PRA Chinese
Rubber Journal Asia Injection Moulding Asia Energy, Oil & Gas Asia
VISIT OUR OTHER SITES:
PRA Chinese
Rubber Journal Asia
Injection Moulding Asia
Energy, Oil & Gas Asia
Recycling: No-waste solutions for waste plastics
Also, download this story from the electronic issue here
This article provides a round-up of the latest technologies and processes that suggest landfills, incinerators and the curb side are no place for waste plastics.
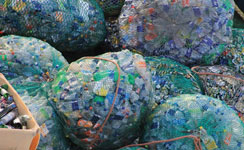
Recycling, a waste reduction strategy, is an important activity in the industry’s bid to reduce oil usage and carbon footprint, as well as recover valuable materials. In other words, sustainability will be driving the growth for recycled plastics in key industries, including packaging, consumer goods, textiles, construction, and furniture; with the list of applications growing as new postconsumer waste materials are developed.
Despite this cognisance for sustainability, recycling remains at a conservative level. The New Plastics Economy: Catalysing Action, a report by the World Economic Forum (WEF) and the Ellen MacArthur Foundation (EMF), cited that the current recycling rate stands at 14%.
The action plan backed by over 40 industry leaders from the global plastics value chain targets to increase recycling to over 70% of total plastic packaging. “As much as 20% of plastic packaging could be profitably re-used and 50% of plastic packaging could be profitably recycled if improvements are made to the designs as well as afteruse systems,” according to the environmental organisations.
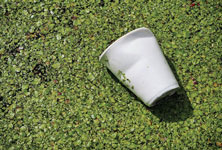
Nonetheless, the remaining 30% of bulk of plastic packaging (by weight), or 10 billion garbage bags/year that are heading to landfills and incinerators, require “fundamental redesign and innovation”, or else they will never be recycled.
While the basis of waste management requires conscientious human participation in the waste disposal process that includes recycling, reusing and recovery of materials, technologies can significantly aid in waste management efforts. Mechanical as well as chemical methods of recycling are just a few of the promising technologies that industries are exploring.
Treating hard-to-recycle materials with chemicals
Hard to recycle plastics do not have to hamper material recovery goals. Polystyrene (PS) wastes, for example, can be depolymerised using chemical recycling process being developed by US-based Agilyx Corporation, an environmental technology firm, and styrenics supplier Ineos Styrolution.
The companies recently inked a joint agreement for the development of a chemical recycling process in the US. With the technology, PS wastes are able to be recycled into virgin, high-quality styrenic polymers for food-related uses.
PS wastes vary in ease of recyclability. The rigid PS type is easier to recycle, since it is merely composed of PS resin with no air bubbles added. Thus, rigid PS can be melted and moulded into new products.
On the other hand, expanded polystyrene (EPS) is more stubborn to recycle, or less efficiently to do so, due to its composition of 98% air and only 2% resin material.
Likewise, offering a chemical-based solution, Dow Packaging and Specialty Plastics, a business unit of DowDuPont Materials Science, has formulated modifiers that facilitate hard-to-recycle packaging formats to enter the recycling stream.
Dow says its Retain polymer modifiers allow converters to recycle barrier film trim back into film production without sacrificing optical or physical properties.
Dow, a founding member of the Trash Free Seas Alliance (a global initiative led by the US non-profit organisation, Ocean Conservancy), is working with flexible packaging manufacturer Bemis Company and Canada-based converter Polykar to produce trash bags from postindustrial plastic scrap.
The post-industrial plastic scraps collected by Bemis are sent to Polykar, which uses its recycling machines to combine the reclaimed plastics with Dow’s Retain technology. The resulting material is a recycled plastic resin, which Polykar uses to manufacture the bags.
Meanwhile, UK-based Recycling Technologies (RT) is engaged in chemically recycling waste plastics, especially those mechanical recycling cannot treat. The technology it developed is housed in a chemical recycling unit called the RT7000 that is capable of treating 7,000 tonnes/year of mixed plastics from household, and commercial and industrial waste streams.
The firm says the technology has been employed successfully at the Swindon Material Recovery Facility (MRF) based in Cheney Manor (England) to recycle plastic waste back into a valuable low sulphur hydrocarbon product called Plaxx.
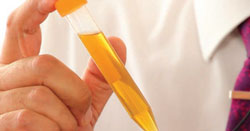
Plaxx can be used as a feedstock for new polymer and wax manufacturing, replacing fossil-fuel derived raw materials, RT states. “By combining mechanical and chemical recycling and working them in synergies, virtually all plastics from households, offices and shops can be recycled. Even materials that previously have been regarded as unrecyclable including black trays, laminated food pouches, films and contaminated food packaging can be processed,” RT said.
Extending use for waste composites
Composite materials are becoming a mainstream for engineering applications, owing to their high strength, durability, light weight and low maintenance. Demand is soaring from major industries like aerospace, automotive and wind energy. Thus, disposal and recycling systems for end-of-life composite products are needed.
Currently, new recycling mechanisms are being developed to enable recovery of as much composite materials as possible from used or aged products. There are quite a few that have shown potential for commercial utilisation.
Carbon fibre-reinforced (CFR) plastics, which are used in a range of applications from aviation to sporting goods, are difficult to break down or recycle. Yet, because CFRs are expensive, it is both practical and sustainable to recycle them, as well as recover valuable components from a product.
Hence, a latest work by the Washington State University (WSU) research team is timely. The WSU team said that certain composites like the ones used in airplanes, are thermosets; and these types of plastics are cured and cannot easily be undone and returned to their original materials.
