Green tie-ups: OMV/Borealis link with Tomra for recycling feedstock; Loop/Ester in jv to produce recycled DMT, MEG in India
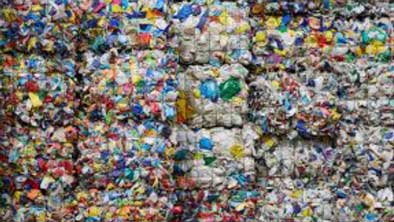
Austrian chemical firms OMV Group and Borealis have entered into long-term feedstock supply agreements for their recycling facilities with Tomra Feedstock, a subsidiary of sorting technology producer Tomra.
These agreements ensure a consistent supply of sustainable and high-quality raw materials for OMV Group’s recycling operations. OMV will process feedstock supplied from Tomra Feedstock plants in its ReOil plants in Austria, while Borealis will process feedstock produced by Tomra at its mechanical recycling operations in Europe.
The feedstock will be produced from mixed post-consumer plastic material otherwise lost to landfill and incineration at a first-of-its-kind sorting facility currently being developed by Tomra in Germany.
Tomra is a supplier of sensor-based sorting systems for metal and waste recycling and is currently building a sorting plant in Germany that will have an input capacity of 80,000 tonnes/year and be operational at the end of 2025.
Tomra Feedstock has pioneered an innovative process that transforms pre-sorted mixed post-consumer plastic waste – materials that would otherwise end up in incineration – sorted into clean fractions of specific polymer types. These fractions can then be further processed in mechanical and chemical recycling plants such as those run by OMV and Borealis.
Borealis will be using the feedstock at its operations based on Borealis’ Borcycle technology, which transforms polyolefin-based post-consumer waste into high-performance polymers suitable for demanding applications in industries including automotive, energy, infrastructure, healthcare, appliances and consumer products.
OMV operates a ReOil pilot plant in Schwechat, Austria, and a new ReOil plant with a capacity of 16,000 tonnes/year is currently under construction at the same site. Like the existing pilot plant, the new plant will have International Sustainability and Carbon certification (ISCC PLUS).
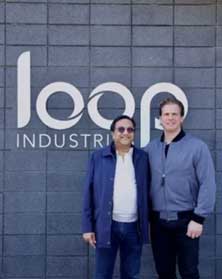
In other news, Loop Industries, a clean technology company that manufactures 100% recycled PET, has formed an agreement with Ester Industries Ltd, one of India’s leading manufacturers of polyester films and specialty polymers, to form a 50/50 India joint venture. The purpose of the India jv is to build and operate an Infinite Loop India manufacturing facility which will produce lower carbon footprint recycled dimethyl terephthalate, recycled mono-ethylene glycol and specialty polymers in India, using the Infinite Loop technology which is said to offer advantages over traditional mechanical PET recycling. Total capital investment is estimated approximately at US$165 million.
Loop and Ester have a well-established working relationship, with Ester producing Loop PET for Loop's global brand customers over the last four years. The India JV leverages the complementary skill set of each partner by combining Loop’s innovative technology and well-established global customer base with Ester's nearly 40 years of specialised polymer production, operational proficiency, and local expertise, including sourcing of PET plastic and polyester fibre waste feedstocks.
The Infinite Loop India facility is expected to produce 70,000 tonnes of rDMT and 23,000 tonnes of rMEG annually and Ester will toll convert the rDMT and rMEG into various grades of specialty polymers. The planned facility in India can lower carbon emissions by up to 70% compared to virgin DMT and MEG manufactured from fossil fuels, offering chemical companies a simple drop-in supplement and circular alternative that helps them achieve their sustainability goals.
The rDMT and rMEG product offerings manufactured at the Infinite Loop India facility represent a strategic product expansion in a low-cost manufacturing environment which complements Loop's existing PET plastic and polyester fibre manufacturing business and will fuel growth by addressing the large and growing demand in the market. This expansion enables the Infinite Loop technology to reach new markets and cater to a broader range of customers across multiple industries including the electronics, automotive, textile, cosmetics and packaging industries.
The India facility will leverage the Infinite Loop technology and existing engineering package which accelerates the lead-time towards groundbreaking, slated to occur by end of this year. Feedstock sourcing for the facility, in which there is abundant supply from textile waste in India, is well advanced and the partners have engaged an external firm to source and secure the land for the facility. Construction is expected to be completed by the end of 2026, with commercial operations commencing in early 2027.
Arvind Singhania, Chairman/CEO of Ester Industries Ltd. comments, “Ester and Loop have a long-standing working relationship with a deep alignment of values and shared commitment to circularity and driving sustainable change. This partnership reinforces our dedication to advancing sustainable solutions in the polymer industry and by leveraging Loop's technology alongside our decades of polymer production experience, we will contribute to reducing the carbon footprint of our products, meeting the evolving needs of our customers.”
(PRA)SUBSCRIBE to Get the Latest Updates from PRA Click Here»