Recycling: Keeping marine litter at bay and useful with recycling
As the saga of marine plastic litter continues, the plastics industry is taking a serious look at recycling and to offer well-rounded solutions.
Of the marine litter found in the sea, plastics make up 90% of marine waste. Plastic waste's slow decay rates are impeding efforts to reduce marine litter quickly. Plastic waste production is also increasing, with estimates indicating that it could triple to 265 tonnes/year by 2060, up from 99 million tonnes in 2015.
Meanwhile, recycling, which has the potential to reduce plastic pollution in the environment, has been an underutilised solution. Only 9% of plastic waste is recycled globally, while 22% is mismanaged.
New “socially responsible” feedstock
A truckload of plastic enters the ocean every minute, or 8-12 million tonnes/year of plastic, with the production of plastic set to quadruple by 2050, according to data by the UN Environment Programme (UNEP).
The Canadian not-for-profit social enterprise Plastic Bank, which boasts over 23 thousand community members, has already stopped over 61 million kg of plastic, or an equivalent of over 3 billion of bottles, from entering the oceans, and engaging more than 600 recycling communities.
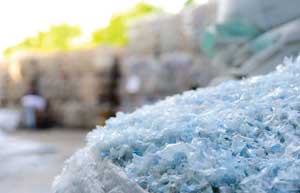
It builds recycling ecosystems in underdeveloped and developing communities to help counter both plastic pollution in the oceans and poverty.
Ocean-bound plastics are then reprocessed into what Plastic Bank refers to as “social plastic” and reintroduced into the global supply chain. These include PET, LDPE, and HDPE materials, available in bale, flake, and pellet form.
In 2017, German multinational firm Henkel became the first major consumer goods company to join forces with Plastic Bank. As of September 2022, Henkel has contributed to the collection of six million kg of plastic waste, which is equal to more than 300 million plastic bottles since 2018. Henkel's consumer business units in Laundry and Home Care, as well as Beauty Care, have introduced product packaging made from social plastic feedstock.
Meanwhile, Italian packaging company Carton Pack is the first and only fruit and vegetable manufacturer in Europe to offer packaging made entirely of social plastic feedstock.
Carton Pack adds it has already prevented over 440,000 kg of plastic - the equivalent of more than 22 million plastic bottles, from entering the ocean since partnering with Plastic Bank in 2020.
Thus, interest of using recycled feedstock is gaining strong momentum.
Bin there, done that: “bin” technologies to collect waste
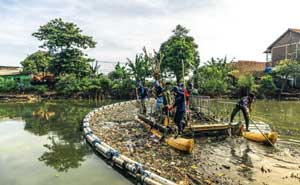
Elsewhere, practical technologies are game changers in combating marine litter, such as the Trashboom from German start-up Plastic Fischer, whose founders had the idea for their business when they saw a stream of waste plastic floating down the Mekong River.
Plastic Fischer, founded in 2019, is led by CEO/Co-founder Karsten Hirsch and describes itself as a "3L Initiative" - locally, low-tech, and lowcost. According to the company, it develops "very simple technology" in its location while boosting the local economy.
TrashBoom is a swimming barrier made of readily available materials such as PVC pipes and PET bottles that stops the vast majority of floating plastic in rivers. Trashboom has been tested in Bali, Indonesia, in 2019. The next stops will be in Bangalore, Varanasi, and Thiruvananthapuram, India; Bandung, Indonesia; and Ho Chi Minh, Vietnam.
Plastic Fischer claims to have collected, sorted, and processed river waste in a safe and "as good as possible" manner. All recyclables are sold to a local recycling company, while non-recyclables are incinerated with energy recovery (thermal recycling), in accordance with international best practices.
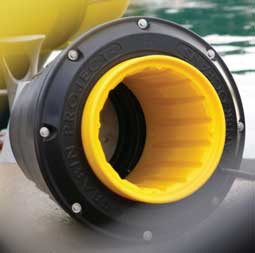
Another venture is the Seabin Project, created as a long-lasting floating garbage can capable of collecting water-borne plastics and trash 24 hours/ day, by Andrew Turton and Pete Ceglinski, two avid water lovers. Turton and Ceglinski launched Australian company Seabin Pty Ltd in 2015 and the Seabin project.
The V5 Seabin unit, which features a sturdy and 100% recyclable plastic mesh, is a floating debris “skimmer” designed to be installed in the water of marinas, yacht clubs, ports, and any other water body with a calm environment. The seabin’s catchbag holds 20 kg of debris and acts as a filter for both macro and micro floating waste. It is installed in a specific problem area in the marina on a floating dock, enabling the wind and the currents to push the debris directly to the seabin.
The Seabin project team is now working on developing a recycling programme to reuse captured plastic waste and contribute to the circular economy.
More ways to recycle difficult plastics
Oneworld Japan Corporation, based in Osaka, has developed what it says is a one-of-a-kind device called Urban Rig, which uses pyrolysis to decompose marine waste and recover oil, charcoal, and metals for recycling.
