Recycling: ExxonMobil to expand US recycling capacity in US$200 mn investment; Mitsui Chemicals developing recycling technology for high-purity phosphorus materials
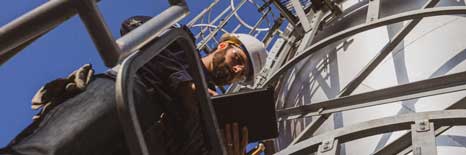
US materials firm ExxonMobil plans to invest more than US$200 million to expand its advanced recycling operations at its sites in Baytown and Beaumont, Texas. The new operations are expected to start up in 2026 and can help increase advanced recycling rates and divert plastic from landfills. The company plans to build additional units to reach a global recycling capacity of 1 billion pounds/year by 2027.
The investment will add 350 million pounds/year of advanced recycling capacity at Baytown and Beaumont, bringing ExxonMobil’s total capacity to 500 million pounds/year. The company is continuing to develop additional advanced recycling projects at manufacturing sites in North America, Europe and Asia, with the goal of reaching 1 billion pounds/year of recycling capacity globally by 2027.
ExxonMobil says it has advanced recycling customers in more than 15 countries across multiple sectors, including food-safe packaging and pet food, and demand is increasing.
Advanced recycling complements traditional, mechanical recycling by transforming plastic waste into raw materials that can be used to make many valuable products – from fuels to lubricants to high-performance chemicals and plastics. Advanced recycling can address a broader range of plastic waste that won't be mechanically recycled and may otherwise be buried or burned.
“We are solutions providers, and this multi-million-dollar investment will enhance our ability to convert hard-to-recycle plastics into raw materials that produce valuable new products,” said Karen McKee, president of ExxonMobil Product Solutions. “At our Baytown site, we’ve proven advanced recycling works at scale, which gives us confidence in our ambition to provide the capacity to process more than 1 billion pounds of plastic per year around the world. We’re proud of this proprietary technology and the role it can play in helping establish a circular economy for plastics and reducing plastic waste.”
The company’s first Baytown facility started up in 2022 and represents one of the largest advanced recycling facilities in North America, having processed more than 70 million pounds of plastic waste as of October 2024. ExxonMobil helped to form joint venture Cyclyx in 2021 to improve the collection and sortation of plastic waste.
In other news, Japan’s Mitsui Chemicals, says that, along with its wholly owned subsidiary Shimonoseki Mitsui Chemicals it has started developing the recycling technology required to produce high-purity phosphorus materials in Japan. The aim of this endeavour, it adds, is to recover phosphoric acid from underused phosphorus resources and turn it into high-value-added products in the form of high-purity phosphorus materials for reuse in manufacturing industry.
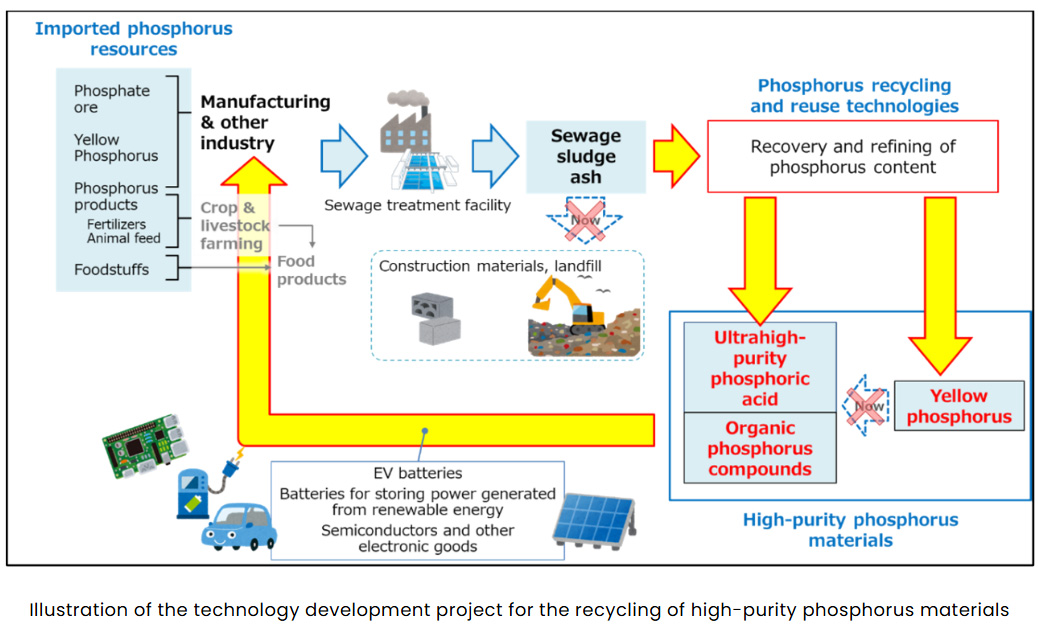
These development efforts are part of a jointly proposed project involving the National Institute of Advanced Industrial Science and Technology (AIST), Yoneyama Chemical Industry Co and Saga University that has been selected by the New Energy and Industrial Technology Development Organization (NEDO) for the Feasibility Study Program on Creation of New Industries and Innovative Technologies, following an open call for proposals.
High-purity phosphorus materials are essential to the formation of zero-carbon industries and societies, due to their utilisation in such items as electric vehicle batteries, semiconductors and batteries for storing power generated from renewable energy.
Made from phosphate ore, yellow phosphorus is a raw material common to the manufacture of these items. However, the technique still used today to produce yellow phosphorus was developed in the latter half of the 19th century and imposes a substantial burden on the environment.
Japan is entirely reliant on imports to cover its phosphate ore and yellow phosphorus usage needs. Given that securing a stable supply of phosphorus resources also comes with economic security risks, phosphorus has been identified by the Japanese government as a specified critical product.
This research project aims to reuse underused phosphorus resources – phosphorus-containing waste and by-products from Japanese manufacturing industry – as high-value-added products by recycling these resources into high-purity phosphorus materials. To this end, the project seeks to establish technologies that will enable the recovered phosphorus to be refined at the atomic and molecular level, and to be reused in a wide range of manufacturing fields.
Shimonoseki Mitsui Chemicals is Japan’s only company producing phosphoric acid via the wet process, while Mitsui Chemicals has its catalytic chemistry. Along with partners including institutions that have a knowledge of phosphoric acid or associated technical capabilities, these two companies intend to further the development of technology that will lead to the expansion of recycling applications for recovered phosphorus, whose use until now has mainly been restricted to fertilisers for the agricultural sector.
(PRA)SUBSCRIBE to Get the Latest Updates from PRA Click Here»