Chemical Industry: Chemical recyclers using other feedstocks to avoid competing with mechanical
By Mark Victory - Senior Editor, Recycling at ICIS
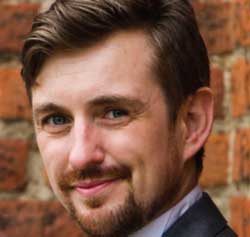
The increased use of partially sorted 90% mixed polyolefin bales by the mechanical recycling sector is pushing pyrolysis-based chemical recyclers towards other feedstocks to avoid competing with the mechanical recycling chain.
Pyrolysis-based chemical recyclers are increasingly investigating the use of PVC-screened reject bales, which currently predominantly serve the refuse-derived fuel (RDF) market, to avoid direct competition with the mechanical recycling sector.
Although there is an absence of comparable life cycle assessments (LCAs) that can show the environmental impact of chemical recycling compared with mechanical recycling, virgin production and alternatives, it is broadly agreed that mechanical recycling has a lower environmental impact than chemical recycling.
Because of this, many chemical recyclers aim to avoid material that can be efficiently used in mechanical recycling to ensure that the processes are complimentary.
In 2021, mechanical recyclers have been increasingly using mixed polyolefin bales – typically with a minimum 90% polyolefin content - because of a shortage of sorted monomaterial polyolefin bales,. These are the same mixed-plastic waste bales that chemical recyclers have, until now, predominantly been sourcing.
There are a variety of reasons why monosorted bale supply is tight, including:
- Substitution of virgin in the first half of the year due to shortages in that market
- Changing virgin plastic packaging material choices, the impact of COVID-19 on sorting centres
- Structural shortages of collection and sorting capacity
- Projects delayed by the onset of the coronavirus pandemic
- Additional demand ahead of the introduction of plastic packaging taxes in Spain, Italy and the UK in 2023
- An extended construction peak season due to delays to project completion dates
- Ambitious sustainability targets from the packaging sector, which go beyond what is available at current collection, sorting and reprocessing capacity
With polyolefin bale shortages expected to last at least into 2022, mechanical recyclers sourcing mixed polyolefin bales is unlikely to prove a temporary phenomenon, until sufficient additional collection and sorting infrastructure is built.
The shift in mechanical recycling purchasing patterns is causing pyrolysis-based chemical recyclers to explore other mixed-waste bale grades, with RDF reject bales a primary focus.
Along with tight PVC tolerances, pyrolysis-based chemical recyclers also typically aim to limit PET content in a bale – because it needs transesterification to depolymerise and because it produces oxygen in the reaction – as well as nylon and flame retardant content.
As a result, they prefer lighter-fraction waste, which broadly matches what is currently being sent to RDF.
Limiting chlorine content in RDF-suitable reject bales is becoming more challenging for waste managers due to the increased presence of PVC content and the rising use of polyvinylidene chloride (PVDC) in products such as films and cheese trays.
At the same time, downstream tolerances are becoming stricter, with bales for RDF use needing to contain below 1% chlorine and bales for pyrolysis typically targeting chlorine content below 0.1% to prevent corrosion.
The move to alternative feedstocks is being aided by a relaxation in downstream petrochemical industry specifications for pyrolysis oil and an increased understanding that a purification stage will be needed at the refinery stage, several chemical recyclers said this week.
A relaxation in pyrolysis oil specifications allows chemical recyclers to widen the potential input feedstock. Historically, purity specifications for pyrolysis oil have needed to match virgin specifications.
Although this is expected to increase demand for this type of bale moving into 2022, it is yet to have an impact on prices in the market, which remain at broad parity with September levels.
Because of the cost of sorting, PVC-screened bales suitable for RDF typically sell at a positive value compared with materials recovery facility (MRF) reject bales, which companies are paid to take away but may contain a variety of contaminants, including non-plastics, and require onwards sorting. These typically trade at negative values.
PVC-free bales are currently trading at below €100/ tonne ex-works Europe, while MRFs continue to pay €90- 150/tonne ex-works NWE (northwest Europe) to have bales removed. The price MRFs will pay for unsorted bale removal is largely dictated by savings against gate fees and local disposal taxes.
Unsorted bales are typically used for burn-for-energy, but commonly require on-site sorting facilities to ensure the removal of PVC.
Because small items fall through the gaps in traditional sorting, some players estimate that there is as much as 70% usable polyolefins content in burn-for- energy reject bales and this is encouraging industry investment in sorting lines at incineration units to extract the usable waste – particularly for thermal depolymerisation use.
Legislation penalising waste incineration is expected to intensify in the coming years across Europe.
(PRA)
Subscribe to Get the Latest Updates from PRA Please click here
©2021 Plastics and Rubber Asia. All rights reserved.
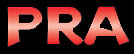
©2020 Plastics and Rubber Asia. All rights reserved.
Home Terms & Conditions Privacy Policy Webmail Site Map About Us