Climate-positivity with sustainable packaging
The packaging industry is on track to achieving carbon neutral footprint in packaging solutions by ensuring recyclability, degradability, safety and effectiveness of the packaging product, says Angelica Buan in this report.
The packaging industry generates a large portion of plastic waste, representing about US$80-$120 billion loss to the global economy every year, according to the World Economic Forum. Thus, the sector is transitioning to using environmentally-friendly sustainable packaging: responsibly sourced, recyclable, and designed to be safe and effective for use during its entire life cycle.
Although developing sustainable packaging involves the entire supply chain, sectors that are major users of plastic packaging such as food and beverage, cosmetics and hygiene, agr icul ture and others, are forging alliances with packaging manufacturers to come up with innovative and eco-friendly solutions.
Clearly, the “take-make-dispose” packaging model is passé, in lieu of the growing demand for sustainable packaging.
Alternative materials with no burden to environment
Protecting the planet’s diversity and natural resources as well as reducing the environmental footprint are barometers for sustainable packaging.

REFUCOAT, an EU-funded three-year project, focuses on developing fully-recyclable food packaging with enhanced gas barrier properties and new functionalities using high performance coatings as an alternative to current metallised and modified atmospheric packaging (MAP).
The consortium, composed of 12 partners including MIPLAST, IRIS, Grupo APEX, Manor Farm, Dacsa, Biopolis, Thunen, CIB, AIMPLAS, EUFIC, Fraunhofer and AINIA, will be utilising middle chain polyhydroxyalkanoates (PHA), biopolymers synthesised by microorganisms, such as flour. With low moisture permeability, PHA is a good alternative for fresh meat packaging and since it is biodegradable by composting, PHA can be converted into fertiliser, according to REFUCOAT.
REFUCOAT adds that it also wants to explore the use of polyglycolic acid (PGA) as a high-barrier coating for biobased food packaging films, since it is fully biodegradable and has good compatibility with other biopolymers and polyolefins. It also has excellent water barrier properties, making it a promising material for use in food packaging, as an alternative to metallic coatings since these require a complex and expensive recycling process.
Relatively, REFUCOAT has developed for the first time an efficient process for producing high-yield glycolic acid (GA) – PGA’s precursor, and which is currently produced from fossil-based raw materials.
REFUCOAT is also exploring the use of natural antifungal, antibacterial and antioxidant substances for f inal packaging st ructures for f resh chicken meat (a breeding ground for salmonella and other bacteria), snacks and cereals. For this, REFUCOAT has developed an active coating that contains antimicrobial bacteriophages to attack unwanted bacterial growth.
For dry foods such as crisps and breadcrumbs, which need to stay crunchy for a long time, while not losing or taking up any flavours to/from the environment they are stored in, an antioxidant coating is being developed, based on bioactive herb essential oils. Specifically, the innovative barrier and active coatings developed during the project are combined with commercial bio-PE, bio- PET and REFUCOAT PHA and polylactic acid (PLA) to produce packaging structures for chicken meat, breadcrumbs and crisps.
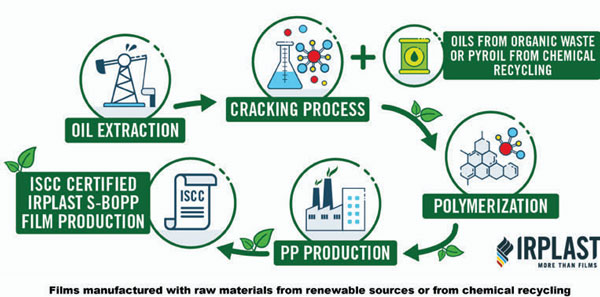
On a similar endeavour, a circular biaxiallyoriented polypropylene (BOPP) film called LOOPP and renewable NOPP (Natural BOPP) film for flexible packaging have been developed by Italian BOPP film producer Irplast utilising materials firm Sabic’s PP polymers from its Trucircle portfolio. The NOPP film is made from certified renewable Sabic PP material from biobased feedstock while LOOPP is made from material that uses feedstock made from chemical recycling of mixed post-consumer plastics. Both films are 100% recyclable in normal polyolefin waste separation streams.
Irplast, known for its BOPP LISIM stretching technology that is done in one step compared to the standard twostep process, says it has been focusing on reducing film thickness to save raw materials and energy. According to life-cycle assessment (LCA) data from Irplast, compared to an equivalent fossil fuel-BOPP film, every kg of NOPP takes 2 kg of CO2 emissions out of the environment.
In a related development for the food sector, Sabic and Netherlands-based Syntegon Technology have launched a frozen food packaging concept comprising the new PHS 2.0 sealing technology from Syntegon and 20-mcm thin BOPE film from Sabic. The partners say that brand owners can now reduce material consumption and increase output rates by replacing conventionally used LDPE films with BOPE sealed on PHS 2.0 equipment for vertical form, fill and seal (FFS) machines.

Meanwhile, the thin gauge film offers a potential material reduction of 35-50% compared to blown LDPE films, and cost savings of up to 30%. The PHS 2.0 seal ing system includes servodriven sealing jaws, an active knife and two-sided heated sealing strips that reduces the required clamped film surface by up to 6.8% and increases the packaging speed by as much as 25%, up to 130 bags/minute. The latter is achieved by reducing the sealing and cooling times by 50% and 30%, respectively.
Walking the talk: advancing recyclability goals
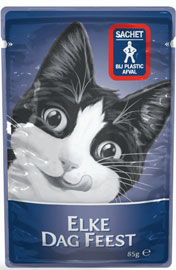
Among the key corporate goals to achieve sustainability is recyclability of the packaging product. Food company Nestlé has been vocal since 2018 about its goal to making its packaging 100% recyclable or reusable by 2025; and reducing use of virgin plastics by a third over this period. In 2019, the company said that it has already advanced to making 87% of its packaging recyclable or reusable.
The Switzerlanddomiciled conglomerate recently partnered with packaging producer Amcor to launch the world’s first recyclable retort pouch for pet food, using Amcor’s AmLite HeatFlex Recyclable solution. It makes its appearance in stores in the Netherlands in October.
The two companies say they worked closely dur ing the produc t development process, testing for heat resistance, machine performance, shelf-life and recyclability in the real world.
Flexible retort packaging is a modern alternative to metal cans and it can improve the carbon footprint of hundreds of consumer products, owing to its light weight, resource efficiency, ease of transportation, and by minimising food waste. Adding recyclability to its list of properties will further improve the environmental profile of this packaging solution, which has a reduced carbon footprint of up to 60%, say the firms.
Amcor also recently unveiled AmPrima PE Plus recycle-ready films, which are designed to be recycled, if clean and dry, through existing store drop-offs or curbside, where available. Currently available in a range of PE formats, AmPrima films show 60% reduction in non-renewable energy use; 46% reduction in carbon footprint; and 18% reduction in water consumption, based on an Amcor’s in-house LCA tool. Also, every million sq m of OPP displaced by AmPrima is equivalent to removing 45 cars from the road for a year.
Similarly, the partnership hatched between Chicago-based Conagra Brands and Indiana-headquartered packaging firm Berry Global has resulted in a sustainable packaging.
Read more...
(PRA) Subscribe to Get the Latest Updates from PRA Please click here
©2020 Plastics and Rubber Asia. All rights reserved.

©2020 Plastics and Rubber Asia. All rights reserved.
Home Terms & Conditions Privacy Policy Webmail Site Map About Us