Green tie-ups: Neste, Idemitsu Kosan, Chimei & Mitsubishi work on bio-styrene monomer; VTT/UrbanMill to develop industrial chemical recycling
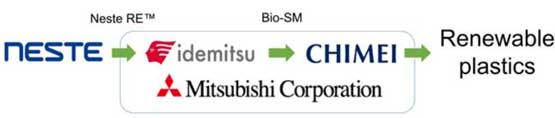
Neste, Idemitsu Kosan, Chimei Corporation and Mitsubishi Corporation have agreed to build a renewable plastics supply chain utilising bio-based hydrocarbons (Neste RE) for the production of styrene monomer (i.e. bio-SM), and its mass balanced renewable plastics derivatives including acrylonitrile butadiene styrene (i.e. bio-ABS). The bio-SM production in Japan and the renewable plastics production in Taiwan will mark the first of such production in each country, and are planned to take place in the first half of 2023.
Finnish producer of renewable and circular feedstocks Neste will provide Neste RE to Idemitsu Kosan, the biggest SM manufacturer in Japan. For this collaboration, Neste RE is produced from 100% bio-based raw materials such as waste and residues and its use can significantly reduce greenhouse gas (GHG) emissions compared with conventional fossil feedstock use, adds Neste.
Idemitsu Kosan will then produce bio-SM based on the mass balance method and supply it to Taiwanese materials firm Chimei Corporation, the biggest ABS manufacturer in the world for its renewable plastics production. Japan’s Mitsubishi Corporation will be coordinating the collaboration between the value chain partners to develop the renewable products’ market.
Through developing an even stronger partnership and closer collaboration than conventionally seen in plastics value chains, the companies are introducing new renewable contents into the value chain to enable plastic production where fossil feedstock has been replaced with renewable feedstock.
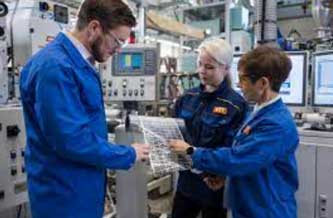
Meanwhile, also from Finland comes another tie-up between VTT Technical Research Centre and UrbanMill co-working and co-creation platform for urban innovations, a Finnish public-private-people partnership run by a private company, Järvelin Design Ltd, and the City of Espoo as one of the main partners. The two-year project of EUR3 million is funded by Business Finland and coordinated by VTT in cooperation with Aalto University. It spans multiple industrial sectors in the plastic recycling value chain and creates strong networks and collaborations between the consortium partners.
The UrbanMill is focused to create novel concepts by combining tailored pre- and post-treatment technologies with pyrolysis. The project is closely linked to Borealis SPIRIT and Valmet Beyond Circularity “Veturi” ecosystems. The other participating companies are Corex Finland, Wipak, Kaipola Recycling, Keskinen Recycling, Lamor, PR Pulping, Resiclo, Salpakierto, Sulapac and Suomen Uusiomuovi.
The project comes on the heels of a low recycling rate of plastic waste, with partners adding that mechanical recycling alone cannot meet the plastics recycling targets set in EU and national legislation. Industrially feasible chemical recycling processes capable to utilise mixed plastic waste are needed to divert plastics away from waste incineration and the environment causing carbon dioxide emissions and littering. UrbanMill co-innovation project is developing enabling technologies to utilise highly mixed plastic waste as feedstock for chemical recycling producing high quality plastic materials complementing current recycled plastics.
Even though plastics have many sustainable advantages as material, the lacking proper waste handling and recycling of plastics cause huge environmental challenges by littering and CO2 emissions. Today, in Finland the recycling rate of packaging plastics is about 30% as the new waste law sets target of 55% by 2030. Thus, there is an enormous need to increase the share of the plastic waste that can be industrially recycled back to new high quality plastic materials.
Plastics can be recycled mechanically and chemically and both are needed to meet the recycling targets. Mechanical recycling from the mixed plastic waste leads often to compromised plastic properties and thus recycled plastics cannot be used in many demanding applications, such as food packaging. In chemical recycling, plastics are broken down into starting materials, from which high-quality plastics similar to virgin plastics are made. Plastic waste used for chemical recycling can also be more mixed in quality than the raw material for mechanical recycling.
“Chemical recycling based on pyrolysis is on the verge of an industrial giant leap as new investments to demonstration and production units are frequently announced. However, many of these early demo units are still using relatively pure plastic waste fractions leaving a large share of plastic waste incinerated. UrbanMill project aims to develop enabling recycling technologies for difficult-to-recycle highly mixed plastic waste,” says Mika Härkönen, Professor of Practice at VTT.
“New technology solutions are needed to solve the huge plastic recycling problem and to reach the set EU targets. The UrbanMill project aims to develop process concepts to enable better plastic recycling with pre-treatment, pyrolysis and post-treatment. These new solutions are needed in the industry to move forward to a circular economy for plastics,” says Antti Raiko, Project manager of plastic chemical recycling in Valmet Beyond Circularity program
(PRA)
Subscribe to Get the Latest Updates from PRA Please click here
©2022 Plastics and Rubber Asia. All rights reserved.
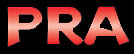
©2022 Plastics and Rubber Asia. All rights reserved.
Home Terms & Conditions Privacy Policy Webmail Site Map About Us