Renewable raw materials: key to more sustainable plastics
by Jeroen Verhoeven, Vice President Value Chain Development, Renewable Polymers and Chemicals business unit at Neste
With the clock ticking on the usage of fossil resources, the plastics industry has to quickly switch to new technologies and solutions to reduce its dependence on fossil raw materials. Renewable, bio-based materials offer a huge opportunity to bridge the gap and make plastics more sustainable - already today.
“You can’t decarbonise polymers,” a chemist told me a few years ago. And it’s true: considering carbon is the basis for organic chemistry and therefore also for the majority of polymers. And that’s why at a time when everyone is talking about decarbonisation to combat climate change, the plastics industry seems to be facing a problem.
The good news is, the problem isn’t carbon itself. The problem is the source of the carbon. Hence, for polymers, the order of the day isn’t decarbonising, it’s defossilising and finding alternative, more sustainable carbon sources.
Conventional plastics take their toll on the planet
As of today globally, the major source of carbon for plastics is fossil crude oil. Yet, every litre of fossil crude oil we use ultimately leads to additional carbon in the atmosphere in the form of CO2: when plastic products reach the end of their life and are incinerated, landfilled, or even worse, are littered in the environment where they slowly decay. The effect of this could be even similar to just burning the fossil crude oil right from the beginning. And that’s why fossil carbon sources need to be replaced.
Luckily, there are other carbon sources we can tap into to replace virgin fossil carbon, namely biomass, which is part of the Earth’s natural carbon cycle. There is a constant emission of CO2 to the atmosphere via plants at the end of their life, but also a constant absorption of CO2 from the atmosphere through plants’ photosynthesis during their growth. Instead of using fossil resources, we can use the renewable carbon from biomass, resulting in a significantly improved carbon footprint of plastic products from these bio-based sources over fossil plastics.
Before digging into the details of the technology to do so, some clarification might be helpful as there often is confusion about bioplastics, bio-based plastics and biodegradable plastics.
While similar, these terms aren’t synonymous. “Biobased” refers to the verified use of renewable materials/ biomass in the production of plastics.
“Biodegradable” refers to the end-of-life properties of the plastics, which allow decomposition, but it doesn’t say anything about the raw materials they are derived from.
Finally, “bioplastics” is the most confusing of the three and often misused as an overarching term for both or it’s used to describe one or the other.
Bio-based plastics can be made from waste and residues without loss in quality
The raw materials that can be used for bio-based plastics are numerous. Looking at the raw materials we use at Neste for our renewable products, over time our raw material mix has evolved.
We have shifted more and more to using waste and residue oils and fats, including used cooking oil or waste and residues from vegetable oil production.
These materials are then processed in our proprietary NEXBTL refineries. In contrast to fossil raw material, the oils and fats we use contain oxygen, which is an undesired element for our customers and we therefore remove them with hydrogen atoms.

What remains at the end of the refining process are pure hydrocarbons. This means the NEXBTL technology allows us to turn renewable raw materials into fuels such as renewable diesel or renewable aviation fuel or into feedstocks for the chemicals and polymers industry. There, they can replace, for example, fossil naphtha.
The big advantage of our renewable feedstock for polymers and chemicals is that it’s chemically hard to distinguish from the fossil version. In fact, it can replace fossil feedstock 1:1 and it can be used either in neat form or be mixed with fossil feedstock. This makes it rather easy to make the switch from fossil to bio-based plastics as there is no need to build up new facilities or make big changes or investments into the existing manufacturing infrastructure.
At the same time, the plastics produced from the renewable feedstock come with the same properties and qualities as the conventional ones: they can be used in the same industries and for the same applications.
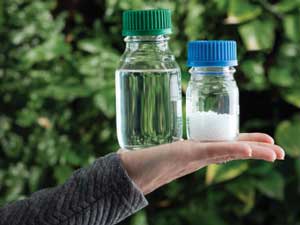
Some examples of end-consumer products that are made out of our renewable feedstock include high-quality coffee capsules, plastic film for packaging, diapers and plastic cups. Any product that is made of fossil-based plastics could also be made from bio-based plastics. The big advantage is that these products have exactly the same look and feel, as well as (food) safety and mechanical properties as their fossil-based equivalents.
While chemically identical to their fossil counterparts, the big difference with the feedstock lies in the carbon footprint.
Life cycle analysis for our renewable hydrocarbons, i.e. renewable feedstock for polymers and chemicals, shows a decrease in greenhouse gas emissions of more than 85% over fossil feedstock.
If emissions from transportation and energy use in the value chain leading to the feedstock produced were reduced further by increasing the use of renewable energy, the greenhouse gas emissions reduction could very well move even closer towards 100%. This is what we are currently working on at Neste.
(PRA)
Subscribe to Get the Latest Updates from PRA Please click here
©2022 Plastics and Rubber Asia. All rights reserved.
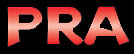
©2022 Plastics and Rubber Asia. All rights reserved.
Home Terms & Conditions Privacy Policy Webmail Site Map About Us