Extrusion Technology
Die plate line with reduced lead time

Nordson Corporation says it has built a dedicated production line for BKG die plates used in underwater pelletising, enabling the company to deliver a new electrically heated die plate in only three weeks after order placement, including order entry, engineering, and production. This is less than half of competitors’ delivery times, it adds.
While most common die plates are on stock and can be delivered within a couple of days, building a new plate requires a range of engineering and manufacturing steps. By creating a database of standard designs, Nordson claims it has eliminated upstream engineering processes that had contributed to longer lead times. To reduce manufacturing time, it has dedicated a complete production line to die plates. The line is part of a new facility for BKG pelletising and melt delivery products completed in Münster, Germany, last year.
While the dedicated line produces only two-piece, electrically heated die plates in the BKG A, AH, Compact, and AHD190 families, these standard designs constitute the largest share of Nordson’s die plate output.
Die plates are wear components which periodically must be refurbished or replaced in order to maintain required levels of productivity and product quality. The BKG A, AH, Compact, and AHD190 families of die plates are available with the most common nozzle bore diameters. Optional features include several different carbide inlays, thermal insulation layers, pressure reduction, staggered rows of nozzle bores, and both standard and short land lengths.
Kuhne’s triple-bubble line for recyclable barrier film

Mono-material film structures are a modern solution for applications that require both high performance and environmental attributes, but the production of full polyolefin (PO) films poses challenges for plastics processors. They have to adapt and expand their manufacturing equipment and meet all the requirements of the food industry.
Now, with its triple bubble technology, Kuhne Anlagenbau from St. Augustin, Germany, offers a solution for the economical production of uniformly oriented highquality mono-material films that are directly sealable.
“We have been building Triple Bubble blown-film lines for over 20 years and, thus, have an enormous wealth of experience both in terms of machine technology and formulation development,” said Jürgen Schiffmann, Managing Director of Kuhne Anlagenbau. “We have transferred this know-how to five-layer fullpolyolefin film structures, an alternative that has many advantages over conventional blown-film lines with machine direction orientation (MDO) stretching units.”
Kuhne has tested and optimised the five-layer structure at its in-house technical centre on a 13-layer triple-bubble R&D line, with an output of around 250- 300 kg/hour for a maximum double film width of 900 mm. Kuhne says the result is a uniformly oriented film with a full PE or PP barrier film structure. The primary advantages of these film structures are their sealability and the waste-free production process, it adds.
With most packaging solutions today involving a barrier function, especially when it comes to food products or pet food, the term mono-material is somewhat misleading, explained Schiffmann. “All commercially available full-PO films contain up to 5% of foreign material in order to achieve the desired barrier properties.”
In Kuhne’s solution, the sealing layer consists of materials such as metallocene PE or plastomers, and the inner EVOH barrier layer is enclosed by two PE-based tie layers and a HDPE blend is used for the outer layer.
“With the same line configuration, we can also produce a mono PP film without any modification,” emphasised Schiffmann.
The technology is just as flexible in terms of the film thickness, which can vary between 15-150 microns, and its film properties. Film shrinkage is also adjustable, depending on whether the film is to be used for standup pouches, coffee and snack packaging, which require non-shrinkable films, or for lid films, which require slightly shrinkable films. Bottom web film for food packaging can also be designed to be thermoformable and even deep-drawable and shrinkable for form-shrink applications.
Kuhne says its solution also eliminates the need to laminate an MDO film with a sealing layer, which is usually necessary. “Our films are directly sealable and can be processed further,” says Schiffmann, adding another economic and ecological argument for the production of mono-material film structures with the triple bubble technology.
Colines’s stretch film with 60% PCR
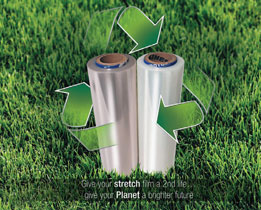
Italian extrusion machinery maker Colines says it has made big steps towards the path of recycling having run tests on post consumer recycled (PCR) material film, in cooperation with materials maker ExxonMobil.
“We performed very high quality reels, both with a wide range of thicknesses and percentages of recycled materials. We reached up to 400% ultimate pre-stretch value (ultimate strain) on a standard film production. Even when using a very high grade of recycled material, the reels offered good optical and mechanical qualities, perfectly suitable for today’s new market requirements,” claimed Nicola Lombardini, R&D Manager. He added, “This is impressive as we used up to 60% of PCR. Our cooperation with ExxonMobil provides us with the confidence to achieve further milestones in the near future.”
Meanwhile, Colines’s Executive President/Co-founder Eraldo Peccetti furthered, “After having made perfect reels with up to 90% of PIR (post industrial recycled) material, we had a further proof of the flexibility of our ALLrollEX lines in production.”
Lombardini also explained that the ALLrollEX lines are equipped with the newly designed GDS (gel down screw) screws and the in-line refeeding system BigMouth.
Read more...
(PRA) Subscribe to Get the Latest Updates from PRA Please click here
©2020 Plastics and Rubber Asia. All rights reserved.

©2020 Plastics and Rubber Asia. All rights reserved.
Home Terms & Conditions Privacy Policy Webmail Site Map About Us