Ioniqa files for bankruptcy protection; deems low-priced virgin PET as a factor
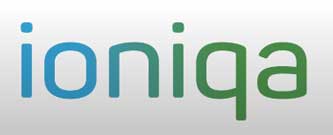
Dutch chemical recycling firm Ioniqa Technologies says has sought bankruptcy protection, having determined that achieving a positive cash flow from its advanced polyester recycling technology will take too long.
Advanced recycling is a term that is often used as an alternative description for chemical recycling (although mechanical recyclers also use the term advanced recycling to refer to some mechanical recycling processes).
Over the last decade, the company says it has made significant progress towards selling technology licensing packages, demonstrating the viability of its advanced plastic recycling technology on an industrial scale and preparing comprehensive technical, process, and economic documentation.
However, it said the comparatively low price of traditional virgin PET and the supply chain for chemically recycled PET still being in development, has resorted to its bankruptcy filing.
Furthermore, the implementation of regulated mandatory standards for meaningful recycling levels are too far out into the future, it claims.
These factors combined render the large-scale deployment of Ioniqa’s advanced recycling technology for a circular PET supply chain economically unfeasible for the company at this time and in its current set-up. It stated that this meant that large-scale deployment of its technology was not economically feasible at this time.
Ioniqa has a glycolysis-based chemical recycling demonstration plant in Geleen, the Netherlands, which has been operational since 2019 and has an estimated output of 8,000 tonnes/year according to ICIS. Investors in the site include The Coca Cola Company, Unilever, Indorama Ventures, Koch Technology Solutions, and Infinity Recycling’s Circular Plastics Fund.
Chemical recycling is an umbrella term for a variety of methods that use different production routes and feedstocks to create new material from waste. This means that each process (and each technology and individual player) has vastly different cost-structures and the economics of each chemical recycling method vary substantially. Coupled with this, achievable prices for chemically recycled products vary significantly between grade and polymer type.
Common chemical recycling methods include pyrolysis, gasification, glycolysis, hydrolysis, methanolysis, and enzymatic hydrolysis.
In chemical recycling, chemical processes are used to revert waste back to an earlier molecular state. Waste can be reverted back to monomer, building block chemicals, or all the way back to crude oil/energy. Chemical recycling alters the fundamental chemical properties of the material.
In glycolysis, a transesterification catalyst is used to break the ester linkages. Typical catalysts include monoethylene glycol (MEG), diethylene glycol (DEG), propylene glycol (PG) or dipropylene glycol (DPG).
In glycolysis, a transesterification catalyst is used to break the ester linkages, which are replaced by hydroxyl terminals. This produces bisterephthalate (BHET) and PET glycozates. These can be reacted with aliphatic diacids to make: polyester polyols, which are in turn used in polyurethane (PU) foams; co-polyesters; unsaturated resins; and hydrophobic dyes. If combined with virgin BHET, the process produces chemically recycled PET via dimethyl terephthalate (DMT) or purified terephthalic acid (PTA) glycolysis. Typical catalysts include monoethylene glycol (MEG), diethylene glycol (DEG), propylene glycol (PG) or dipropylene glycol (DPG).
(PRA)SUBSCRIBE to Get the Latest Updates from PRA Click Here»