PRA Chinese
Rubber Journal Asia Injection Moulding Asia Energy, Oil & Gas Asia
VISIT OUR OTHER SITES:
PRA Chinese
Rubber Journal Asia
Injection Moulding Asia
Energy, Oil & Gas Asia
IKO Polymeric: Innovative solution for energy-efficient production of flexible PVC
Also, download this story from the electronic issue here
This article by Alois Billigen, Division Manager Marketing/ Documentation of AZO GmbH + Co. KG, is a case study of systems installed by IKO Polymeric for the production of flexible PVC for roofing membranes.
IKO Group is a global manufacturer of high-grade roofing systems. Its subsidiary, IKO Polymeric, whose headquarters are in Chesterfield, Great Britain, was founded in 2005 in order to promote single-layer ply roofing membranes for flat roofs. Since it was first founded, the division has grown from three employees to 80 and it is now the market leader in Great Britain.
Roofing membranes from IKO Polymeric are used in both new buildings and in refurbishments. The company offers an extremely broad variety of products for high-performance flat roofing solutions.
Since IKO Polymeric's aim was to manufacture the flexible PVC needed to make the roofing membranes at its own site in Chesterfield, provided it could achieve a high level of energy efficiency, the company had planned to invest in a manufacturing plant for flexible PVC.
AZO was charged with developing and producing this plant, after winning over the contract against well-known rival firms.
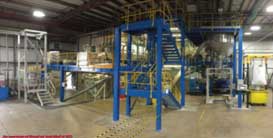
A crucial factor in awarding the contract to AZO was its many years of experience in raw materials handling and its technical expertise. Indeed, AZO notched up points with its custom solutions to satisfy the customer’s specific requirements. For instance, existing peripherals could be made use of and new plants designed exactly, to fit the existing building.
The tasks AZO faced
AZO faced two major challenges:
- adapting and integrating the plant to fit in the existing buildings
- directly feeding the compounder/extruder downstream from the heating mixer without a cooling stage, which meant no longer cooling the mixture before the extruder, as is otherwise done when manufacturing flexible PVC.
AZO also had to meet the following requirements:
- maximum process accuracy
- maximum versatility
- consistently high product quality
- highly accurate weighing
- constant batch weights
- a high degree of process transparency
- reliable documentation
- automation of all raw materials handling, for both powdered and liquid raw materials.
Dispensing with the cooling stage resulted in particular challenges when feeding materials to the extruder. It was necessary to maintain the mixture at a temperature of approximately 100°C, while simultaneously stabilising or increasing homogeneity of the mixture.
After the mixing process, the mixture is moistened, which increases the challenge yet further with regard to homogeneity and consistent temperatures and requires that
the plant engineering firm has in-depth knowledge of process engineering and extensive experience.
Reliable solutions for control engineering systems are required here: the buffer bin, which is designed as an insulated mixing vessel, is equipped with a weighing device and a temperature-measuring instrument. The signals it sends are used to regulate filling levels and temperature to ensure maximum consistency in the properties of the end products.
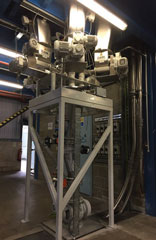
Major savings in energy are achieved by dispensing with the processes of cooling the blend in the cooling mixer and of reheating it in the extruder, as these stages use substantial amounts of energy. The height of the building meant it was also possible to dispense with expensive modifications such as extending the roof.
A further stipulation for materials handling was to integrate a large number of raw materials, both in liquid and in powdered form. The wide variety of formulations meant that the plant had to be very flexible at the same time.
The formulations contain large quantities of plasticisers, PVC, chalk and different additives. Tracking and tracing of the entire production process, using barcode scanners at raw materials feeding points, was a further requirement for the new plant.
Implementation
Commissioning of the plant took place in 2014; and in 2017, the final phase in expansion of the plant involved supplying an additional silo for PVC.
Feeding of raw materials and feeding the heating mixer
Due to the large number of different materials, feeding of raw materials is broken down into liquid medium components, liquid components and into large, medium and small powdered components.
Liquid plasticisers are stored in four tanks and are pumped into gain-in-weight scales via micro filters with pressure monitoring. The micro filters are designed as a bypass solution, so that there are no downtimes caused by the need to carry out cleaning. The raw materials are conveyed completely from the scales into the heating mixer.
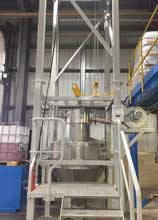
The liquid medium components are supplied in two scale hoppers, which are connected in parallel. From there, they are then weighed into the heating mixer using the loss-inweight method.
