Packaging: Curbing food wastes and cutting carbon emissions
Data shows that food waste contributes to carbon emissions, and sustainable packaging solutions appear to be an effective way to reduce this environmental impact, says Angelica Buan in this report.
Environment in a pickle with food wastes
Mouldy food in the fridge, unsold bags of spoiled produce from supermarkets, or fast-food wrappers and leftovers discarded on the curb, ready to be collected and sent to landfills: these are just some of the ways how food waste is generated and disposed of daily.

Now, imagine the daily volume of food waste sent to landfills, along with packaging, much of it contaminated, that cannot be recycled.
The World Wide Fund (WWF) reports that an estimated one-third of all food produced globally, ie 1.3 billion tonnes of fruits, vegetables, meat, dairy, seafood, and grains, is wasted. This food either remains on farms, is spoiled in distribution, or is discarded by businesses and households.
Food waste creates a double burden by contributing to both food insecurity and carbon emissions. The United Nations (UN) stated that nearly 1 billion tonnes of food, 17% of all food available to consumers, is discarded annually.
Producing, transporting, and allowing this food to rot contributes over 8% of global greenhouse gas emissions, particularly through methane production, according to UN’s “Food and Climate Change: Healthy diets for a healthier planet” report. When food waste is sent to landfills, it decomposes without oxygen, a process known as anaerobic decomposition, which produces methane: a greenhouse gas far more potent than carbon dioxide. In fact, methane accounts for about 58% of emissions from landfilled food waste, intensifying the impact on the climate.
Tackling food waste requires a variety of approaches, and one key strategy is adopting durable, biodegradable/compostable packaging, which resists damage and provides effective barriers as well as breaks down naturally, helping to reduce waste. Furthermore, other low-carbon-impact options are reusable or minimal-material packaging.
Using more packaging than necessary creates waste throughout the entire production process, from increased raw material use and energy consumption to more waste generation. While advocates for less packaging or even no packaging at all argue for reduced waste, this approach can pose risks to both consumers and the environment, especially in terms of carbon emissions.
The report also highlights that underpackaging can strain the system, resulting in food waste caused by spoilage or damage due to insufficient protection. The ideal solution is packaging that offers adequate protection, with innovations in biodegradable/ recyclable packaging continuing to grow.
Efficient barriers for longer shelf life
Efficient barriers in food packaging contribute to maintaining product quality, safety, and extending shelf life, to protect food from environmental factors such as moisture, oxygen, light, and microbial contamination. The significance of barrier properties cannot be overstated, as they directly influence the freshness, taste, and overall longevity of food products.
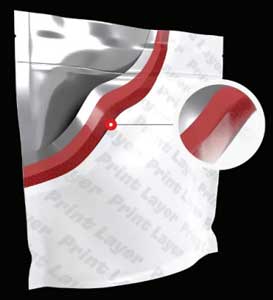
Advancing barrier innovations is the collaboration between US adhesives producer Henkel Adhesive Technologies and Indonesian manufacturer of CPP and LLDPE film, PT Panverta Cakrakencana (Panverta), to develop a sustainable solution for dry food packaging by improving the oxygen barrier properties of packaging films.
Packaging for products like flour, rice, and pasta typically uses multiple layers for protection, but these are hard to recycle. The collaboration aims to reduce the number of layers, cutting waste while still ensuring quality food protection.
The joint innovation between Henkel and Panverta, which advances mono-material PP packaging for easier recycling, focuses on optimising metallised CPP and aluminium oxide-coated (AIOx) films. These films achieve oxygen barrier performances of less than 0.5 cc/ sq m/day and 8 cc/sq m/day, respectively.
Henkel says its certified recyclable Loctite Liofol oxygen barrier coating enables mono-material packaging designs without sacrificing the essential oxygen barrier needed to preserve food.
Stretching to nylon as a lightweight material
Polyamide (PA)/nylon packaging is a strong, durable material with excellent barrier properties, ideal for food packaging. It protects against moisture, gases, and contaminants, helping extend food shelf life. Common uses include packaging for bakery items, meat, poultry, and dry goods.
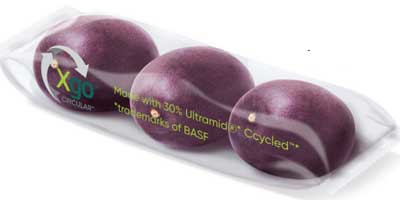
According to MarketsandMarkets, the PA food packaging market was valued at US$49.8 billion in 2021 and is projected to exceed US$72 billion by 2027, growing at a CAGR of 6.4% from 2022-2027, driven by the increasing demand for ready-to-eat and convenience foods that require effective packaging solutions.
In response to this market growth, non-profit Advanced Packaging Association (APA) AISBL was established in 2023. Founded by companies in the plastics sector such as Grupa Azoty ATT Polymers, BASF, Ube, Envalior, and Domo Chemicals, APA aims to highlight the key role of PA as a high-performance material for recyclable packaging applications by 2027, backed by scientific data.
In this context, German chemical producer BASF and Israel's packaging specialist StePac have collaborated to develop sustainable packaging for the fresh produce sector. BASF provides StePac with Ultramid Ccycled, a chemically recycled PA6, enhancing the flexibility of StePac’s contact-sensitive packaging and elevating its sustainability within the circular economy.
With REDcert2 certification, StePac incorporates recycled PA6 into its flexible, modified atmosphere packaging (MAP) products. The company’s brands, Xgo and Xtend, utilise MAP technology to control humidity, slow respiration, delay ageing, inhibit microbial decay, and preserve the produce's quality during storage and long shipments. Ultramid Ccycled makes up 30% of the packaging, with potential for higher integration.
-products.jpg)
Colombian passionfruit exporter Jardin Exotics is the first to use StePac’s Xgo packaging, which with MAP properties allow for slow ripening and preserve fruit quality during the long sea voyage from Colombia to Europe. By packing the fruit directly in retail packaging, repacking after arrival is eliminated.
Meanwhile, French resin manufacturer SK Functional Polymer (SKFP) offers Lotader recycling agents, which improve the environmental friendliness of plastics. Lotader is used to compatibilise plastic blends and enhance their mechanical properties. Recycled PA feedstocks are often contaminated with small amounts of PE, which can negatively affect the mechanical performance of the recycled compound, even at low contamination levels (10% or less). This leads to degraded performance, making it inferior to virgin PA.
To address this issue, Lotader 3410 was evaluated for improving the performance of PA/PE blends with 25% PE content. Lotader 3410, a terpolymer of ethylene, butyl acrylate, and maleic anhydride, has a high ethylene and maleic anhydride (MAH) content, making it an effective compatibiliser for PE in PA.
Its unique composition enables a fine dispersion of PE within the PA6 matrix, which is essential for maintaining strong mechanical properties. It can be added to PA6, PA66, or PA12 at concentrations between 2.5-10% to significantly improve impact resistance and PE compatibility.
(PRA)SUBSCRIBE to Get the Latest Updates from PRA Click Here»