PRA Chinese
Rubber Journal Asia Injection Moulding Asia Energy, Oil & Gas Asia
VISIT OUR OTHER SITES:
PRA Chinese
Rubber Journal Asia
Injection Moulding Asia
Energy, Oil & Gas Asia
Production of biodegradable materials, a work in progress
Also, download this story from the electronic issue here
Environmental wastes need to be managed; and non-renewable resources (like fossil fuel) need to be preserved. These are but a few of the basis why the industry has nurtured an appetite for degradable plastics made from renewable sources, in this report on a round-up of the latest developments.
When the first generation polyolefin starchbased plastics introduced in the early 1990s failed to deliver its claim of degradability, let alone break down faster than non-biodegradables, an important lesson was learnt, that there is still more work to be done to achieve a nearly perfect biodegradable material.
Thus, experts and industry players are working together to discover more breakthrough materials that meet degradability expectations, with new materials developed to offer consumers a choice for sustainable products.
Green TPEs make the cut for cups and capsules
With the ‘green thinking’ rooted among Scandinavian and Nordic countries, Hexpol TPE offers biobased TPE and now Wildo Sweden is using it in its Fold-A-Cup camping cup. Hexpol TPE says it is continuing to trial new and emerging raw material combinations and further test the possibilities of its Dryflex Green TPE compounds. Because requirements vary for each application, there is a need for highly customised formulations, it said.
Together with Wildo, it developed a bespoke Dryflex Green TPE compound for the Fold-A-Cup and required it to display the correct behaviour during repeated folding and opening of the cup, to be flexible, yet rigid enough to withstand temperatures from hot or cold drinks. Other considerations were haptics and food contactcompliancy.
Wildo’s history started more than 35 years ago when
it developed the Fold-A-Cup
and Camp-A-Box reusabl e
outdoor utensi ls. At that
time, i t was pioneer in
contrast to the buy and
throw away- thought as
well as the heavy options
that were around. It has also preservered to keep the production in Sweden, and
resorted to recycling and re-using of boxes as well as
easy designed packages.
In a similar vein, Italian TPE maker API, which was acquired by materials company Trinseo in July 2017, has introduced a broadened portfolio of its Apinat bioplastics for single-serve coffee capsules, in a respite to the growing production of non-recyclable capsules, expected to reach 17 billion capsules by end of 2020.
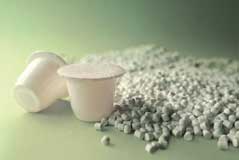
API launched new grades of biodegradable and compostable bioplastics, including TPE-E and TPC for compostable coffee capsules. It says Apinat boasts mechanical and thermal characteristics during the brewing process and can easily substitute conventional plastics. The new grades are suitable both for injection moulding and continuous compression moulding. The US FDA and EU food contact-compliant plastic grades are based on 60% to more than 90% of renewable resources, API stated. It also conforms to biodegradability standards of the European Bioplastics Association and standards like EU13432/EN14995 and US ASTM D6400.
Crustacean biomaterial subs plastic laminates
Penn State University researchers have developed an inexpensive biomaterial that can be used to replace plastic barrier coatings in packaging and many other applications.
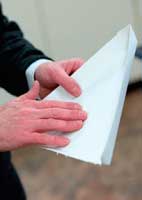
The fully compostable material, a polysaccharide polyelectrolyte complex, is comprised of nearly equal parts of treated cellulose pulp from wood or cotton, and chitosan, which is derived from chitin - the primary ingredient in the exoskeletons of arthropods and crustaceans. Chitin used for the biomaterial can be sourced from leftover shells from lobsters, crabs and shrimp consumed by humans.
According to the University, the environmentally friendly barrier coatings have numerous applications ranging from water-resistant paper, to coatings for ceiling tiles and wallboard, to food coatings to seal in freshness.
It boasts strong, insoluble adhesive properties, useful for packaging, as well as other applications like natural wood-fibre composites for construction and even flooring.
A key is the sturdy and durable bond between carboxymethyl cellulose and chitosan, two inexpensive polysaccharides that are already used in the food industry and in other industrial sectors with different molecular charges to lock together in a complex that provides the foundation for impervious films, coatings, adhesives and more.
The polysaccharide polyelectrolyte complex coatings performed well in research, the findings of which were published recently in Green Chemistry. The research team says that the results show that the materials may be competitive barrier alternatives to synthetic polymers and are working to develop commercialisation partners in different industry sectors for a range of product applications.
The work is funded by a Research Applications for Innovation grant from the College of Agricultural Sciences.
Fluorine from living cells to bioplastics
US scientists have genetically engineered a microbial host for organofluorine metabolism, allowing it to produce a fluoridated intermediate known as a diketide. As reported in the journal Angewandte Chemie, the diketide could then be used as a monomer for the in vivo production of fluorinated bioplastics.
The researchers said that natural organic compounds that contain fluorine are rare because living organism, with a few exceptions, do not produce them.
