Chemical recycling: another formula for a circular economy
Though chemical recycling is still a work-in-progress solution for plastic waste, with its environmental and economic viability largely debatable, there is growing market interest and innovations being undertaken.
Pros and cons of chemical recycling
Chemical recycling, or advanced recycling, is gaining traction for its ability to process mixed and hard-torecycle plastics that are often unsuitable for mechanical recycling. Unlike traditional methods, it breaks down plastics into basic building blocks to create new products or raw materials. Additionally, the process can produce high-quality outputs comparable to virgin plastics, making it suitable for applications with stringent standards, such as food and medical packaging.
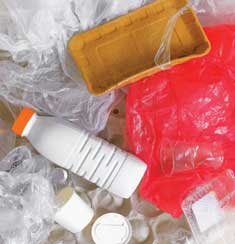
Despite these advantages, the effectiveness of chemical recycling has been questioned. A report by the International Pollutants Elimination Network (IPEN) and Beyond Plastics, two environmental NGOs, critiques the industry's claims. They argue that chemical recycling remains largely unproven, with evidence suggesting it could exacerbate pollution and contribute to climate change.
The report examined 11 US-based chemical recycling facilities, assessing their output, financial backing, and environmental impact, and found that the process may generate significant toxic waste and emissions, raising concerns about its overall environmental benefits.
Moreover, chemical recycling tends to be significantly more expensive than mechanical methods due to the sophisticated technology and high energy requirements. The economic viability of this process depends heavily on achieving large-scale operations, yet many existing facilities struggle with underutilisation.
Market growth: albeit slower than mechanical
Nevertheless, the market for chemical recycling continues to gain traction. It is projected to expand, growing at a CAGR of 9.4% from 2024-2030, according to a report by Grandview Research. Likewise, a report by UK-based intellectual property law firm Appleyard Lees shows a surge in patent filings for chemical recycling technologies.
Pyrolysis, the most common chemical recycling method, leads in patent filings, far surpassing other methods like gasification and hydrothermal treatment.
However, according to research firm ICIS, the chemical recycling and dissolution sector remains in a state of relative infancy, with around 130 plants operational or at the final investment decision stage of approval, compared to around 2,500 mechanical recycling plants.
Industry installed plastic waste processing capacity (pyrolysis-based technologies, chemical depolymerisation and dissolution) in Europe in 2024 stood at 150,000 tonnes/ year, or 510,000 tonnes/year if including facilities in the construction and commissioning phase, but the current pre-FID project pipeline could add 3 million tonnes by 2029, according to ICIS.
However, ICIS adds that several anticipated startups were delayed in 2023-24 due to a combination of factors, including permitting delays, access to feedstock, unfavourable macroeconomics and extended commissioning.
Mechanical vs chemical recycling
Meanwhile, mechanically recycled polymers' share of the total market is set to increase in the coming decades but penetration, defined as domestic recycling production versus total polymer demand, is likely to remain limited through to 2050, says Tom Brown, Chief News Correspondent at ICIS.
He adds that mechanical recycling domestic production is likely to represent 17% of total PE consumption in Europe, and 19% of PP by 2050, based on analysis of ICIS supply and demand data.
Rates in northern America and northeast Asia are likely to be similarly muted, according to ICIS analytics EMEA team lead for plastics recycling Egor Dementev.
Take-up of bottle grade mechanically recycled PET is likely to be stronger, at 49% in northern America and Europe, but technological issues limit the odds of greater market dominance for other polymers.
“The penetration rates still stay quite limited, as lots of plastics applications such as polymer flexibles and textiles are intrinsically difficult to recycle mechanically,” Dementev said.
The projected 2050 rates are minor uptick compared to 2023 mechanically recycled PE market penetration rates of 12% in North American and Europe and 4% in northeast Asia.
ICIS says in future, chemical recycling could fill in some of the gaps left by mechanical recycling.
“Chemical recycling could be a complementary solution,” Dementev said. “Without chemical recycling, we are probably not going to leapfrog,” he added.
The relatively small number of operational or approved plants, which are largely small-scale units, obscures the scale of potential capacity in the pre-approval phase at present, Dementev added. As for FIDs postponements, they are largely policy driven, according to Dementev.
Chemically recycled plastics: strong contenders for sustainability
Chemically recycled plastics are widely used across various industries, for example in the consumer goods sector, specifically in retail packaging for cosmetics, household items, and food packaging, rHDPE and rPET are used in containers, bottles, and films.
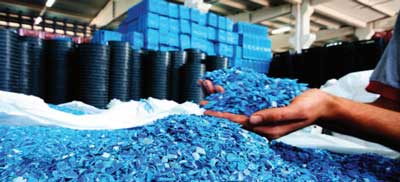
In the automotive industry, recycled plastics are used in interior and exterior parts, reducing weight and improving efficiency. In construction, they are used for insulation, roofing, and plumbing, offering durability and a lower environmental impact. The textile and fashion industries incorporate rPET fibres in clothing, accessories, and home textiles. Electronics manufacturers use recycled plastics in device casings and components, ensuring technical compliance.
In a pivotal collaboration, Brazilian petchem firm Braskem and Georg Utz AG, a Swiss company specialising in reusable transport packaging, have introduced chemically recycled ISCC Plus-certified PP to the food transport packaging market. Braskem says this is its first closed-loop project with Georg Utz, in a “collaboration that demonstrates the power of joint efforts in the value chain to create solutions that not only meet the highest standards for food transport packaging.”
(PRA)SUBSCRIBE to Get the Latest Updates from PRA Click Here»