Expansions: Borealis/TotalEnergies start up jv PE unit in US; World’s largest PDH plant construction project streamlined in Saudi Arabia
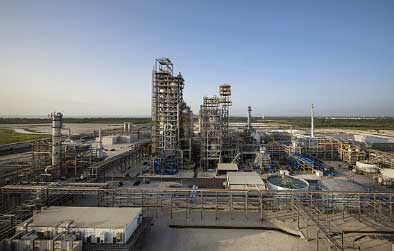
Austria’s Borealis and French petchem firm TotalEnergies recently celebrated the start-up of their Baystar joint venture’s new 625,000 tonnes/year Borstar polyethylene (PE) unit, which more than doubles the current production capacity at Baystar’s site in Pasadena, Texas.
The new US$1.4 billion unit completes the partners’ integrated petrochemicals venture, which includes the expanded Bayport PE facility, and the ethane cracker at the TotalEnergies Platform in Port Arthur, Texas.
The new PE unit, referred to as Bay 3, increases the Baystar site’s total production to over one million tons per year, which includes two legacy PE production units. Bay 3 features the proprietary Borstar 3G technology licensed in North America for the first time. Borstar technology delivers advanced value-added polymers with enhanced sustainability by enabling light-weighting and the incorporation of greater amounts of post-consumer recycled materials in a variety of end products, serving the energy, infrastructure and consumer products industries.
“The arrival of Borealis’ proprietary Borstar technology in North America by way of Baystar marks, in line with our owners’ strategies, a crucial step for us in becoming a global leader in advanced and sustainable chemicals and material solutions,” said Borealis CEO, Thomas Gangl. “Expanding and deepening our footprint through Baystar enables us to better serve customers and partners by offering improved access to Borstar based products produced right here in North America.”
“After the inauguration of the ethane cracker unit in Port Arthur last year, the start-up of the new PE unit is the second milestone of this joint venture aimed at establishing Baystar as a fully integrated U.S. petrochemical player. The fruition of this venture also advances TotalEnergies’ ambition to grow in the United States,” said Bernard Pinatel, President, Refining & Chemicals, TotalEnergies.
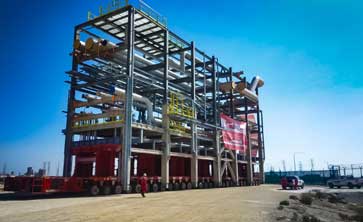
In other news, as the world’s largest Propane Dehydration plant (PDH) takes shape in Saudi Arabia, logistics firm Mammoet says it ensured that its critical components all arrived in the right sequence, and were installed smoothly and safely into position, minimising port charges and reducing onsite congestion. During construction on the congested site, customised lifting system ensured efficient use of space.
With Saudi Arabia looking to diversify its economy, the petrochemicals sector is poised for considerable growth. Forecast to allocate more than a third of its oil output to chemical production by 2030, several new facilities are now being built across the country.
One of the largest of these new facilities is a vast new Propane Dehydration plant being built by Samsung Engineering for Advanced Polyolefins Company (APOC) in Jubail Industrial City. Producing more than 840,000 tonnes/year of propylene, this is set to be the largest PDH plant in the world, increasing Saudi Arabia’s total propylene output by more than 60%.
With a project of this type, the challenges are immense. A constant flow of prefabricated components must arrive onsite in exactly the right sequence to be installed safely into position.
Mammoet says it proposed a carefully planned and integrated, all-in-one solution to streamline operations and minimise risks. Its team of experts took charge of the full scope of factory-to-foundation logistics, marine and land transport and heavy lift requirements. In doing so, it was necessary to choreograph many domestic and international shipments, handle some of the largest prefabricated components ever constructed, and deliver a series of spectacular heavy lift operations – while overcoming some unexpected challenges along the way.
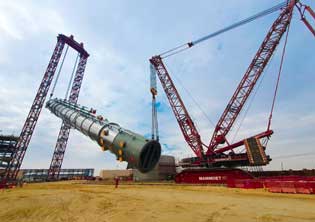
Mammoet’s expertise in inland and marine transportation played an essential role in transporting 15 vast pipe rack modules, measuring up to 46 m long and 33 m high, and weighing up to 1,900 tonnes, from a fabrication facility in the UAE to Saudi Arabia. By organising six consecutive voyages and utilising its nearby yard as a laydown facility, Mammoet optimised the sequencing, reduced onsite congestion and streamlined the operations.
The in-country transportation process included both imported and locally built components, as well as the plant’s central process tower, or product splitter. To negotiate the 26-km route from the quayside and the laydown facility to the project site, Mammoet performed complex route simulations, determined where and how the road network would need to be modified and strengthened, and managed all permitting processes with the Saudi authorities. A large fleet of transport equipment,– including 180 axle lines of SPMT, 60 conventional axles, and eight prime movers were utilized for the safe delivery of components.
Among the 125 separate heavy lift operations, erecting the 129 m tall, 10 m wide, 1,600t product splitter was the most challenging. Leveraging their expertise and specialist equipment, Mammoet drafted in a tower gantry lifting system, and a 1,250-tonne capacity crawler crane - a CC6800 with 850-tonne counter weight. The CC6800 handled the tail, keeping it clear of the ground throughout the lift, while the gantry’s hydraulic lifting system hoisted the product splitter from the top. Unlike most gantry lifting systems, Mammoet’s is entirely freestanding and requires no guy wires, even at a height of 130 m. This means the footprint is kept to an absolute minimum, which is an important consideration on a busy and congested site like this one.
The project is due to be completed and commissioned on schedule, ready for the facility to become operational from 2024.
(PRA)
Subscribe to Get the Latest Updates from PRA Please click here
©2023 Plastics and Rubber Asia. All rights reserved.
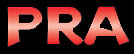
©2023 Plastics and Rubber Asia. All rights reserved.
Home Terms & Conditions Privacy Policy Webmail Site Map About Us