Thermoplastic Elastomers: TPEs headed towards sustainability
With the current emphasis on sustainability, manufacturers of thermoplastic elastomers (TPEs) are innovating TPEs with recycled materials content.
Teknor Apex launches TPVs with up to 40% recycled content
US compounder Teknor Apex has introduced its Sarlink thermoplastic vulcanisates (TPVs) with up to 40% recycled material content. The TPVs, targeted at automotive applications requiring elasticity and long-term performance, are promoted as a recyclable, light-weight alternative to EPDM rubber.
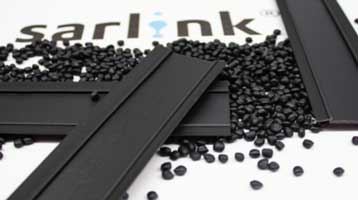
The latest series, Sarlink RX 3100B, was developed to help automotive brands achieve sustainability targets, by incorporating up to 40% post-industrial recyclate, depending on the hardness. These multi-purpose TPVs are suitable for injection moulding, extrusion, overmoulding and co-extrusion with PP or other TPEs.
For these high-durometer grades, applications include the backbone or carrier for extruded seals, like in glass run channels, or boots, bellows, and other under-the-hood components.
The two grades, an 84 Shore A and 94 Shore A, are based on the existing Sarlink 3100 Series technology, but contain 25% and 40% recycled content, respectively.
The firm says the materials process and perform similarly to their virgin counterparts yet offer sustainability benefits, which is ideal for OEMs looking to reach aggressive targets around the use of sustainable material content in vehicles.
Sarlink RX 3100B TPVs are pre-coloured black and can still be recycled in process or at the end of the product’s life cycle.
The use of PIR content versus Post-Consumer Recycled (PCR) content derived from household waste, provides for a more controlled and consistent raw material stream that can be used in extrusion-grade TPVs without issue, adds Teknor Apex.
It says it also treats recycled feedstocks like prime raw materials, and they are subject to the same quality assurance testing and must meet relevant specifications for use.
Scott Nakon, Global Automotive Market Manager, adds, “Our ongoing projects include new sustainable raw materials streams such as recycled and bio-based content, as well as carbon negative additives. Also, we plan to introduce new thermoplastic elastomers with up to 65% post-consumer recycled content later this year, as well as expand the Recyclon portfolio of recycled polyamide solutions.”
KRAIBURG TPE’s new TPE series targeted at Asia Pacific market
Elsewhere, German TPE manufacturer KRAIBURG TPE says its Thermolast R-RC/FC/PCR/AP series, with 9-35% PCR content (hardness-dependent), is designed for the Asia Pacific market. It is targeted at interdental brush and other dental tooling applications.
Using cutting-edge materials such as TPEs from the bristles to the handle ensures that the design and functionality required for interdental brushes are met, it adds.
The TPE series is offered in a wide hardness range of 30-90 Shore A, and allows for processing via multi-component injection moulding, plus good adhesion to PP, among other benefits.
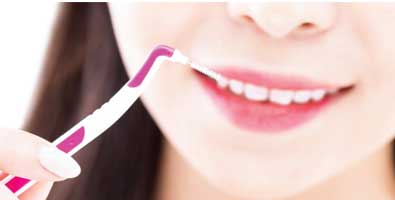
The series offers features and properties to achieve design and functionality outcomes for interdental brushes, particularly grip, handle, and tip cover applications.
Plus, it allows for the customisation of a wide range of surfaces, from soft-touch and smooth or silky feel to high surface friction, depending on the design requirement. The series' exceptional anti-slip feature makes it ideal for applications requiring an ergonomic grip and easy manoeuvring.
The compound series also conforms with REACH SHVC and RoHS, ensuring that the material is free of restricted chemical or hazardous substances, as required by European regulations. The series also meets food contact regulatory criteria including (FDA) CFR21.
Available in both natural and translucent colours, the series also offers precolouration options, for customisation in a variety of hues for a vibrant and appealing look of the products.
Besides interdental brush applications, KRAIBURG TPE’s recent sustainability innovations include a series of material solutions specially developed for automotive, consumer, consumer electronics, wearables and industry applications.
Comprising up to 48% PCR and 50% PIR content, the material complies with multiple global standards such as FDA raw material compliance, RoHS and REACH SVHC requirements.
KRAIBURG TPE says it also provides customers with product carbon footprint values.
Hexpol/Polykemi tie-up for sustainable consumer product project
Swedish compounders Hexpol TPE and Polykemi have collaborated on a 2K sustainable development project that reduced the product carbon footprint for consumer products.
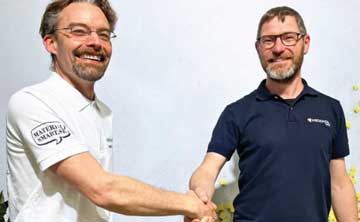
Making a material selection can be a complicated task when designing consumer products. There are many properties to balance, and the choice is even more complex when including eco-design principles. Selecting two materials for a 2K part is not doubling the difficulty; it is squared. To help with this decision, Hexpol TPE and Polykemi teamed up to enable combinations based on properties and sustainability targets.
Hexpol TPE and Polykemi have done work in the field of sustainability, allowing them to provide cradle-to-gate Product Carbon Footprints (PCF) and calculate the Global Warming Potential (GWP) per kg of material.
The PCF data shows that switching from a combination using fossil-based ABS from Polykemi, overmoulded with a fossil-based TPE from Hexpol TPE, to a recycled PP and TPE with bio-circular attributed content, can give a 77% reduction in CO2e. This combination can also bring advantages when considering end-of-life and recycling compatibility.
Combinations using mechanically recycled ABS with bio-circular attributed TPE were also tested, which gave a 57% reduction in CO2e compared to the fully fossil-based equivalents. The TPE is bio-circular attributed via the mass balance approach using 2nd generation feedstocks.
Avient launches bioderived healthcare solution
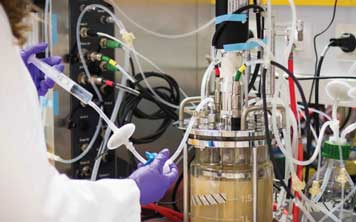
Avient Corporation has announced the availability of its newest bio-derived healthcare solution, Versaflex HC Bio TPE. Developed as a more sustainable alternative for biopharmaceutical tubing, the initial Versaflex HC Bio BT218 grade is formulated with nearly 40% firstgeneration biomass content, resulting in a lower carbon footprint than traditional alternatives.
The 71 Shore A formulation provides critical application performance such as weldability, kink resistance, and tensile strength comparable to leading medical tubing materials, including silicone and standard TPEs, says the US firm.
In contrast, the bio-derived grade offers greenhouse gas emissions at 2.35 kg CO2e / kg product, a nearly 25% lower cradle-to-gate product carbon footprint (PCF) than Avient’s standard Versaflex HC BT218 grade.
Avient’s PCF calculation method follows the ISO 14067:2018 standard and is certified by TÜV Rheinland, it adds.
Certified for USP Class VI and ISO 10993, the new Versaflex HC BIO BT218 grade is manufactured in the US with global commercial availability
(PRA)
Subscribe to Get the Latest Updates from PRA Please click here
©2023 Plastics and Rubber Asia. All rights reserved.
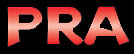
©2023 Plastics and Rubber Asia. All rights reserved.
Home Terms & Conditions Privacy Policy Webmail Site Map About Us