Green materials: Eneos/Nippon/Mitsubishi to study biobased ethylene; BASF introduces additive solutions for mechanical recycling of plastics
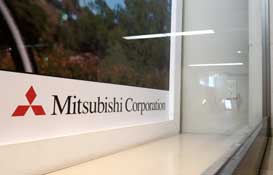
Eneos Corporation, Nippon Shokubai Co., Ltd. (Nippon Shokubai) and Mitsubishi Corporation (MC) have agreed to undertake a joint feasibility study on the manufacturing and sale of ethylene derivatives derived from bio-based raw materials (bio-derivatives). This will be the first such undertaking in Japan and is in line with the country’s aim to go carbon neutral by the year 2050. The plan is to commence operations in fiscal year 2024.
Eneos manufactures and sells ethylene from petroleum products. Using its ethylene, Nippon Shokubai manufactures and sells ethylene oxide (raw materials for toiletries, cosmetics, etc.), ethylene oxide derivatives and ethylene glycol (raw materials for PET bottles, polyester fibres, etc.). Mitsubishi Corporation’s expertise is to supply stability in chemicals products and raw materials, as well as business-development and marketing capabilities in bio-based and eco-friendly raw materials. By leveraging their respective strengths, the companies expect to forge Japan’s first bio-derivatives supply chain.
The joint study is to assess the feasibility of these bio-derivatives supply chain and the market’s need for them, using the companies’ existing production capabilities and sales channels for both ethylene and ethylene derivatives including the supply-and-logistics infrastructure at the Kawasaki Industrial Complex.
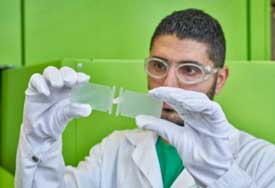
In other news, German chemical firm BASF has launched IrgaCycle, a new range of additive solutions to address the imminent needs in plastics recycling.
The plastics industry is seeking ways to incorporate higher content of recycled polymeric material in all major applications to meet sustainability goals, while facing growing consumer concerns and stricter regulatory requirements to reduce plastic waste. Hereby a major challenge is to mitigate quality deficiencies of polymers arising from thermal and mechanical stress during the recycling process.
Recycled plastics often contain impurities and polymer contaminants that accelerate polymer degradation, which change the material properties. Consequently, recyclers and plastic converters are facing quality and performance issues while processing recycled polymeric material. Formulated additive packages improving the properties of these recycled plastics can be a solution for this challenge.
‟The production of plastics from mechanical recycling is expected to almost triple by 2030, driven by improved technologies and regulation. This corresponds to a growth of around 10% per year,” says Dr. Thomas Kloster, President of BASF’s Performance Chemicals division. ‟With IrgaCycle we are expanding our existing portfolio step by step by specific solutions for recycling to support the circular economy goals for plastics.”
The new IrgaCycle range includes additive solutions that can help increase the percentage of recycled content in several end-use applications such as packaging, automotive & mobility, and building and construction. These solutions address specific quality issues associated with recycled resins, such as limited processability, poor long-term thermal stability and insufficient protection from outdoor weathering. At launch, the product line includes a range of different additive formulations, with more to follow in the future.
IrgaCycle PS 030 G enhances long-term thermal stability in rigid applications, mainly for recycled HDPE, polyolefins and mixed polymers.
IrgaCycle PS 031 G improves processing and long-term thermal stability of recycled LDPE and LLDPE for incorporation into films and related flexible packaging applications.
IrgaCycle PS 032 G provides processing stability and long-term thermal protection for recycled PP and polyolefin blends containing impurities.
IrgaCycle UV 033 DD combines weathering stability with enhanced thermal and processing stability for reclaimed HDPE and PP blends for re-use in outdoor goods.
IrgaCycle XT 034 DD rejuvenates processing, long-term heat stability and helps neutralise impurities of the “first life” of the plastic, and with this improves mechanical properties of polyolefin recyclates.
A specific advantage of these blends lies in their ready-to-use product forms, which are easy to apply in the recycling steps. The granulated non-dusting product form ensures safe and easy dosage during converting or compounding of reclaimed material.
“We have formulated these solutions based on our extensive experience in the plastics industry, combining the high quality of our antioxidants and light stabiliser systems with our application expertise,” says Dr. Volker Bach, Global Lead Innovation at BASF Plastic Additives. “With our global setup we are able to engage across the entire value chain of the recycling industry, be it with brand owners or converters alike and in all regions.”
The IrgaCycle range is offered as part of the Valeras portfolio. In addition to enabling plastics circularity with IrgaCycle, the solutions are said to bring significant sustainability value to plastic applications by improving durability, reducing waste, saving energy, reducing emissions, and promoting biodiversity.
(PRA)
Subscribe to Get the Latest Updates from PRA Please click here
©2021 Plastics and Rubber Asia. All rights reserved.
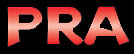
©2020 Plastics and Rubber Asia. All rights reserved.
Home Terms & Conditions Privacy Policy Webmail Site Map About Us