Decoupling from plastics for the sake of the environment
The packaging industry can help in mitigating the worsening climate change with responsible sourcing of raw materials and eco-friendly material substitution, says Angelica Buan in this article.
Material substitution and recycling in packaging
Plastics are an unrivalled packaging material due to their diverse properties and low production costs. However, fuelled by expectations of emissions of 85 million tonnes/ year of CO2 by 2050 and the drive for a low-carbon economy, plastics have come under the heat of late.
The use of renewable materials is seen as a viable option. Finnish packaging materials producer Stora Enso is looking at shifting from fossil to renewable materials like wood fibre as a complementing strategy for packaging. In a study conducted by Swedish management consulting business Material Economics for Stora Enso, wood fibre is pointed out as CO2-neutral and able to offset 65% of fibre production emissions. It also stated that while recycling is necessary to address the plastics problem, this solution will only tackle 30-40% of the problem.
Stora Enso also stated that eliminating CO2 emissions from packaging plastics in the EU alone would require 80% of all electricity currently produced from renewable energy sources in the EU.

Meanwhile, Belgium-based industry association PlasticsEurope recently said that revisions made to the European Commission’s Packaging and Packaging Waste Directive (PPWD) are key to the transition to a circular economy for plastics. It adds that European plastics producers support the European Commission’s proposal for a mandatory EU recycled content target for plastics packaging, and it is now calling for a mandatory target of 30% recycled content in plastics packaging by 2030.
It adds that members are already working towards this target “by investing billions of Euros in increased high-quality supply of recycled plastics and leading-edge technology solutions.” Ramping up chemical recycling is essential to achieve such a mandatory target, it said, citing that its members' planned investments in this vital technology and infrastructure range from EUR2.6 billion by 2025 to EUR7.2 billion by 2030 in Europe.
Waste, non-food feedstock for bioplastics
Without plastics, packaging may not be the same. Even the most environmentally-friendly packaging alternatives, excluding paper, metal, and glass, will contain plastic elements, but in smaller proportions.
Bioplastics are biomass-derived polymers that attempt to mimic the mechanical properties of petroleum-based plastics while posing no environmental risks.
Since the invention of the first cellulose-based plastic and casein milk plastic in the 19th century, the development of bioplastics has gained traction. Following this, companies developed and patented bioplastics made from wood, hemp, and cotton, such as Cellophane (which was a registered trademark by Futamura Chemical UK in some countries), as well as plastics produced by organism fermentation. As a result of these breakthroughs, it became possible to use a material derived from renewable resources.
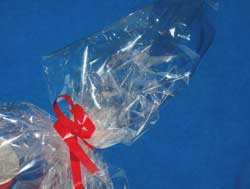
However, the cost and viability of commercialscale production have been a disadvantage, with questions been raised about the sustainability of bioplastics’ feedstock sourcing.
With the availability of new materials processing technologies and studies, the production of bioplastics is expected to become less expensive. Current R&D efforts have also demonstrated the viability of a variety of renewable sources that address carbon footprint and feedstock sustainability.
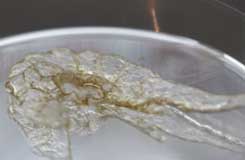
For example, The Circe (Circular industries with cellular factories) project of Harvard University’s Wyss Institute is using engineered microbes to produce biodegradable plastics from carbon dioxide and hydrogen gases. Bioplastics, their study claims, will have smaller carbon footprint than petroleum-based plastics and minimal environmental impact than plant-based plastics. Circe’s proprietary microorganisms consume CO2 and H2 gases to produce a class of biodegradable fatty acid polymers that can be used in applications ranging from packaging to cosmetics and apparel. These polymers are said to be non-toxic and biodegrade quickly in both the ocean and on land.