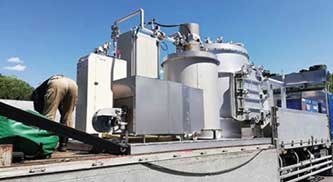
By cooling down gases that have been distilled during the pyrolysis process, Urban Rig can separate light diesel oil and other oils, methane gas, carbonised ash, and other materials from plastic. From 200 cu m of waste containing 10% plastic, Urban Rig can recover approximately 10,000 l of light diesel oil and 50 cu m of charcoal.
In a similar vein, US-based materials company Eastman is building a US$1 billion material-to-material molecular recycling facility in Port-Jérôme-sur-Seine, Normandy, France, that is expected to be operational by 2025. This location will provide the company with easy access to waste polyester feedstock, the space needed for a large facility, and the infrastructure required for operations of this scale.
With the ability to recycle 160,000 tonnes/ year of difficult-to-recycle polyester waste each, Eastman's operations at this plant will include on-site polymerisation, which will allow for sorting, depolymerisation, and recycling of PET in a single location.
Eastman adds that its polyester renewal technology (PRT) will complement mechanical recycling and achieve true circularity for difficultto-recycle plastic waste in a linear economy. Like coloured or degraded PET or textiles, this material is typically incinerated because it cannot be mechanically recycled or must be downcycled.
On a similar mission, materials company Dow and advanced plastic recycling solution company Mura Technology are joining forces to build multiple 120 kilotonnes/year recycling facilities in the US and Europe, using Mura's HydroPRS (Hydrothermal Plastic Recycling Solution).
In keeping with this, Mura intends to build a new facility at Dow's Böhlen site in Germany. The new Böhlen facility, which is expected to be operational by 2025, will provide approximately 120 KTA of advanced recycling capacity at full run-rate. This, along with other planned units in Europe and the US, would add up to 600KTA of advanced recycling capacity by 2030, propelling Dow to become the world's largest consumer of circular feedstock for polyethylene production.
The HydroPRS advanced recycling process can be used to recycle all forms of plastic, including flexible and multi-layer plastics, which have previously been deemed unrecyclable. The process uses supercritical steam to break down plastics (water at elevated pressure and temperature). In as little as 25 minutes, the steam acts like molecular scissors, cutting longer-chain hydrocarbon bonds in plastics to produce the valuable chemicals and oils from which the plastic was originally made.
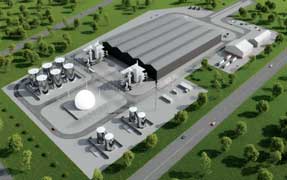
Because supercritical steam is used, the technology is naturally scalable. Unlike other methods that heat waste from the outside, steam imparts energy from the inside, resulting in an efficient conversion of plastic waste that can be maintained at any scale.
It’s complicated: Southeast Asia’s recycling status
According to a recent study, the top contributors of marine debris are from the Southeast Asia region. Six out of ten ASEAN member states alone generate more than 31 million tonnes/year of plastic waste. While many of them are engaged in efforts to combat plastic waste, these efforts tend to be policy-centric with ambiguous goals that are open for interpretation and often difficult to meet without proper directions.
To compound the problem, the sudden increase in volume of single use plastics and personal protective equipment (PPE) during the Covid-19 pandemic is putting additional stress on these countries as they tackle marine pollution.
According to Joshua Tan, Analyst (Asia Pacific) at research firm ICIS, the distribution of recycling capacity in the region does not even correspond to the distribution of population in the region. Many countries lack the necessary infrastructure, such as recycling facilities, to combat plastic pollution. Furthermore, there are national and regional plans in place to combat marine litter, either directly or indirectly, but none of them, according to Tan, actively propose recycling as a solution.
Tan went on to say that the recycling industry's role in this transition is critical. However, incentivising additional capacity investment and supporting infrastructure improvements in collection to deliver waste as feedstock to those plants are equally important and fall under the purview of the entire supply chain as well as governments.
A step in the right direction is the recent tie up between Malaysian chemical firm Petronas Chemicals Group Berhad (PCG) and US-based ExxonMobil to assess the potential for large-scale implementation of advanced plastic recycling technology to help create a circular economy for plastics in Malaysia. The companies will also evaluate opportunities to support improvements to plastic waste collection and sorting in the country.
However, Southeast Asia will remain as the top contributor of marine plastic debris without the development of recycling capacities beyond the status quo.
The many national and international developments focused on regulatory frameworks to shift markets up the waste hierarchy towards recycle/reuse and beyond are essential but just one part of the solution.
(PRA)
Subscribe to Get the Latest Updates from PRA Please click here
©2022 Plastics and Rubber Asia. All rights reserved.
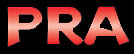
©2022 Plastics and Rubber Asia. All rights reserved.
Home Terms & Conditions Privacy Policy Webmail Site Map About Us