PRA Chinese
Rubber Journal Asia Injection Moulding Asia Energy, Oil & Gas Asia
VISIT OUR OTHER SITES:
PRA Chinese
Rubber Journal Asia
Injection Moulding Asia
Energy, Oil & Gas Asia
Composites are taking off in the aerospace industry
Also, download this story from the electronic issue here
Opportunities to build safer,more fueleconomical, and more cost-efficient aircraft structures and parts are on the horizon with composites.
The aerospace industry has witnessed an increasing use of composites in aircraft structures, including wings, fuselage, aircraft interiors, and other parts that are required to withstand survive extreme operating conditions such as high stress, shocks, and impact loads, according to a market report by Markets and Markets.
The report indicates that the aerospace industry sustains the continuing growth for advanced composites and is expected to hit US$38.41 billion by 2022. The requirement for high strength, low weight and corrosionresistant materials for use in the manufacture of new generation aircraft, such as Airbus A350 XWB and A320neo, and the Boeing 787 and 737 MAX, is instrument to the growing demand for advance composites.
Composites can reduce weight of aircraft between 20 to 50%. However, what could hamper the growth of the market is the high processing and manufacturing costs of advanced composites, as well as the lack of standardisation in advanced composite manufacturing technologies, the report disclosed.
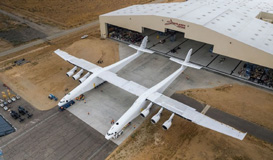
To date, the largest all-composite aircraft by wingspan, measuring 385 ft, is the Stratolaunch. Utilising six Boeing 747 engines for a payload capacity of over 227 tonnes and an operational range of approximately 2,000 nautical miles, Stratolaunch is capable of delivering payloads to multiple orbits and inclinations in a single mission.
In May this year, Stratolaunch conducted its first fuelling test; and in mid-September, it completed the first phase of engine testing. Stratolaunch is slated for its first launch demonstration as early as 2019.
Pushing the envelope with carbon fibre
Aluminium has been the primary material used in aircraft construction, taking up nearly 80% of the total weight of modern aircraft. The advent of advanced composites in aircraft, debuting in US fighter planes in the 1940s, ushered in the use of light weight yet robust materials such as carbon fibre.
The man-made composite materials, carbon fibre-reinforced (CFR) composites and glass fibre-reinforced plastic (GFRP), which typically consist of strong fibres in a tough resin matrix, offer the benefits of high strength, stiffness, toughness and low density.
Carbon fibres are almost five times stronger, yet three times lighter, and twice as stiff as steel, but have better yield strength, according to Frost & Sullivan. Adoption of carbon fibre in the aerospace industry leads to lightweighting and fuel efficiency. However, high costs of producing carbon fibre, as well as time and energy-intensive phases of the manufacturing process are discouraging mass adoption.
At any rate, aerospace specialists are on a materials development spree to latch onto the efficiency of carbon fibre.
Connecticut, US-headquartered Hexcel Corporation has launched a EUR8.35 million R&D project called Multi Axial Infused Materials (MAXIM), and is expanding its manufacturing facility in Leicester, UK, with a state-of-the art machine for carbon non-crimp fabrics development as well as laboratory equipment for research into this technology.
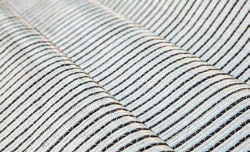
The four-year project, backed by the UK Aerospace Technology Institute (ATI) and match-funded by the Department for Business Energy and Industrial Strategy, will enable Hexcel to develop new carbon fibre fabrics for aircraft parts. Hexcel manufactures structural materials including carbon fibres, speciality reinforcements, prepregs and other fibrereinforced matrix materials, honeycomb, adhesives, engineered core and composite structures for use in commercial aerospace, space and defence and industrial applications. Commenting on MAXIM, UK’s Business Minister, Richard Harrington, said that it will enable composite structures such as aircraft wings and car bodies to be manufactured faster, greener and more cost-effectively.
“Composite structures are around 25-30% lighter than metal equivalents, delivering positive environmental benefits. For example, by making aircraft lighter, less fuel will be used and fewer CO2 emissions will be produced,” according to Hexcel.
The company, which will be working closely with Bristol-headquartered National Composites Centre, also explained the intricacy of making large aerospace composite parts. “Most large aerospace composite parts are made from prepregs where the carbon fibres and resins have already been combined. Converting this material into solid parts requires huge pressurised ovens, known as autoclaves. The MAXIM project will explore the manufacture of new carbon fibre fabric forms and resins that can be made into parts without using autoclaves.”
The aim is to enable complex metal structures, such as aircraft wings, to be manufactured from composites more cost effectively and at faster production rates, plus it will also develop composite parts for passenger cars, added Thierry Merlot, Hexcel’s President – Aerospace, Europe/MEA/Asia Pacific.
Segueing to a relevant development, cited in an aerospace composites market report by Global Market Insights (GMI), an emerging trend is seen in the segment of fibre recycling, which may be worth exploring.
The significant potential demand of reclaimed fibres, especially that of carbon fibre, can be attributed to the high value, recovered high strength, and high modulus aerospace grade fibres that retain better properties, says GMI’s report, which pegs a US$5 billion aerospace composites market by 2024.
Demand up for thermoplastic composites
Thermoplastic composites are replacing metal to meet the demand for energy savings, recyclability, and costefficiency. It is predicted that the industry, spooled up by the advantages offered by thermoplastics, will be increasing its use by manifold through the coming years.
