Country Focus: 2020, still a banner year for Thailand’s key industries
Thailand, Southeast Asia's second-largest economy and the world’s 19th largest manufacturer, is on track to achieving its high income status ambition by 2037 by leveraging competence in the automotive and medical devices industries, says Angelica Buan in this report.
In previous years, Thailand has tussled with weak exports resulting from the US-China trade war, further aggravated by a strong currency during the period and long-running political tensions. Its economic growth plummeted to nearly double between 2018 and 2019, from 2.4% to 4.2%, respectively, according to the World Bank. This year, however, has been hampered by the Covid-19 pandemic, enfeebling the world’s financial markets and indomitable economies, including that of Thailand. Recently, the resurgence of political unrest in the country is anticipated to further mar the economy.

The Thai economy is projected to regress by 5% in 2020, according to World Bank’s June country monitoring report, considering its openness to trade and its anchor to tourism, which accounts to about 15% of its GDP. General weak demand, globally and domestically, spurred by the outstretched lockdown measures, has impacted Thailand’s key industries including the automotive, travel, energy, manufacturing, and exports, to cite a few.
Mobility restrictions from the Covid-19 are starting to be eased and anticipated to jump start economic activities. By 2021, economic growth is expected to rise to 4.1%, and in 2022, to 3.6%; recovery to pre-Covid output levels is also augured in two years’ time, hinged on an effective economic response that will help affected sectors including the vulnerable households and businesses, the World Bank also reported.
As well, optimism can be gleaned from its two high-value industries, the automotive and medical devices, which despite the challenges the country is facing continue to thrive.
Banking on rebound of the automotive sector
The global automotive sector has struggled for some years but remains to be Thailand’s ticket to economic recovery. Thailand is Southeast Asia’s automotive hub, honing on its supply and logistics chain.
However, the pandemic has shaken up the industry with lockdowns resulting in reduced production in the first half of 2020 by a total 43.1% year-on-year, according to the Thai Automotive Institute data, with the Federation of Thailand Industry (FTI) estimating a 32.9% year-on-year slump in local car sales from January-August this year.
But even so, the Covid-19 crisis has not deterred investments activities. In September, Chinaheadquartered Great Wall Motors (GWM) signed a share sales and purchase agreement with General Motors (GM) to acquire GM’s production facilities in Rayong, Thailand. GWM intends to make Thailand its ASEAN production base for export of new energy vehicles and internal-combustion engine models. Production is planned to start in the first quarter of 2021.
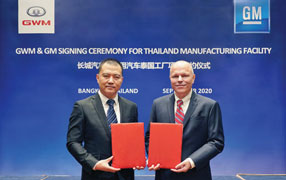
Elliot Zhang, President, GWM ASEAN & Thailand, added that the engine and vehicle production hub will be renovated and undergo system upgrades, upon the turnover of the assets as part of the signed deal.
This will enable GWM’s expertise and capability in SUV and pickup truck production, including advanced powertrain technologies, giving it the ability to produce internal combustion engine (ICE) vehicles and electric vehicles such as hybrid electric vehicles (HEVs), plugin hybrid electric vehicles (PHEVs) and battery electric vehicles (BEVs). Moreover, GWM says it will also invest in production automation technologies, such as AI, as well as R&D for Thai and Southeast Asian markets.
Meanwhile, the segment for advanced materials for automotive is also showing forward movement with German materials company Covestro, which has started up its operation of a new production line at the Map Ta Phut Industrial Estate.

Covestro’s new capacity for PC films in Thailand will serve the automotive, telecommunications, medical technology and ID document sectors. The project is the first step in a global expansion of Covestro's plastic film production, the company said, adding that the total investment of more than EUR100 million includes an expansion of the associated infrastructure and logistics to shorten delivery times. Covestro, which has 30 production sites worldwide, has been operating a production facility for specialty films in Thailand since 2007.
Green shoots in electric vehicles
Thailand’s foray in green transportation is also unfazed by the ongoing Covid-19 and volatile political situations.
The government, keen to reduce energy consumption in the transport sector, as well as support global climate change initiatives with EVs, has been incentivising EV production in the country.
Three agencies, Electricity Generating Authority of Thailand (EGAT), National Electronics and Computer Technology Centre (NECTEC), and the National Science and Technology Development Agency (NSTDA), also embarked on EV conversion of old vehicles. The agencies jointly studied and developed major parts used for modifying old vehicles into EVs. Modification for one vehicle costs not more than 200,000 baht, excluding the battery.
Meanwhile, an EV roadmap has been drawn, underscoring Thailand’s capability to becoming a vital EV and electric bikes hub in the Asian region by 2025. The target by then is to produce 250,000 EVs, 3,000 electric public buses, and 53,000 electric motorcycles. In 2030, ambition is to raise EV production to 30% of total annual car production.
An EV assessment report by Frost & Sullivan in January, covering 2018 through 2025, projected a CAGR of 21.6% for the EV market during the forecast period. The EV landscape has changed tremendously and at such a short time, with urbanisation as well as technological advancements in e-mobility as major growth drivers.
It is not surprising that adoption of EVs in Thailand continues to rise: in 2019, registration posted over 30,000 new HEVs/PHEVs, and over 1,200 battery electric cars and motorcycles; some 750 charging outlets were installed in 500 locations, according to the Electric Vehicle Association of Thailand (EVAT).

Relatedly, the Thailand Board of Investments (BOI) has recently approved 24 projects by car makers to produce EVs, HEVs, PHEVs, and battery electric vehicles (BEVs), with a combined capacity of over 500,000 units/year.
Among the approved projects include Mitsubishi Motors Thailand, which has earmarked 5.48 billion baht to upgrade the company’s existing car production line at Laem Chabang Industrial Estate, allowing the a production from 2023 of a total of 39,000 vehicles/year, consisting of some 9,500 BEVs and 29,500 HEVs. As well, Sammitr Group is investing 5.5 billion baht investment for the production of 30,000 BEVs at its Phetchaburi facility. Both projects are aimed at the local market and exports, mainly to other ASEAN countries.
Read more...
(PRA) Subscribe to Get the Latest Updates from PRA Please click here
©2020 Plastics and Rubber Asia. All rights reserved.

©2020 Plastics and Rubber Asia. All rights reserved.
Home Terms & Conditions Privacy Policy Webmail Site Map About Us