Bioplastics from food wastes: from potatoes to tomatoes
Biobased polymers made from low to zero-value food products and organic wastes are being praised for their viability and sustainability in achieving circularity of packaging materials, according to Angelica Buan in this report.
There are various materials being explored in order to develop environmentally friendly alternatives to plastics. Using food and organic waste as feedstock for bioplastics is one of the most popular and sustainable methods. This allows the use of waste streams that would otherwise wind up in landfills or end up being incinerated.
According to the World Bank study, What a Waste 2.0, solid waste management is crucial for sustainable, healthy, and inclusive cities and communities, but it is frequently disregarded, especially in low-income countries. While recycling and composting recover more than one-third of waste in high-income nations, just 4% of this waste is recycled
Thus, converting food and organic wastes into valuable resources can assist to reduce waste generation, laying the groundwork for developing a circular economy.
Generations of feedstocks
Food and organic waste are derived from renewable sources such as agricultural products, food processing wastes, and organic materials that have been discarded. As opposed to fossil-based plastics, bioplastics contribute to a more sustainable and circular economy by utilising easily available and renewable resources.
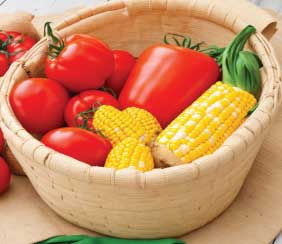
Furthermore, biomass-derived polymers have the ability to biodegrade under the right conditions. This means that when disposed of in suitable environments, such as industrial composting facilities or natural ecosystems containing microbes, they can degrade into harmless byproducts such as water, carbon dioxide, and organic matter.
That said, by utilising low to zero-value waste materials for bioplastic synthesis, waste management issues can be addressed too, reducing greenhouse gas (GHG) emissions, saving resources, and supporting the ethical transition to more sustainable plastic alternatives.
There are four generations of feedstocks used for manufacturing biobased materials, according to Deloitte in its report, The Future of Materials
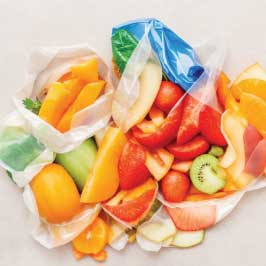
Corn, sugarcane, and soybeans are examples of first-generation feedstocks. These are frequently utilised in the production of biofuels and bioplastics. Switchgrass, algae, and agricultural waste are examples of secondgeneration feedstocks that are frequently employed in packaging applications.
Microorganisms such as bacteria, yeast, and fungi are examples of thirdgeneration feedstocks. that can be used to make oils for food, cosmetics, and biofuels.
Fourth-generation feedstocks include those based on synthetic biology that are used to create and engineer organisms that produce specified materials or chemicals. These can be used to make high-value compounds for fragrances, flavours, and pharmaceuticals.
Maize residue to renewable material
Bio-based products are produced by extracting natural feedstocks or inputs from plants or other organic sources, such as starch, cellulose, and proteins, and then processing them through various biological and chemical reactions. These materials are subsequently processed into fibres, films, and resins using techniques including extrusion, casting, and moulding, according to Deloitte.
US chemical firm Dow and clean energy producer New Energy Blue have chosen corn as a suitable source in their collaboration to develop renewable plastic polymers.The companies formed a long-term supply arrangement in North America where New Energy Blue will produce bio-based ethylene from renewable agricultural residues.
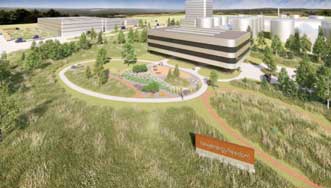
Dow expects to purchase this bio-based ethylene, which will be used in recyclable applications such as transportation, footwear, and packaging.
This collaboration is being billed as the first in North America to produce plastic raw materials from corn stover (stalks and leaves). This is also Dow's first North American deal to use agricultural waste for plastic manufacture.
Under the terms of the agreement, Dow is supporting the design of New Energy Freedom, a new facility in Mason City, Iowa, that will process 275 kilotonnes/year of corn stover and produce commercial volumes of secondgeneration ethanol and clean lignin.
Almost half of the ethanol produced will be converted into bio-based ethylene feedstock for Dow products. This deal also provides Dow with similar commercial supply alternatives for the next four New Energy Blue projects, allowing the latter to scale its production while also assisting farmers by providing a steady market for agricultural residues.
The five projects are intended to displace about 1 million tonnes/year of GHG emissions and allow Dow to increase its usage of renewable, recyclable materials as well as contributing to the reduction of agricultural carbon emissions from rotting corn stover if not used.
Good potato innovation
Rising consumer demand for biodegradable and ecologically sound packaging materials, as well as a growing emphasis on sustainable development and reducing plastic waste, has fuelled the expansion of biobased plastics.
According to market research firm SkyQuest, the starch-based bioplastics market will be worth more than US$23.8 billion by 2030, growing at a CAGR of 14.1% from 2023.
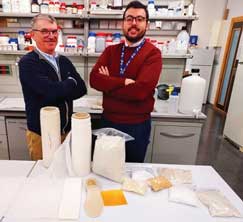
Starch-rich potato, like cassava, a prevalent ingredient in the production of a variety of bioplastic materials, is showing potential as a bioplastic feedstock.
The University of Alicante's Waste, Energy, Environment, and Nanotechnology (REMAN) research group has developed a method for producing a water-soluble plastic material based on potato starch, which will soon be available on the market via the UA technology-based company, Solublion, linked to the Alicante Science Park.
According to Professor of Chemical Engineering, Ignacio Martin Gullón, the material is both compostable and biodegradable, and is appropriate for usage as a flexible film, preferably in bags and packaging.
The plastic developed by the REMAN group is said to be stable and has a low migration rate. Gullón stated that these solutions are intended for use as direct alternatives for conventional packaging materials and single-use plastics.
The research group's formulations require the starch to be gelatinised and plasticised in the presence of plasticisers, often water and another plasticiser with a higher boiling point.
Plasticised starch, surrounded by plasticiser molecules, has a significant tendency to retrograde, which means it partially returns its previous ordered structure, resulting in decrease in properties. However, with the technology developed by the group, this migration is substantially avoided, increasing the useful life of these materials without compromising their mechanical qualities, biodegradability, compostability, or water solubility.
(PRA)
Subscribe to Get the Latest Updates from PRA Please click here
©2023 Plastics and Rubber Asia. All rights reserved.
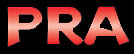
©2023 Plastics and Rubber Asia. All rights reserved.
Home Terms & Conditions Privacy Policy Webmail Site Map About Us