The Institute also developed a degradable bioplastic called Shrilk, a portmanteau of its two key ingredients – shrimp shells (chitosan) and silk protein. According to Wyss scientists, Shrilk biodegrades quickly in compost, producing a nitrogen-rich fertiliser. It can be utilised to make implantable foams, films, and scaffolds for surgical closures, wound healing, tissue engineering, and regenerative medicine applications, since chitosan and fibroin are both employed in FDA-approved devices.
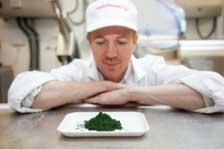
Meanwhile, an EU research project in collaboration with the University of Hohenheim showcases seaweeds or algae as sustainable carbohydrate source for bioplastic development. According to the University scientists, these are not only biodegradable, but their properties can also help to extend the shelf life of food products packaged in them.
Dr Amparo Lopez-Rubio from the Institute of Agrochemistry and Food Technology (IATA-CSIC) in Valencia, Spain, who is the coordinator of the EU-funded BIOCARB4-FOOD project attests to algae’s potentiality as a source of vital compounds, not to mention that it is abundant.
The algae industry is currently generating a turnover of approximately US$7.4 billion worldwide, with interest for applications in pharmaceutical and packaging driving its growth. The specific properties of these algae carbohydrates, also known as phycocolloids, make them suited for use as smart packaging materials, the scientists said. BIOCARB-4-FOOD, which runs from September 2018 to September 2021, is researching on more efficient methods, such as ultrasound, microwaves, and enzymes, for extracting carbohydrates from algae, to optimise the process.
Meanwhile, algae and sea grasses reproduce quickly, grow in a range of conditions, and as an alternative biomass source for bioplastics do not interfere with food production, according to López-Rubio.
Equally important, industrial extraction byproducts can be used because the remaining biomass still contains enough bioactive compounds to produce novel carbohydrate-based extracts and fibres, such as cellulose and nano-cellulose, which can be used to develop biodegradable packaging materials, as demonstrated in the IATA-CSIC laboratory
Pitching PVA for a real green solution
Another viable alternative raw material is polyvinyl alcohol (PVA or PVOH), which is in high demand. The global PVOH market will reach US$ 1.2 billion by 2025, based on Grand View Research’s estimate, and cross US$1.3 billion by 2027 based on Global Industry Analysts’ projection.
PVA or PVOH use for packaging is increasing, according to Bioplastics International, an Arizona-based producer of PVOH and bioresins from plant starches. Even so, the market must be constantly informed about the advantages of PVA from the standpoints of the environment and customers, it adds.
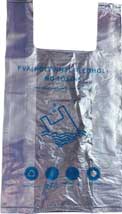
In an interview with PRA (www.plasticandrubberasia. com), Garreth Valentino, CEO of Bioplastics International, said that conveying knowledge about PVOH is difficult amid a climate of greenwashing by industry marketers.
“Right now, we’re involved in the huge effort of informing the rest of the world about our water-soluble, compostable PVOH bags. This is not a simple task, especially when the majority of people believe we’re just using a catchphrase to promote bioplastic bags. People are unable to grasp the existence of a bag that is both safe and dissolves in water in minutes. They also expect PVOH bags to cost the same as petroleum-based bags. Because the majority of people have never heard of PVOH, we have our job cut out for us! We’re getting a lot of positive feedback, and every plastic bag we can replace with PVOH is a winwin situation,” Valentino said.
Describing PVOH, he added that the hydrophilic synthetic polymer is manufactured by the hydrolysis of polyvinyl acetate, which is formed by the polymerisation of vinyl acetate
“It is made from renewable natural gas and minerals, contains no plastic, no toxins, no heavy metals, and no bioplastic. It dissolves in water in minutes, leaving behind carbon dioxide and water. It does not leave behind any microplastics or any residues,” he affirmed.
He stressed that PVOH is safe for human consumption, having been approved by the US FDA, and is currently used as a food additive and in the medical industry, in “advanced biomedical applications such as wound dressing, wound management, drug delivery systems, artificial organs, and contact lenses.” All this is due to its ability to retain water almost as well as natural cells, as well as its biocompatible, biodegradable, and non-toxic behaviour, elaborated Valentino
Furthermore, PVOH is non-toxic to animals, claims Valentino, adding that it can be eaten by fish, birds, marine animals, and land animals, and it will safely pass through their digestive systems.