Different types of PVC are stored in three silos and are transported via a vacuum conveyor into the vacuum conveying scales situated above the heating mixer. In addition, the PVC can also be transported into the vacuum conveying scales from a big bag discharge station.
Five medium
components are
weighed into
a scale hopper
via sack discharge stations and volumetric dosing
units. These five raw materials have minimum
ignition energy between 3 and 10 mJ. The medium
components are also conveyed in parallel into the
same vacuum conveying scales in the PVC line.
The proportion of these components varies, depending on the formulation, up to 5% within the PVC line into the vacuum conveying scales. This leads to a premix of the different raw materials, which are discharged from the scales into the heating mixer.
Micro components can be added to the heating mixer using appropriate methods of product feeding.
Feeding the extruder with the mixture from the heating mixer
A special feature is that there is no cooling stage in the direct feeding of the compounder/extruder after the heating mixer. This results in a huge advantage for the customer in terms of energy efficiency.
The demands on control engineering are extremely high for this solution. The heating mixer discharges into a homogeniser hopper via a screw feeder. The screw feeder and hopper are insulated in order to maintain the temperature at approximately 100°C. It is vital to avoid fluctuations in product temperature at this stage in the process. Failure to achieve this will have negative consequences on the subsequent extrusion process and product quality.
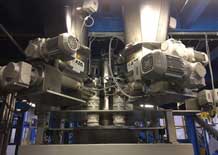
Homogenisation serves to stabilise or improve the quality of the mix. The hopper is equipped as scales in order to monitor yields and keep check of the product temperature.
The extruder is fed continuously using differential dosing scales. In addition, two vacuum conveyors and downstream differential dosing scales can be used to feed returning raw materials and various substances for dyeing the PVC.
Filling of finished goods following the extruder
The finished products are discharged from the extruder into a hopper and conveyed from there into a silo for intermediate storage.
The silo is fitted with load cells. The flexible PVC is filled into big bags either for interim storage or for selling. There is an option to expand the plant with direct feeding to the next process (calender).
The AZO Group
The AZO Group delivers innovative concepts for automation from a single supplier: plant engineering and construction, process engineering and process IT dovetail seamlessly. AZO provides everything – from the initial concept, from innovative individual components for storage, discharge, screening, conveying, dosing and weighing of raw materials right through to a turnkey solution. AZO is the specialist for automated handling of raw materials and of processes; of large, medium and small components in granular, powder and liquid form.
AZO SOLIDS is the expert when it comes to efficient handling of bulk materials. It caters to reliable
storage, discharge, screening, conveying, dosing and weighing
of raw materials within fully automated processes. From the
major ingredient down to micro quantities, from the initial study
concerning safety concepts and risk assessments through to the
turnkey plant in its entirety, AZO combines what belongs together.
Founded in 2008, AZO LIQUIDS provides for mixing, dispersing and homogenising liquid and semi-solid products. Its main target is the development of a new generation of batch and continuous process plants with an innovative homogeniser for fully automatic feeding of raw materials.
AZO CONTROLS is
the expert for innovative
process IT in developing
automation solutions in the
production environment.
From consulting to
implementation, from sensor technology to the commercial
production planning level, this is where AZO will provide with
reliable, joined-up solutions at each stage.
For over 35 years, AZO CONTROLS, as a full-service provider for automation, has delivered innovative solutions in the production environment for the entire value chain. It is backed by well-trained staff from a wide variety of specialist fields, who offer extensive experience, in-depth knowledge of products and process-oriented approaches resulting in the ideal combination of innovation and reliability. AZO CONTROLS acts as a partner for many renowned companies and, in addition to its own developments, it offers solutions that are based on tools that are available commercially.
Hence, the AZO Group provides support for successful companies all over the world in implementing innovative projects by using the technologies of the future and through its extensive network of production and sales companies. In this way, AZO is continuously enhancing its products and adapting them to the future requirements of the market and customers’ needs.
With sales subsidiaries and service partners the world over, customers are provided with expert advice and service in line with market requirements.
The success of AZO is based first and foremost on the quality and reliability of the solutions and the accumulated experience of 65 years in building automatic material handling systems.
At the same time, AZO is open to new ideas and is not afraid to translate them into new innovative systems for dispersing, mixing and homogenising of liquid and semi-solid products.
AZO measures the quality of its services by considering the customers benefit. The reliability of the AZO system in combination with specifically configured and fine-tuned process control allows the highest possible availability and therefore an excellent efficiency.
For further information contact:
Alois Billigen, Divisional Manager Marketing/Documentation
Tel: +49(0)6291/92-0
Email: azo-solids@azo.com
Copyright (c) 2017 www.plasticsandrubberasia.com. All rights reserved.