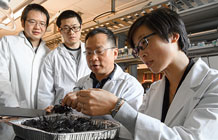
The patent-pending recycling method developed by the team led by Professor Jinwen Zhang uses mild acids as catalysts in liquid ethanol at a relatively low temperature to break down the thermosets. Zhang said it was the combination of chemicals that proved effective.
To break down cured materials effectively, the researchers raised the temperature of the material so that the catalyst-containing liquid can penetrate the composite and break down the complex structure. Ethanol is used to make the resins expand and the zinc chloride to break down critical carbon-nitrogen bonds.
Zhang states that it is critical to develop efficient catalytic systems that are capable of permeating the cured resins and breaking down the chemical bonds. In this method, the researchers were able to preserve the carbon fibres as well as the resin material in a useful form that could be easily re-used. The team is working to commercialise this process.
The Institute for Advanced Composites Manufacturing Innovation (IACMI) and the American Composites Manufacturers Association (ACMA) are also jointly offering a solution to recycle scrap and endof- life composites.
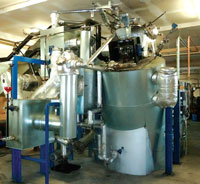
ACMA will head a team composed of Continental Structural Plastics (CSP), a US Tier One automotive supplier; CHZ Technologies, an American engineering company; A. Schulman, a plastics supplier; and the University of Tennessee, Knoxville; with support from composites manufacturer, Owens Corning, and speciality chemicals company Ashland.
Tom Dobbins, President of ACMA said, “End-oflife composites have a perception of being inferior to competing materials in terms of cradle-to-cradle sustainability because they are difficult to recycle or reuse. This research will counter that perception by providing strong technical evidence to the composites industry for the recyclability of end-of-life composites.”
The collaboration is expected to build a mechanical and thermal recycling approach that captures both the energy value and residual ash/fibre, which at the same time complements IACMI’s goal to create 80% recyclability of composites within five years.
Furthermore, the project also supports ACMA’s goal to reclaim glass and carbon fibre from fibrereinforced polymer (FRP) composite materials. The project will study and test CHZ Technologies’s pyrolysis technology called Thermolyzer.
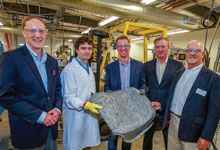
“Thermolyzer recycles all liquids, tars, and oils from composite materials and converts them into clean synthetic gases while recovering both glass and carbon fibres,” the partners said.
Very soon ACMA will be demonstrating the technology by processing fibreglass wind turbine blade samples at a Thermolyzer pilot plant in Germany. This process is also being applied to electronic circuit boards and other difficult-torecycle products.
In a related development, IACMI also provided tooling expertise to Washington-based Composite Recycling Technology Centre (CRTC) and ELG Carbon Fibre in making automotive seatbacks from recycled carbon fibre composites, which the partners showcased at a recent automotive materials summit held in Michigan.
The bucket-style seatback is 24-inch high and 19-inch wide, with side flanges of nearly 5-inch at their deepest, IACMI describes. The seat utilised 1.3 kg of ELG’s Carbiso TM PA6 60% SM45D. The recycled fibre/nylon 6 resin was moulded by CRTC in a hot compression cycle at 435°F, using its Wabash/MPI 300-tonne hot-platen press.
The seatback was moulded in IACMI’s aluminium tool that was previously developed for a pre-production prototype evaluation project.
“The goal of the project was to demonstrate manufacturability of the materials, to test flow and compaction into the various features, and to provide samples for non-destructive and destructive testing,” IACMI added.
Sustainable manufacturing in space
The NASA (National Aeronautics and Space Administration) crew on-board spacecraft follow a closed-loop system during space exploration because it is required that they recycle the limited water and air they use for survival. Specifically those on-board the permanent International Space Station (ISS), utilise a special equipment, a multi-function system called the Environmental Control and Life Support System (ECLSS), that can filter contaminants and impurities from wastewater (urine, sweat, or moisture from their breath) to be recycled into potable water.
This time, a latest NASA innovation recycles the 3D printed tools the ISS astronauts make in space. According to NASA, by 2018, the space agency will launch the Refrabricator, an automated device that can not only print plastic parts but can also recycle the pieces back into reusable raw materials.
NASA explains that the Refabricator, which is the size of a dormitory-room refrigerator, will accept plastic materials of various sizes and shapes and turn them in to the feedstock used to 3D print items.
“The Refabricator will be a key in demonstrating a sustainable logistics model to fabricate, recycle, and reuse parts and waste materials,” said Niki Werkheiser, Manager of In-Space Manufacturing at NASA's Marshall Space Flight Centre.
Washington-headquartered Tethers Unlimited Inc (TUI) has, for a number of times already, been contracted by NASA to build several in-space recycling technologies, including the CRISSP (Customisable, Recyclable ISS Packaging) technology for recyclable packing materials, such as bubble-wrap, foam, and custom 3D-printed boxes. It also uses the ERASMUS process for recycling, sterilising, and reprinting food-contactsafe utensils and containers aboard the ISS, to mention a few.
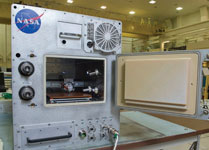
The Refabricator is expected to complete final flight certification testing at the Marshall Centre late this year, prior to its launch next year.
Evidently, more technologies and processes will be developed and will come on stream, as a result of the industry’s as well as end-users’ quest for earth – and space –friendly techniques to salvaging valuable materials like plastic.
(PRA)Copyright (c) 2017 www.plasticsandrubberasia.com. All rights reserved.