Chemial Sector: Decarbonised chemicals, plastics gain momentum with multiple production pathways
by Joseph Chang, Global Editor, ICIS Chemical Business
Momentum is building in the zero-to-low carbon chemicals and plastics space with many different pathways to production that will give customers more options to reduce their carbon footprint.
There’s more than one way to skin a cat, as the English phrase goes. And so for the global decarbonisation challenge, all technologies and processes are on the table – carbon capture and storage (CCS), carbon capture and utilisation (CCU), biogenic CO2, green hydrogen, green methanol, e-naphtha and one day, direct air capture (DAC).
For now, we exclude recycled and bio-based plastics as these processes are already a bit more established.
For many new projects, offtake agreements will be critical, as decarbonisation is neither easy, nor cheap, as US materials firm Dow’s CEO Jim Fitterling has said.
With higher costs, the resulting decarbonised products would have to sell at a premium to conventional material – perhaps a considerable one early on – or be supported by government incentives. Or both.
Launch of Vioneo: fossil-free PP/PE
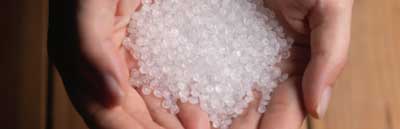
The latest splash in the pool comes from an industry ‘outsider’ - AP Moller, the parent company of shipping giant Maersk, as it launches Vioneo to “pioneer fossil-free plastics production”
The new company has designed a production process using what it calls an “innovative and proven technology” to produce fossil-free PP and PE at scale, using green methanol as a feedstock.
The EUR1.5 billion project in Antwerp, Belgium, would have capacity of around 300,000 tonnes/year of PP and PE, and could start commercial operations by 2028. Vioneo will start front-end engineering and design (FEED) in Q4 2024 with a potential final investment decision (FID) in 2025
To make green methanol, Vioneo would use biogenic CO2 and presumably green hydrogen from an electrolyser. Then presumably again, methanol-to-olefins (MTO) would yield propylene and ethylene, which would be polymerised to PP and PE.
The company claims its technology ensures a fully segregated and traceable supply chain, avoiding the mixing of non-certified and certified feedstocks. Production will also be powered by renewable electricity, significantly reducing greenhouse gas (GHG) emissions.
Vioneo said its PP and PP will save up to 6 kg of CO2 per kg of plastic and will be drop-in, virgin quality, suitable for applications across all sectors including medical appliances, home goods, automotive and packaging.
For the planned project to become reality, there are a set of conditions. The equity and debt funding will “depend on broad stakeholder support, including updated regulatory frameworks and policies supporting a competitive environment for fossil-free plastics, as well as better conditions for the European chemicals industry such as lower energy costs”, according to Vioneo.
“Furthermore, the success of the venture requires long-term offtake agreements of its customers,” it added.
The newly launched company said is in advanced discussions with several major global brands, including those in healthcare, automotive, fast moving consumer goods (FMCG), beauty and home products.
Borealis, Infinium to use e-naptha for PPE/PE
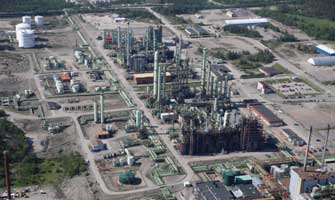
Another way to go is using green hydrogen and captured waste CO2 to produce e-naphtha which then can be fed into a conventional naphtha cracker to produce ethylene and propylene, and then PE and PP.
Austria’s Borealis earlier this year announced a partnership to source eNaphtha from eFuels producer Infinium to produce “ultra-low carbon footprint” PE and PP. It already started buying eNaphtha feedstock in Q2 and plans to offer commercial quantities of lowcarbon PE and PP starting in 2025.
Infinium is producing ISCC Plus-certified eNaphtha at its Project Pathfinder facility in Corpus Christi, Texas, US, and commercial eNaphtha volumes are being shipped to Borealis' facility in Porvoo, Finland.
Borealis’ Porvoo cracker has ethylene capacity of 400,000 tonnes/year, and downstream capacities include 102,000 tonnes/year of HDPE, 150,000 tonnes of LDPE, 153,000 tonnes/year of LLDPE and 220,000 tonnes/year of PP.
Infinium’s eNaphtha is made from captured waste CO2 and green hydrogen produced from renewable power. It is said to contain no sulphur and is produced without process emissions, according to the company.
(PRA)SUBSCRIBE to Get the Latest Updates from PRA Click Here»