpla. The reusable PET bottle is reportedly compatible with all automatic return systems, and at the end of their life cycle, the bottles and caps are sorted and recycled.
Alpla says it is promoting closed ‘bottle-to-bottle’ cycles with its own plants, and the Zerooo reusable PET bottle was developed with the SEA ME team at Alpla’s in-house design centre, at the company’s headquarters in Hard, Germany.
(PRA)SUBSCRIBE to Get the Latest Updates from PRA Click Here»