PU Expansions: Kumho Mitsui Chemicals starts up MDI facility in South Korea; Stahl opens PUD facility in Singapore
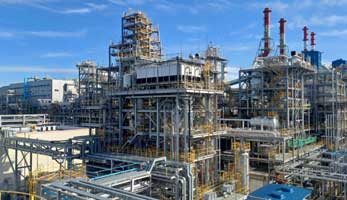
Japan’s Mitsui Chemicals has announced that its South Korean affiliate Kumho Mitsui Chemicals Inc. has commenced operations late September at additional production facilities for methylene diphenyl diisocyanate (MDI). The new facility will produce 200,000 tonnes/year, increasing the total capacity from 410,000 tonnes to 610,000 tonnes/year.
MDI is a key raw material for polyurethane, a signature material used in numerous fields such as auto parts, bedding and furniture, insulation for homes and fridges, elastic fibres, and various adhesives. Demand for MDI is projected to grow at an annual rate of 6% going forward on account of policy measures around the globe to improve residential insulation as a means of global warming suppression, as well as due to the heightened demand accompanying economic growth.
Kumho Mitsui Chemicals manufactures and sells high-performance monomeric MDI and modified MDI used for making auto parts, elastic fibres and synthetic leather, as well as commodity polymeric MDI used for making insulation materials. The newly implemented capacity increase is intended to accommodate increased demand growth for high-performance MDI – employed primarily in electric vehicles for the purposes of noise, vibration and harshness (NVH) mitigation – as well as the existing demand growth for insulation materials.
In addition to expanding its production facilities, Kumho Mitsui Chemicals will install recycling facilities that can reuse the by-products created during the manufacturing process as raw materials. This will not only aid in significant cost rationalisation by improving self-sufficiency for raw materials but will also reduce wastewater emissions from the plant and greenhouse gas emissions from the overall supply chain, it adds.
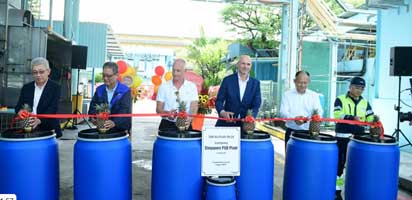
In other news, Stahl, a supplier of speciality coatings for flexible materials, has announced the opening of a new facility for the manufacturing of polyurethane dispersions (PUD) in Singapore. This strategic expansion is designed to better serve the growing demand in the Asian and South Pacific regions. The company did not state the capacity.
Historically, Stahl’s PUD production has been centred in Europe, with products imported into Asia to meet market demand. With the establishment of the Singapore facility, Stahl can now streamline its supply chain, reducing delivery times and improve service for its customers across the region.
Therefore, the shift underscores Stahl’s long-term commitment to investing in the region and supporting its customers with faster, more sustainable solutions tailored to the unique demands of the Asia-Pacific market, it adds.
The new facility will focus on producing high-performance polyurethane dispersions, which offer a range of beneficial properties critical for various industries. These advanced PUDs provide exceptional fastness, water resistance, print retention, and high flex durability, making them ideal for use in demanding applications.
PUD technology plays a key role in reducing solvent usage, making it an important component of Stahl’s broader sustainability strategy. By producing more water-based coatings, Stahl reduces the environmental impact of its operations, supporting the transition to more sustainable materials across industries. The Singapore facility will further explore renewable energy and bio-based formulations, advancing the company’s ESG goals and paving the way for future innovations.
Dennis Koh, Site/Operations Manager at Stahl Singapore, expressed the significance of this new development: “The new facility for PUD manufacturing in Stahl Singapore is designed to serve the Asian and South Pacific markets, spanning from China and Japan to New Zealand. This expansion supports our ESG goals by increasing the production of water-based coatings and decreasing solvent usage. With this new development, we can simplify our supply chain and shorten lead times for our customers. We are proud to include PUD in our service offerings, enhancing our technical capabilities to collaborate on challenging projects. I am extremely proud of my team who worked closely with the main contractor, Essential Engineering & Construction, to successfully complete this project in 18 months.”
(PRA)SUBSCRIBE to Get the Latest Updates from PRA Click Here»