Expansions: BASF inaugurates new plant for alkyl ethanolamines in Antwerp; Covestro to build TPU development centre in China
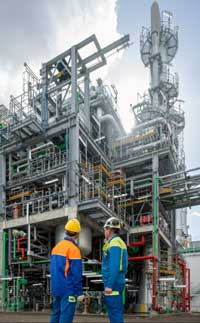
German chemical firm BASF has inaugurated a new world-scale production plant for alkyl ethanolamines at its Vsite in Antwerp, Belgium. This new investment will increase the company’s global annual production capacity for alkyl ethanolamines, including dimethyl ethanolamine (DMEOA) and methyl diethanolamine (MDEOA), by nearly 30% to over 140,000 tonnes/year. The new plant is an important part of the BASF production network for this portfolio at the company’s sites in Ludwigshafen, Germany; Antwerp, Belgium; Geismar, Louisiana; and Nanjing, China.
The versatile alkyl ethanolamines are mainly used as precursors for gas treatment chemicals, for flocculants applied in water treatment and as binders between pigments and resins in the coatings industry. Other applications include fabric softeners, additives for metalworking fluids and polyurethanes.
With approximately 300 different amines, BASF says it has the world’s most diverse portfolio of this type of chemical intermediates. Along with alkyl-, alkanol- and alkoxyalkylamines, the company offers heterocyclic and aromatic as well as specialty amines.
BASF’s portfolio also includes an expanding range of chiral amines, known for their high optical and chemical purity. The versatile products are used mainly to manufacture process chemicals, pharmaceuticals and crop protection products, as well as cosmetic products and detergents. They also serve to produce coatings, special plastics, composites and special fibres.
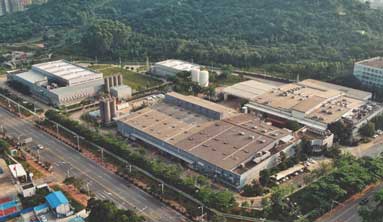
Meanwhile, compatriot German firm Covestro says it will start the construction of a new Thermoplastic Polyurethanes (TPU) APAC application development (AD) Center in Guangzhou in South China. It is the second investment announcement for TPU in quick succession: Just last year the company announced and started to build its largest TPU plant in the nearby coastal city of Zhuhai.
Covestro says the centre will be designed to integrate technical acumen with innovative solutions and tailored services in key applications including films (PPF), specialty cables, consumer electronics, footwear and further extrusion and injection applications.
Construction is set to begin in late 2024, with the facility expected to become operational in 2025. The centre will be outfitted with advanced equipment to address complex market demands and leverage local resources and networks to streamline talent and administrative management.
“Establishing this new application development centre in Guangzhou is a strategically important move for us to jointly with our customers leverage on the vibrant Asia-Pacific and especially the Chinese market. The centre will also contribute to developing more sustainable TPU solutions, underscoring our dedication to innovation that benefits our esteemed customers and partners,” said Dr. Andrea Maier-Richter, EVP and Global Head of TPU at Covestro. “Together with the ongoing investment in our largest global TPU production site in Zhuhai, we will soon run two powerful engines in two major cities. This highlights our company’s ongoing commitment to growth and its commitment to the innovative capabilities of TPU in particular.”
With the existing regional R&D centre in Changhua, the ongoing construction of the largest global TPU production site in Zhuhai and the upcoming APAC application development centre in Guangzhou, the collaborative and complementary strengths from the three sites are expected to drive even more powerful regional synergies.
Covestro adds it is committed to offering sustainable and circular solutions that align with its long-term goals. Its Desmopan CQ TPU portfolio utilises alternative raw materials such as feedstocks from waste or biomass, attributed via mass balancing.
The company as a whole furthermore aims to become fully circular and aims at becoming operationally climate neutrality by 2035, striving to utilise only renewable energy for its operations by then. This lowers the carbon footprint of products like TPU even further.
(PRA)SUBSCRIBE to Get the Latest Updates from PRA Click Here»