Recycling: Alpla starts up HDPE recycling plant in Mexico; Evonik/Vita partner in PU mattress recycling process
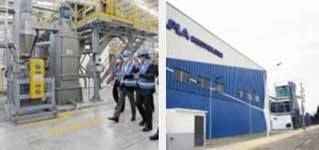
Packaging/recycling specialist Alpla Group has opened a new EUR20 million plant for HDPE plastic recycling in Toluca, Mexico. At the same time, the company has announced it will double its annual regrind material production capacity to 30,000 tonnes from the second half of 2022. Around 70 new jobs have been created at the plant, which will be run as a wholly owned subsidiary of Alpla.
The facility is currently designed for an annual capacity of 15,000 tonnes of recycled HDPE (rHDPE) in pellet form. This regranulate is mainly used for the production of non-food packaging such as personal care products and household cleaning agents. The demand for recycling material is so high in Mexico and Central America that the majority of the output will be used regionally.
Carlos Torres, Regional Manager Mexico, Central America and the Caribbean, explains: ‘We are seeing increasing momentum in the recycling market, taking one step forward in our commitment to sustainability, and the demand from our customers in the region for post-consumer recycled materials is rising. This is enabling us to already initiate an increase in our production of rHDPE in Toluca.’
Alpla has many years of experience in recycling post-consumer PET in Mexico. The first bottle-to-bottle recycling plant in Latin America, Industria Mexicana de Reciclaje (IMER), went into operation back in 2005. IMER is a joint venture between Alpla México, Coca-Cola México and Coca-Cola Femsa. By joining forces, the partners have established the infrastructure for collecting and recycling used PET beverage bottles over the past 15 years. They produce close to 15,000 tonnes of food-grade flakes from post-consumer PET a year.
In early 2021, the Alpla announced that it would invest an average of EUR50 million a year until 2025 in the ongoing expansion of its recycling activities. In particular, it plans to globalise its activities in the area of high-quality recyclates in order to close the materials cycle in as many regions as possible. In all, the annual capacity of the ALPLA recycling companies, joint ventures and partnerships amounts to approximately 130,000 tonnes of PET and 60,000 tonnes of PE.
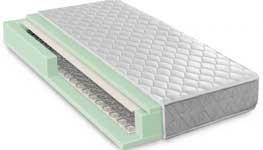
In other news, German materials firm Evonik says it has used its expertise in polyurethane (PU) chemistry to develop an efficient chemical recycling process for converting flexible PU foams back to the original polyol raw material. Evonik’s new hydrolysis recycling process has the potential to achieve circularity in the flexible PU foam industry.
As the next phase of the development, Evonik will scale-up trials of its new process, which has been further strengthened by its partnership with the Vita Group, a provider of value-added and differentiated flexible PU foam products. Vita has trialled the recycled polyols from Evonik's hydrolysis process in several of its flexible foam applications.
According to the latest report from EUROPUR (European association of flexible polyurethane foam blocks manufacturers), some 40 million mattresses are discarded each year in Europe alone, with the majority ending up as landfill creating the equivalent of 600 kilotonnes of waste: including more than 300 kilotonnes of PU foam. With the potential to recycle the main component materials used in flexible PU foams and PU foam-based mattresses, Evonik’s process offers significantly higher use levels of the recycled polyol compared with existing commercialised technologies.
Evonik’s solution will contribute to the global flexible PU industry’s sustainability expectations of reducing waste and increasing the use of renewable raw materials in the production of its products. This enables Evonik to expand its position as a leading solutions provider for the PU industry and supports the entire Evonik Group’s objectives of establishing a fully functioning circular economy.
“It’s only by recycling products back to their raw materials and reusing them over and over again that we will enable a fully circular economy,” said Ralph Marquardt, Head of Evonik’s polyurethane additives business. “Our new hydrolysis process delivers recyclates of a quality and performance similar to that of virgin raw materials. Thus, innovative foam producers like our partner The Vita Group can meet their own sustainability targets, while continuing to deliver high-quality PU products.”
“The Vita Group is renowned for our long-history of innovation in sustainability and investing in circular economy products. We recycle and rebond over 30,000 tonnes of trim each year, as part of our dynamic sustainability agenda,” said Ian W. Robb, Group CEO for The Vita Group. “Sustainability and innovation are central principles of every aspect of our business. We see it as our responsibility to be at the vanguard of the development of eco-friendly technology within our industry. This hugely exciting partnership represents a key milestone on our journey to achieving the circular economy we are all striving for, and we look forward to working closely together with Evonik.”
(PRA)
Subscribe to Get the Latest Updates from PRA Please click here
©2021 Plastics and Rubber Asia. All rights reserved.
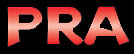
©2020 Plastics and Rubber Asia. All rights reserved.
Home Terms & Conditions Privacy Policy Webmail Site Map About Us