Recycling: Neste/Ravago jv on chemical recycling; Honeywell launches “revolutionary” recycling process
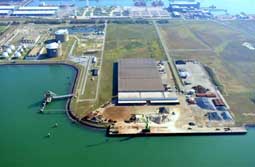
Helsinki-based sustainable materials firm Neste and Ravago aim to establish a joint venture to build an industrial facility for chemical recycling in North Sea Port in Vlissingen, the Netherlands. The facility is intended to be the starting point of joint global chemical recycling (often also called “advanced recycling”) activities, built upon the advancement of the thermochemical liquefaction technology of US-based Alterra Energy, a chemical recycling technology company. With this, Neste, the world’s leading producer of renewable diesel, sustainable aviation fuel, and drop-in renewable feedstocks and solutions for the polymers & chemicals industry, and Ravago, the world’s leading distributor and recycler of polymers, plan to demonstrate and advance the commercialisation of chemical recycling. The transaction is awaiting for and subject to regulatory approval.
This strategic partnership combines Ravago’s expertise in the mechanical preparation of plastic waste, Alterra Energy’s proprietary liquefaction technology, and Neste’s expertise in the processing of hydrocarbons. Neste and Ravago are aiming for a first industrial chemical recycling site in North Sea Port in Vlissingen with an annual processing capacity of about 55,000 tonnes of mixed plastic waste, corresponding to the plastic packaging waste generated by some 1.7 million average EU citizens per year. The long-term aspiration of the partners is to significantly increase the processing capacity on a global scale and continuously develop the joint venture into a global leader for chemical recycling of mixed plastic waste.
This targeted investment is the consistent continuation of the fast-paced progress in the cooperation between the partners. In 2019, Neste and Ravago set a joint target to reach the capacity to process over 200,000 tonnes/year of mixed waste plastic by 2030. Ever since, the companies have evaluated technologies, the raw material market, and built joint business cases to develop chemical recycling capacities. Already in 2020, Neste also successfully conducted the first of several industrial trial runs with liquefied waste plastic at its oil refinery in Finland.
In other news, technology firm Honeywell has commercialised what it says is a revolutionary UpCycle Process Technology that utilises molecular conversion, pyrolysis, and contaminants management technology to convert waste plastic back to Honeywell Recycled Polymer Feedstock, which is then used to create new plastics.
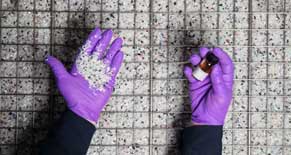
Sacyr, a Spain-based global engineering and services company with operations in more than 20 countries worldwide, will be the first to deploy Honeywell's proprietary UpCycle Process Technology. Honeywell and Sacyr will form a joint venture where the two companies will co-own and operate a facility in Andalucía, in Southern Spain, with a capacity to transform 30,000 tonnes/year of mixed waste plastics into Honeywell Recycled Polymer Feedstock. Production is expected to begin in 2023.
The UpCycle Process technology expands the types of plastics that can be recycled to include waste plastic that would otherwise go unrecycled, including coloured, flexible, multi-layered packaging and polystyrene. When used in conjunction with other chemical and mechanical recycling processes -- along with improvements to collection and sorting – Honeywell's UpCycle Process Technology has the potential to increase the amount of global plastic waste that can be recycled to 90%.
According to a study published by AMI International in September 2020, waste plastics processed through advanced recycling technologies, such as UpCycle Process Technology, could amount to between 5 and 15 million tonnes of additional plastic waste being recycled per year by 2030.
Recycled plastics produced via UpCycle Process Technology can result in a 57% reduction of CO2-equivalent (CO2e) emissions compared with the production of the same amount of virgin plastic from fossil feeds. The process also reduces CO2e emissions by 77% compared with conventional modes of handling waste plastic, such as incineration and landfilling2. These CO2e reductions are some of the largest improvements among all pyrolysis technology offerings.
Partnering with companies that have waste management experience such as Sacyr allows Honeywell to help close the loop within the plastics supply chain by bringing the recycling technology onsite to the collection source. The recycling plants employ a modular design, enabling straightforward deployment and installation, striking the right balance between economy of scale and amount of waste plastic generated locally.
Honeywell's UpCycle Process Technology was created within Honeywell's Sustainable Technology Solutions (STS) group, which is part of Honeywell UOP. This latest technology builds upon Honeywell's focus to deliver high impact, environmentally sustainable solutions for customers and society.
(PRA)
Subscribe to Get the Latest Updates from PRA Please click here
©2021 Plastics and Rubber Asia. All rights reserved.
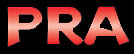
©2020 Plastics and Rubber Asia. All rights reserved.
Home Terms & Conditions Privacy Policy Webmail Site Map About Us