Green tie-ups: Technip Energies/Enerkem to advance waste-to-sustainable fuels technology; Axens/partners to license Rewind PET polyester recycling process
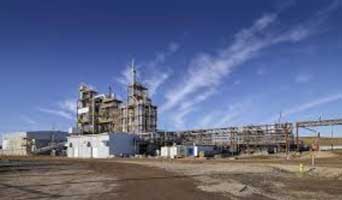
Engineering firm Technip Energies and Enerkem Inc have officially tied up to accelerate the deployment of Enerkem’s technology converting non-recyclable waste and residues into sustainable fuels and circular chemical products.
Enerkem’s groundbreaking gasification technology caters to hard-to-abate sectors such as aviation and marine fuels, providing sustainable fuel and chemical pathways. Under the terms of the agreement, Technip Energies and Enerkem will provide everything from strategic plant design and modularised project delivery services to clients, the firms say.
As Enerkem’s strategic partner, Technip Energies will contribute its expertise in engineering (incl. modularisation), technology integration (hydrogen, carbon capture, etc.) and project delivery to support joint development of such projects. The collaboration will focus on strategic efforts to further optimise design elements and industrialize the approach to offer a cost-effective solution.
Bhaskar Patel, SVP Sustainable Fuels, Chemicals and Circularity of Technip Energies, said: “We are pleased to deepen our relationship with Enerkem for the deployment of its technology platform to convert waste into sustainable fuels and chemicals. Together, we will leverage our design and engineering expertise to provide sustainable solutions using non-recyclable wastes as feedstock.”
Michel Chornet, CEO of Enerkem, stated: “We are pleased to expand our collaboration with Technip Energies to accelerate the deployment of Enerkem’s technology in Europe, North America, and the Middle East. Technip Energies’ deep experience in developing and executing projects in the energy transition sector will benefit our clients, helping them get projects to market faster, less expensively and more efficiently.”
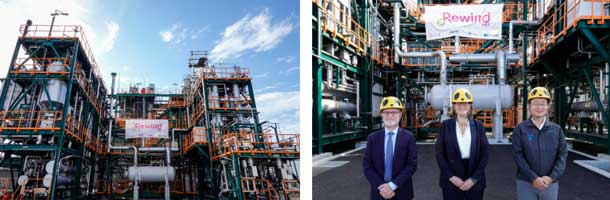
In other news, in line with the announcement made at the inauguration of a semi-industrial demonstration unit at Kitakyushu in Japan in 2023, materials firm Axens, French research firm IFPEN and Japanese recycler JEPLAN, partners in the project, have announced the launch of the commercialisation (licensing) by Axens of the Rewind PET process. This is said to be a major step forward for the three partners, concluding a successful one-year test period within the demonstration unit, which qualifies the performance of the technology, and will enable a further acceleration of the energy transition and the circular economy of plastics, which are at the heart of Axens' and IFPEN's strategy. Axens teams will now be able to market a complete Rewind® PET license package to their customers all over the world.
Axens, IFPEN and JEPLAN formed a strategic partnership in 2020 to develop this innovative chemical recycling process, which can be used to recycle all types of polyethylene terephthalate (PET) waste, especially the waste difficult to recycle mechanically. With the support of the French Environment and Energy Management Agency (ADEME), this collaboration resulted in the construction, commissioning and start-up of the semi-industrial Rewind PET unit in September 2023.
The validation and commercial launch of Rewind PET follows the positive outcome of a year-long program of tests carried out in the demonstration unit. This extensive large-scale test program demonstrated the effectiveness and reliability of the process while treating post-consumer PET waste. Results and launch are on schedule, in line with the ambitions announced by the three partners.
Axens says it is now in a position to offer a complete Rewind PET license package, including basic process design (which may be modularised), performance guarantees, supply of proprietary equipment and technical support for the start-up and operation of its customers' industrial units.
Rewind PET involves the continuous depolymerisation of PET by glycolysis, followed by in-depth purification of the resulting monomer, BHET (Bis(2-Hydroxyethyl) terephthalate). Its main advantage for manufacturers lies in its ability to separate all additives and colorants to restore a pure BHET monomer, which can be easily re-polymerised in existing (or new) polymerisation plants.
Recycled PET produced from the semi-industrial plant's pure BHET monomer has already received approval from several major companies in the food packaging and cosmetics sectors, underlining its potential for widespread market adoption.
In 2017, JEPLAN initiated operations at its KHP demonstration plant (1 kilotonnes/year) in Kitakyushu-city for clothes-to-clothes PET chemical recycling. In 2018, JEPLAN acquired its commercial plant (PET Refine Technology Plant, 22 kilotonnes/year) in Kawasaki-city, which restarted operations in 2021 and uses chemical recycling technology to manufacture rPET resin (bottle-to-bottle). PRT has more than ten years of experience in operating this plant.
(PRA)SUBSCRIBE to Get the Latest Updates from PRA Click Here»