Recycling: OMV to build chemical recycling plant in Austria; Ineos/Plastic Energy to build 100kt plant in Germany
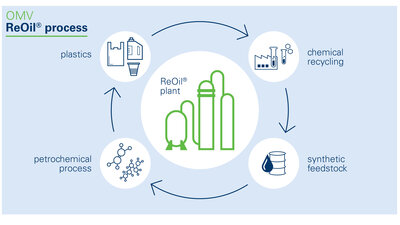
OMV, the Austrian integrated oil, gas and chemicals company headquartered in Vienna, has taken the final investment decision to build a chemical recycling demo plant, based on its proprietary ReOil technology, at its Schwechat refinery. With this, OMV is taking the next step toward an industrial-scale plant planned for 2026.
The patented chemical recycling technology, developed by OMV, converts plastic waste into synthetic feedstock, under moderate pressure and normal refinery operating temperatures, which is then primarily used to produce again high-quality plastics.
OMV was among the first companies to develop a chemical recycling technology for used plastics more than a decade ago.
A ReOil pilot plant has been operating in the Schwechat refinery since 2018, capable of processing 100 kg of used plastics into 100 l/hour of synthetic feedstock. The pilot plant has been running for a total of 13,000 hours since its commissioning and thus enabled an improvement in the thermal cracking process and supported the further scale up of the ReOil technology.
The current investment covers the construction of a ReOil demo plant with a design capacity of 16,000 tonnes/year at the OMV site in Schwechat, Austria. Production startup is planned for early 2023. To finance this project, OMV entered into its first-ever green loan agreement which is in alignment with the green loan principles and based on a green and project-specific external due diligence appraisal, so-called Second Party Opinion, and a project-specific green financing framework.
The demo plant will turn plastic waste that is not fit to be mechanically recycled and would otherwise be sent to waste incineration into a valuable resource. The feedstock will be sourced in Austria, in close cooperation with local waste management companies, and will consist mainly of polyolefins.
Examples of such plastic waste include food packaging, plastic cups, lids from takeaway coffee and confectionery packaging. Through the chemical recycling of plastics, OMV obtains a pure raw material which can again be used to produce virgin-quality base chemicals and plastics for all types of applications including packaging for the food industry and medical products, which must meet the highest quality and safety standards.
“The ReOil pilot plant has shown that we are on the right track with our in-house developed technology and with our efforts in this field. We are confident that chemical recycling can complement the available mechanical recycling technologies and that it represents a sustainable and profitable solution. With the decision to build a demo plant, we are now taking the next step toward circular economy and thus toward reducing our CO2 emissions,” said Alfred Stern, CEO/Chairman of the Executive Board of OMV.
The plant will be fully integrated within the petrochemical site at the Schwechat refinery, enabling OMV to guarantee the best use of resources, maximum efficiency, and the highest industrial safety standards, while creating around 50 new jobs. It represents an important step toward developing ReOil into a commercially viable, industrial-scale chemical recycling technology with a processing capacity of up to 200,000 tonnes/year by 2026.
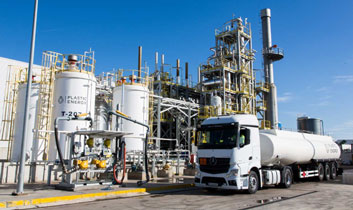
In other news, UK companies Ineos Olefins & Polymers Europe and Plastic Energy, are tying up to produce 100,000 tonnes/year of recycled raw materials from plastic waste. This will be the largest use of Plastic Energy technology on the market. Production will be based in Köln, Germany. Plastic Energy’s patented Tac recycling technology will turn difficult-to-recycle plastic waste otherwise destined for incineration or landfill, into a valuable raw material Tacoil, a Plastic Energy product that can be used to create virgin-quality polymers.
Ineos will also invest in technology to process the Tacoil further before feeding it to its steam crackers, where it will replace traditional raw materials derived from oil. This use of advanced recycling enables plastic waste to be turned into new, virgin-quality materials that can be used in demanding applications where safety standards require the highest level of product purity and performance, says Ineos.
As well as reducing the risk of plastic pollution and the use of fossil-based raw materials, the circular re-use of ‘end of life’ plastic will also help to reduce total emissions, supporting the transition to net zero.
Ineos and Plastic Energy first announced a collaboration to explore the construction of a commercial scale plant in 2020. Working together Tacoil has already been successfully converted into virgin-quality polymer through the Ineos cracker at Köln, Germany, and used by selected customers and brands to demonstrate the viability and demand for materials from advanced recycling. As a result, Ineos and Plastic Energy have extended their partnership. Production is targeted for the end of 2026.
Rob Ingram, CEO, Ineos O&P Europe North, said: “Advanced recycling is an essential part of the solution for turning plastic waste into materials that can be used for demanding applications. Our position is that advanced recycling has to be done at scale in order to make the process environmentally and commercially viable.”
Carlos Monreal, Founder/CEO of Plastic Energy, said: “We are pleased to announce this project with Ineos to further scale our portfolio of plants in Europe. Tacoil from our recycling process has already been used in products that have been commercialised on the European market, and we look forward to working with Ineos to enable the production of more recycled content.”
Using a mass balance approach, an independent, third-party organisation such as ISCC or RSB will certify that fossil-based feedstocks have been substituted by the new, recycled materials and ensure that recycled benefits are being accounted for correctly. A mass balance approach enables co-processing of circular and fossil feedstocks, a key step in the transition to a circular economy.
(PRA)
Subscribe to Get the Latest Updates from PRA Please click here
©2022 Plastics and Rubber Asia. All rights reserved.
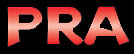
©2022 Plastics and Rubber Asia. All rights reserved.
Home Terms & Conditions Privacy Policy Webmail Site Map About Us