The water-soluble polymer can be mass-produced in vast quantities and can be used for blown films, extrusion, or injection moulding processes, he said.
PVOH: neither a fad nor a bioplastic
Bioplastics have become a movement, according to Valentino, due to increased public awareness over marine waste, consumer interest, and legislative regulations against polluting plastics. Nonetheless, studies have shown that bioplastics do not biodegrade in landfills, despite the fact that they may be crucial in efforts to defossilise the sector. They are also expensive to manufacture, and if not properly disposed of can pollute recycling processes.

Valentino stated that his company, which also produces polylactic acid (PLA)-based products, has focused on manufacturing PVOH/PVA items in order to help mitigate the problem of marine litter.
“We continue to make PLA items, but our new focus is on saving our oceans from the plague of plastic waste,” he said.
He said that the current plastic waste issue is a serious one and must be immediately addressed.
“Only about 10% of the world’s plastics are recycled. The majority of them will wind up in landfills or in the oceans. If left for hundreds of years in landfills, plastics will leak methane gas into our environment. Methane is a powerful greenhouse gas with a warming potential 20 times greater than carbon dioxide.”
He said that in view of the above, the company decided to develop PVOH bags, which are “stronger, more durable, and will hold more weight than plastic or PLA bags”. Furthermore, PVOH bags and products do not need to be recycled. They can be washed down the sink drain. If they enter the petroleum-based recycling stream, they will not contaminate it. PVOH waste in landfills will completely disintegrate into carbon dioxide and water as soon as rain or moisture penetrates the soil, he said.
At this point, Valentino also stressed that PVOH is not a bioplastic although there is the tendency to “misidentify” it as such, and this, he observed, is hindering the patronage of the product.
“Potential buyers or supermarkets may mistakenly believe that our PVOH bags are merely a new name for bioplastic bags, causing them to show little interest. Our PVOH bags have nothing in common with bioplastic bags - they contain no plant starch, lactic acid or any other bioplastic component. A bioplastic bag will be present in the environment for years.”
Valentino says the company is “opposed to the use of bioplastic bags, which can last for years once they enter the environment”.
“People cannot comprehend that there is a bag available that will only last minutes in the ocean and even less time in a landfill,” he explained.
Light at the end of the tunnel with PVOH
With all the benefits it has going for it, a downside is that it costs more to develop PVOH goods, compared to petroleum-based plastics. “In terms of bags, PVOH bags are currently more expensive than paper bags,” commented Valentino. He counters that a way forward to reducing the costs would be bigger volumes. “The costs will be significantly reduced as more potential purchasers realise that PVOH bags and products are in a class of their own, and can help to eliminate the horrible plastic pollution crisis.”
“In my opinion, are we allowed to attach a cost to preservation of our seas and reduction of greenhouse gas emissions?” he ponders.
In view of this, Bioplastics International intends to continue advocating the reduction of plastic waste and one way is through mandatory use of PVOH bags. “We would like to see the usage of PVOH bags made compulsory in supermarkets, restaurants, and other businesses. Our goal is to never see another plastic bag on a beach, to never have a sea turtle or other wildlife die as a result of eating plastic bags, and to never have humans infested with microplastics,” Valentino emphasised<.p>
Furthermore, the US company also intends to push PVOH in the medical, pharmaceutical, and cruise line industry sectors.
“That’s a good start,” he noted, concluding that PVOH bags are not the full solution to saving the planet and that the company intends to continue soldiering on for future solutions.
(PRA)
Subscribe to Get the Latest Updates from PRA Please click here
©2021 Plastics and Rubber Asia. All rights reserved.
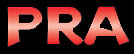
©2020 Plastics and Rubber Asia. All rights reserved.
Home Terms & Conditions Privacy Policy Webmail Site Map About Us