Expansions: Grasim Industries/Lubrizol break ground on 100 kt C-PVC plant in India; Sumitomo Chemical to build pilot plant to produce propylene from ethanol
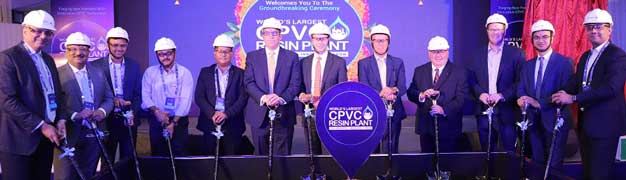
Speciality chemicals firm Lubrizol and Grasim Industries Limited, a flagship company of the Aditya Birla Group, have broken ground on the first phase of a 100,000-tonne CPVC resin plant in Vilayat, Gujarat, India. The facility located at the Grasim Industries’ site will be the largest single-site capacity for CPVC resin production globally, designed to meet rising CPVC demand for piping applications in India, as well as neighbouring countries like Nepal, Bangladesh and Indonesia.
This resin plant will utilise Lubrizol’s advanced CPVC resin manufacturing technology.
In addition to the resin site, Lubrizol is doubling its existing CPVC compound manufacturing capacity at its Dahej, Gujarat, India site from 70,000-140,000 tonnes. When coupled, these projects advance Lubrizol’s standing in the region to be the largest producer and the only company with end-to-end CPVC capability, allowing for Lubrizol’s partners to meet the projected 10-12% annual increase in CPVC demand within the India market.
Lubrizol is also planning a R&D centre at its Dahej site to address the rapidly changing needs of the India market. Lubrizol expects to add 150 to 200 new employees in the next year at this location, with an intention to add more jobs over the next several years.
Phase one of the resin site in Vilayat, as well as the additional line in Dahej, are expected to be operational by early 2025. With the upcoming project in Vilayat and expansion of the Dahej plant, Lubrizol is expected to generate more than 4,000 direct and indirect jobs.
Lubrizol introduced CPVC into the India market 25 years ago, which has represented a significant economic development opportunity for the region. Today, India is amongst the largest consumers of CPVC, primarily in the form of plumbing pipe and fittings, and growing needs for clean water in all residential and commercial buildings will drive continued growth, it adds.
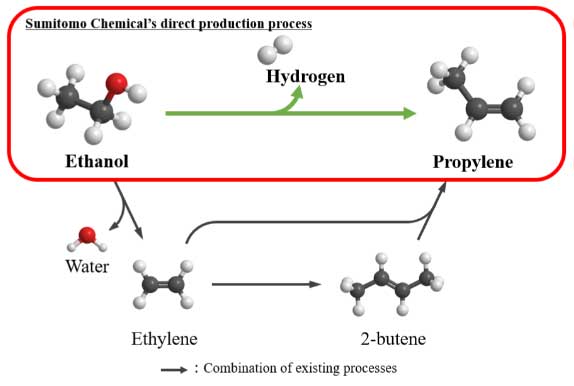
In other news, Japan’s Sumitomo Chemical has begun construction of a pilot facility to establish a process for producing propylene directly from ethanol, which is attracting attention as a sustainable chemical raw material. The development of this technology is one of the projects supported by the Nedo Green Innovation (GI) Fund. The company adds it will work to complete the construction of the pilot facility at the Sodegaura site of its Chiba Works in Japan by the first half of 2025 and step up efforts to quickly implement the technology in society.
Propylene is an essential chemical product. Currently, it is mainly produced by cracking fossil resources, such as naphtha, and classified as an upstream petrochemical. Ethanol, meanwhile, can be produced from biomass, such as sugarcane and corn, and it is anticipated that technology for manufacturing ethanol at scale from combustible waste, waste plastics or CO2 will be established in the near future. Expectations are rising for ethanol as a sustainable essential chemical raw material.
Given these developments, Sumitomo Chemical has newly established a pilot facility to produce ethylene using ethanol as a raw material at its Chiba Works, while it has also been working to develop a proprietary new process to manufacture propylene using ethanol.
This process, which is to produce propylene directly from ethanol, has the advantage of being compact and low-cost compared to existing processes that involve multiple intermediates. Additionally, while producing propylene, which enjoys ongoing solid demand, it also generates hydrogen as a by-product at the same time.
Sumitomo Chemical will acquire the necessary data for scaling the process for commercial production from the pilot facility, while also providing samples of polypropylene using the propylene produced in the pilot facility for customer evaluation. The company aims to start commercial production with the new process, as well as licensing of the technology to other companies, by the early 2030s.
(PRA)
Subscribe to Get the Latest Updates from PRA Please click here
©2023 Plastics and Rubber Asia. All rights reserved.
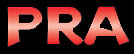
©2023 Plastics and Rubber Asia. All rights reserved.
Home Terms & Conditions Privacy Policy Webmail Site Map About Us