Among the recent innovations in thermoplastic composites is a collaboration between Tods Aerospace and Technical Fibre Products (TFP), a UK-based high performance nonwoven materials manufacturer. The collaboration has yielded a solution for the dissipation of electrostatic charge in composite structures, specifically to overcome the limitations of current state-of-the-art products available in the market, and is tailored for composite applications in commercial and military aircraft fuel systems. Tods Aerospace, a Unitech Aerospace Company, says it is at the forefront of the UK supply-chain for thermoplastic composite aerostructures and interiors.
Sean Cooper, Materials and Manufacturing Development Manager for Tods Aerospace, explained that electrostatic dissipation is a requirement for nearly all glass-based composite materials used in fuel systems for modern composite-wing aircraft.
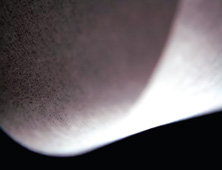
“Low-level electrical conductivity is required to prevent a build-up of static charge in the structure and prevent the propagation of electrical effects through the fuel system during an external lightning strike. This process of electrostatic management is an absolute necessity to ensure the safe operation of the aircraft.”
The newly developed material is compatible with aerospace qualified composite prepreg and provides high levels of sheet resistance (~0.1 to 5 MΩ/Square) on a normally insulating glass fibre based composite structure. The material is porous so it can be fully wetted by a prepreg resin system and is flexible so it can be incorporated either into the composite surface or placed inter-ply throughout the thickness of a complex composite layup.
Tods Aerospace said that it is undertaking further development to design and manufacture specific composite fuel system components and assemblies that incorporate this new and innovative technology.
In yet another thermoplastic composite exploit, Belgium-based EconCore’s thermoplastic honeycomb technology is expected to create a buzz. EconCore, the honeycomb sandwich panels and parts manufacturer, is extending its latest technology to develop next- generation solutions for aircraft interior modules.
Working with Germany-based Diehl Aircabin, a division of Diehl Aerosystems that specialises in cabin modules, crew rest compartments and air ducting, for a European Commission-funded project called InCom, EconCore’s thermoplastic honeycomb technology enables a new cost-effective process for creating modules by thermoforming and functionalising mono-material sandwich panels in a single step.
Both EconCore and Diehl Aircabin belong to the
InCom project consortium that consists of leading
European institutes and universities in biocomposites
and processing technology and sol-gel development,
together with a range of industrial participants from
seven European countries. The aim of the project is to develop economical viable production methods for
lightweight structures based on sustainable materials
for lightweight structural applications used in packaging,
land vehicles and aerospace.
The partners have produced a prototype of an aircraft stowage unit, which was showcased during the a composites exhibition held recently in September in Stuttgart, Germany.
The project highlights EconCore’s honeycomb production technology with a special grade of polycarbonate that has fire-smoke-toxicity performance. Test reports confirm the fire resistant behaviour of the final sandwich structures, which are said to cost significantly less than aramid and other conventional honeycomb solutions.
Commenting on the collaboration with Diehl Aircabin , Tomasz Czarnecki, COO of EconCore, says he anticipates further development of mono-material thermoplastic honeycomb sandwich panels that could be efficiently one-shot thermoformed and functionalised into final aircraft interior modules.
Super material graphene making waves in the air
Modern aircraft are aiming for ideal lighter, faster, and fuel-efficient flights. Achieving these with graphene increases adoption of 2D material in manufacturing aircraft components. The so-called super material (also called a wonder material), graphene has a single atom thickness, yet is more than hundred times stronger than steel, and an excellent conductor of heat and electricity.
The first aircraft wing built with graphene-enhanced carbon fibre was test flown in July last year. Prospero, the 3 m-wide unmanned airplane, is pioneering research collaboration between the University of Central Lancashire and the University of Manchester’s National Graphene Institute.
Evidently, graphene composites are starting a trend in the aerospace field. Sizing up its market potentials, research company GMI forecasts that the number of large commercial aircraft is expected to reach over 1,680 units, and be valued at US$200 million in 2024, from 1,430 units in 2016.
Meanwhile, a new project has been launched to research the viability of graphene-based composite materials.
The “smart composites” collaborative project of Swinburne University and Imagine Intelligent Materials (Imagine IM), an Australian developer of graphene-based applications for industrial textiles and fibres, will develop graphene-reinforced smart composites. These will be able to provide real-time information on the condition of large structures, enabling productivity gains by communicating requirements for service on an as needed basis in the transport sector and leading to significant commercial potential.
The project partners reason that graphene can ensure integrity of large composite structures that can degrade over time, affecting equipment performance and safety without being easily detectable.
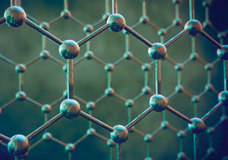
“The impact of graphene-enabled smart parts will be profound in the automotive and aerospace industries where composite wear and tear can be monitored on a continuing basis and servicing response can take place as a result of real time monitoring,” say the partners.
The US$20,000 grant-supported project will develop graphene ink coatings for glass fibres embedded in an epoxy matrix. The graphene composites used are highly conductive and sensitive to strain.
“Lightweight construction and function integration are the current major trends in the global mass transport sector, and this can be optimally realised through the clever design of fibre-reinforced composite materials,” according to research leader, Dr Nishar Hameed, noting that the integration of graphene is an efficient and viable way to achieve functionalities in composites to record and report the state of the component in service.
The project is expected to provide insights into the opportunities graphene composites will offer aerospace industries, as well as other industries that can use the “wonder” material’s performance.
(PRA)Copyright (c) 2017 www.plasticsandrubberasia.com. All rights reserved.