Recycling: Solution to plastic waste recycling at the end of the road
Over 2 billion tonnes/year of municipal solid waste is generated in the world, according to the World Bank¹, with this figure expected to rise to 3.4 billion tonnes by 2050.
In terms of waste products, the plastics segment is anticipated to exhibit the fastest compound annual growth rate of 7.1% from 2020 to 2027². Global plastic waste volumes are expected to reach 460 million tonnes by 2030 as a result.
Packaging – main culprit
Plastic packaging, remains the largest application, representing 26% of the total volume of plastics used³. Furthermore, an overwhelming 72% of plastic packaging is not recovered at all: 40% is landfilled and 32% leaks out of the collection system — that is, either it is not collected at all, or it is collected but then illegally dumped or mismanaged.
Not only is packaging the largest application of plastics with 26% of volumes, its small size and low residual value also makes it especially prone to leakage. One indicative data point is that plastic packaging comprises more than 62% of all items (including non-plastics) collected in international coastal clean-up operations.
Waste collection is a critical step in managing waste McKinsey’s Sustainability in Packaging: Consumer Views in Emerging Asia4 report states the region remains packaging’s top growth market.
As the use of packaging in Asia increases, so too does the ecological burden, as packaging materials leak into the environment. Usually, this is often due to a lack of waste collection and adequate recycling systems at a scale needed to manage the increased production of waste.
Interestingly, consumers in China, India, and Indonesia, according to McKinsey, are currently more concerned about water and air pollution than physical waste production. Within these three regions Generation X consumers demonstrate the highest level of environmental concern across different sustainability issues, followed by Gen Z’s, millennials, and baby boomers, respectively.
When looking at how they can assist the recycling sector in Asia, consumer packaged goods companies (CPGs) and their packaging supply partners need to understand how local consumers use products and dispose of them. Especially as those surveyed by McKinsey would like to see more recyclable or compostable plastic films and paperbased packaging in the future.
A way forward
In dealing with the plastic waste crisis there is an urgent need to transform today’s broken systems for recycling plastic.
According to the Ellen MacArthur Foundation, 95% of plastic packaging material valued at US$100 billion per annum, is being lost globally because it is not recycled but ends up incinerated or landfilled.
Holistic solutions are required that integrate technologies with the local waste systems that are already in place.
Embracing this concept is the Greenback Circularity Platform, developed by Greenback Recycling Technologies, a UK-based company that is implementing distributed advanced recycling solutions.
Greenback’s Circularity Platform improves on current audit-based methods to certify proof of material provenance and value. It manages this by using a combination of artificial intelligence and IoT gathered evidence, all backed up on Blockchain to provide additional security. This evidence includes camera images, weigh scale data, smart contracts, and advanced analysis of waste types, including AI recognition.
One of the solutions Greenback is implementing in the recycling of post consumer plastic waste, involves waste pickers sifting through hard-to-recycle flexible plastic items and then moving these items onto the recycling technology installed at landfill sites where the core elements are extracted and reused by the plastics recycling industry.
Enval microwave-induced pyrolysis
The recycling technology planned for use by Greenback at landfill sites is Cambridge spin-out Enval’s microwave induced pyrolysis, developed via Enval’s proprietary pyrolysis solution for low-density packaging waste.
This pyrolysis recycling technology works by enabling a thermochemical decomposition of organic material at elevated temperatures in the absence of oxygen. It is viewed as one of the solutions for hard-to-recycle flexible plastics headed to landfill, as it allows the treatment of mixed, unwashed plastic wastes. The system has fantastic potential for recycling heterogeneous plastic waste that cannot be economically physically separated and classed.
When installed at landfill sites, the technology gives the CPG companies total assurance that the pyrolysis oil has come from post-consumer plastic waste. It also enables waste pickers to be reimbursed at source for separating plastic waste materials into the different waste streams, adding fair trade benefits into the model.
These pyrolysis plants are scalable and quick to commission, which are important factors to consider when faced with growing recycling quotas and as governments around the world implement more environmental regulations to address plastic waste.
A single module can process 2.5 kilotonnes/year of hardto-recycle plastic waste and can neatly scale in 2.5 kilotonneincrements to fit the size of the waste stream available.
By placing recycling plants close to the waste sources, they can assist local economies extract maximum value from their waste. A combination of local collection, sorting and recycling helps to reduce plastic pollution, water usage, resource depletion and CO2 emissions into the bargain. On top of this, fair distribution of value along the supply chain is a key driver of the business.
It is critical for the marketplace to ensure that the provenance is certified. When the pyrolysis oil is utilised for manufacturing new food-grade packaging, everyone knows it has been produced from post consumer plastic waste.
The Circularity Platform is invaluable as it enables Greenback to enhance the value of its Py-Oil by certifying its provenance. Organisations within the value chain have to be certain that the environmental claims can be substantiated, while CPG companies need assurance that the voluntary per tonne fees paid results in the collection and recycling of post-consumer waste.
Reformation needed urgently
Since there is an urgent need to reform today’s systems for recycling, Greenback is working with several prominent CPGs to address these challenges head-on.
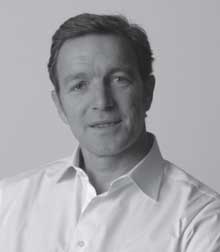
The company is excited about the potential of the technology and awaits the outcome of its first project, which is imminent in Latin America.
“Shifting to a circular economy creates new markets and opportunities, especially when the right technology is utilised in recycling the vast number of plastics that cannot be economically recovered through conventional recycling,” says Philippe von Stauffenberg, Greenback CEO. There are some significant challenges ahead, and one critical challenge for CPG companies attempting to solve their plastics issues is securing legitimate sources of clean, recycled plastics, and being able to verify the provenance of materials - from the point of collection to use.”
(PRA)
Subscribe to Get the Latest Updates from PRA Please click here
©2021 Plastics and Rubber Asia. All rights reserved.
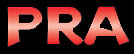
©2020 Plastics and Rubber Asia. All rights reserved.
Home Terms & Conditions Privacy Policy Webmail Site Map About Us