Blow Moulding: Cypet on a good run with PET ISBM
Cyprus-based manufacturer of single-stage injection stretch blow-moulding (ISBM) systems Cypet Technologies pushed ahead with expansion plans, even against the challenging Covid-19 situation
"Although we faced a slowdown in order intake in 2020 due to the negative investment climate caused by the pandemic, we had a strong order book entering the pandemic period, which sustained the operations until orders picked up again,” said Polykarpos (Pol) Panayiotides, Head of Business Development, Far East & ASEAN.
He explained that even during “the difficult Covid period, the company had been hard at work to grow its sales and support team, with dedicated people for Europe, Asia, The Americas, Middle East and Africa.”
He added, “Our global network of agents has also grown and we have plans to expand it further.”
Currently, the company has a global customer base on all five continents, with additional offices and a manufacturing facility in Ahmedabad, India.
“Our aim in the next few years is to increase the sales of Cypet machinery and moulds globally,” he says.
Making strides in ISBM with Cypet machines

ISBM is a technology that transforms PET resin directly into finished containers such as bottles, jars, jerrycans, drums and pressurised containers.
The flexibility offered by Cypet’s production machines plus the “very low energy consumption (up to 50%, depending on the bottle that is being produced)” are factors for its popularity.
“Packaging producers can now incorporate handles as one piece with the blown container; can produce containers from tiny 20 ml bottles up to huge 120 l industrial drums and can use their Cypet machine both as a blow moulding system as well as a standard injection moulding machine,” said Pol.
The Cypet process is set apart from conventional singlestage technologies in that it utilises a single clamping unit for opening and closing both the injection and the blow moulds. As a result, instead of using a specially designed machine, the process utilises the clamping unit (and injection unit) of an injection moulding machine base, converting it into a single-stage machine by integrating it with a stretch-blowing unit, a set of moulds and a control system.
The stretch-blowing unit carries out the functions of transferring the preforms from the injection to the blow moulds, blowing them into containers and removing the finished containers.
Furthermore, Cypet offers some machine models that are all-electric, making them especially suitable for medical, pharmaceutical or food contact applications.
PET – recyclability an attraction
The company focuses on PET processing because PET has very good mechanical properties and excellent recyclability. It can be easily separated from other plastics in mixed waste, can be re-used as re-grind or recycled into granules with equal properties as the virgin material, including suitability for food contact. Therefore, it can be recycled repeatedly, making it ideal for use in a circular economy.
When asked if Cypet machines are able to cater to rPET, Pol explains, “Yes, they are able to produce containers with both virgin and rPET. As an example, we had a customer produce a 5 l PET jerrycan with a handle. It is being used to package Ad Blue by Shell in Europe. This is made from 100% rPET, on a Cypet machine.”
Making a difference with a Cypet machine

When asked what sets its machines apart from the competition, Pol explained, “A Cypet ISBM machine works in a different way to competitor ISBM machines. Firstly, the layout of the machine is different: it has a single, horizontal clamping unit. The injection mould is situated vertically below the blow mould and the moulds are laid out at 90 degrees to each other, meaning that the preforms are rotated by 90 degrees when transferred from injection to blow mould.”
He also adds that the Cypet machine requires only one set of neck rings rather than three needed on other machines. Thirdly, a Cypet machine uses injection moulds that are similar to two stage preform production - this allows the Cypet machine to be used also as a standard injection moulding machine, if needed.
“Imagine being able to blow your bottle in PET and then switching moulds to produce the HDPE cap for that bottle, all on the same machine. Being able to use your ISBM machine also as an injection moulding machine, de-risks the initial investment and offers a flexibility that does not exist in other ISBM machines on the market.”
Due to the uniqueness of the technology, in that it uses only one clamping unit to open/close both the injection mould and blow mould, while conventional single-stage ISBMs need two separate clamping units (and associated hydraulic pumps, servo motors etc), the investment cost for a Cypet machine is typically 10-30% less than for a conventional single stage ISBM machine, for equivalent output.
“Lower investment cost and lower electricity cost add together to allow our customers to reduce their direct production cost per bottle and hence their ROI,” adds Pol.
New area of productions/new models
Cypet is now moving into the production of large PET containers for bulk storage and transport, which is a new area for PET.
“There is large value to be had by entering such markets with PET containers and we plan to expand the presence of our machinery in the large PET container market,” according to Pol.
In 2020, Cypet also introduced its Generation 2.0 machine technology, which is applied to all of its machine models. “The upgraded technology brings numerous benefits, such as increased reliability, increased speed, higher bottle quality repeatability and faster mould change.”
Market accreditation
With all that it has to offer, Cypet’s innovations have been recognised internationally – it won the Cyprus Innovation Award in 2017 and its world-first 120 l PET Drum was a finalist in the global Sustainability Awards in 2019.
Throughout its history, Cypet has also been awarded both local and European grants relating to business innovation, helping the company to accelerate the development of its technologies and products.
“We are customer focused and committed to maximising the value we provide, not only via the products we sell but also with additional bottle development services, 24/7 technical support and commercial support,” furthers Pol.
“Whether you are new in PET container production or an established company looking to lower costs, make new products and enter new markets, or an end user looking to vertically integrate, Cypet can offer solutions that maximise return on investment and keep you ahead of the game in an ever more volatile and competitive world,” he concludes.
(PRA)
Subscribe to Get the Latest Updates from PRA Please click here
©2021 Plastics and Rubber Asia. All rights reserved.
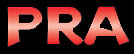
©2020 Plastics and Rubber Asia. All rights reserved.
Home Terms & Conditions Privacy Policy Webmail Site Map About Us