Fluor ine, an element that does not occur free in nature, is found in many agrochemicals, and about 20-30% of modern pharmaceuticals, ranging from antimalarial and cytostatic drugs to inhalation anaesthetics, blood substitutes, and liquid ventilation agents. Organofluorine molecules are also used in liquid crystals for displays, as well as ozone-friendly refrigerants and propellants.
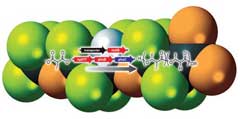
Given the potential for living systems to produce highly complex chemical compounds, researchers working at the University of California, Berkeley, aimed to manipulate the biosynthetic machinery in cells to use simple fluorinated building blocks to make new organofluorine target molecules.
To construct the diketide biosynthesis pathway, the scientists introduced genes that code for three particularly efficient enzymes from a variety of other microorganisms into the bacterium, Escherichia coli. These enzymes are able to use fluorine-containing derivatives of their normal substrates. In addition, it was also necessary to introduce a gene for a transport protein that carries fluoromalonate, as fluorinecontaining starting material, into the cell. The enzymes allowed the cells to use the biosynthesis pathway to make fluoromalonyl coenzyme A and convert it to the 2-fluoro-(R)-3-hydroxybutyrate diketide in high yield.
The researchers also int roduced another gene
for an enzyme used by many bacteria to make
polyhydroxyalkanoates (PHAs), which are polyesters
used to store carbon and energy. Biodegradabl e
PHAs are used in the production of bioplastics for
applications like food packaging and medical implants.
The new, genetically engineered microorganisms
incorporated the fluorinated diketides into the PHAs
they produced, generating polymers containing 5% to
15 % fluorinated monomers.
The fluorinated bioplastics are less brittle than f luor ine- f ree PHAs. Cont rol led incorporat ion of f luor inated monomers could al low for targeted variation of the properties of bioplastics, they said.
Upcycling waste into eco-friendly materials
Researchers from Murdoch University, Australia, have found a way to convert industrial waste into biodegradable plastic. The School of Engineering and Information Technology researchers Dr Damian Laird and Dr Leonie Hughes have been investigating an environmentallyfriendly solution for the use of oxalate, one of the major waste products of the alumina industry.
“We are interested in finding a use for carbon-based industrial waste, which is currently stockpiled or is difficult to treat,” Dr Laird said. The study, which was published in the Journal of Environmental Chemical Engineering, is inspired by the production of bioplastic from food waste and applying it to a toxic by-product of the alumina industry.
The team, after sourcing an initial bacterial culture from a local wastewater treatment plant, created a synthetic wastewater to understand the conditions required for bacteria to convert the oxalate waste product into the biodegradable plastic.
The research team is now identifying the suite of bacteria that can work in the process and examining ways to increase the amount of oxalate that is converted.
The output will be a naturally produced plastic that is biocompatible and completely biodegradable. “One of our goals is to 3D print products for the medical industry such as stents and sutures,” they said.
The team is also col laborat ing wi th Murdoch University’s Algae Research and Development Centre to look at using blue-green algae organisms that have a blend of bacteria and algae, to find a way to accelerate the process.
Likewise, embarking on a similar study, researchers at the University of Wolverhampton, UK, have turned waste plastic such as old water bottles into biodegradable resins for medical and consumer products.
Working with international partners, the university is pioneering what it calls the ‘King Midas’ approach, making different types of biodegradable polymers for use in agriculture, medicine and general household goods.
In this study, plastic waste is being converted into a pliable wax-like substance to which other elements can be added, turning it into a high-value, biodegradable form of bioplastic.
Dr Iza Radecka, Reader in Biotechnology at the University’s Faculty of Science and Engineering, and Marek Kowalczuk, Professor in Synthetic/Polymer Chemistry, are currently carrying out tests on the substance.
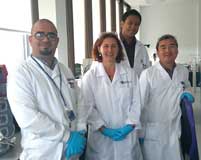
Used for the study are waste PE, which is a potential carbon source that could be utilised to make value-added biopolymers.
The researchers expounded: “Bacterial polymers such as PHAs are a group of biocompatible, environmentally neutral, biodegradable plastics that can be produced by certain bacteria. The structure of the PHAs can be adapted for a wide range of medi¬cal applications, especial ly implants, including hear t valve t issue engineering, vascular tissue engineering, bone and cartilage tissue engineering, as well as nerve conduit tissue engineering.”
The university is working in partnership with other institutions and companies, namely, The Centre of Polymer and Carbon Materials; Polish Academy of Sciences, and the Department of Chemical Organic Technology and Petrochemistry at Silesian University of Technology (Poland); Fraunhofer UMSICHT (Germany), University of Bologna (Italy), and UK-based recycling technology company Recycling Technologies.
The l ist of new biodegradable research and innovations, however, does not end here, as the quest for the Holy Grail of biodegradables continues.
(PRA)Copyright (c) 2017 www.plasticsandrubberasia.com. All rights reserved.