Recycling: Xycle constructing recycling plant in Rotterdam; Teijin Frontier develops chemical recycling tech for polyester fibres
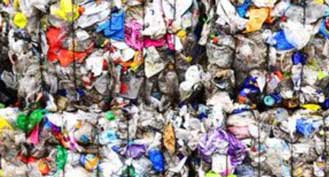
Xycle, a joint venture of NoWit, Patpert Teknow Systems and Vopa, will commence construction of a plant in the port of Rotterdam that will convert 20,000 tonnes/year of non-mechanically recyclable plastic. For this purpose, the Rotterdam Port Authority has leased a site at Rijndwarsweg in Europoort to Xycle.
Construction of this first Xycle plant is scheduled to start in the fourth quarter of 2022.
Xycle has been working for 14 years on a technique for converting on a large scale non-mechanically recyclable plastic waste into secondary raw materials of virgin quality through chemical recycling. This includes heating mixed plastic without adding oxygen. It does not burn, but disintegrates and can be used again as a raw material. Xycle’s technology has now been tried and proven. Xycle expects to receive the environmental and building permits in the third quarter. This means construction of the plant can start at the end of this year, and is expected to be operational in the fourth quarter of 2023.
Arjen Varekamp, on behalf of NoWIT & Patpert, “As initiators of Xycle, after years of preparation, it is a privilege to be able to translate our sustainable dream into the realisation of a Rotterdam circular project together with our strong strategic partner, Vopak.”
Marcel van de Kar, Global Director New Energies Vopak, “We’re very pleased with this milestone for Xycle and proud that Vopak is contributing to this. Developing new infrastructure solutions and setting up new supply chains in partnership is essential in the energy transition.”
Allard Castelein, CEO Rotterdam Port Authority: “Xycle setting up business in the port of Rotterdam fits in seamlessly with our strategy to help existing companies become more sustainable and to attract these kinds of new, circular companies.”
Xycle’s ambitions stretch beyond Rotterdam. In addition to this plant, which converts 20,000 tonnes of plastic into approximately 20 million l of liquid hydrocarbons (pyrolysis oil), Xycle wants to operate plants with a capacity of 80 to 100,000 tonnes/year. In addition, Xycle’s proven depolymerisation technology will be rolled out worldwide. In the coming years, Xycle says it wants to realise several of these larger plants in various locations in the world.
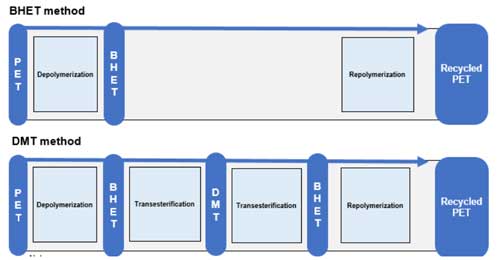
In other news, Teijin Frontier Co., Teijin Group's fibres and products converting company, says that it has developed a recycling technology using a new depolymerisation catalyst to recycle coloured polyester fibres without losing the quality of polyester fibres made from petroleum-derived raw materials.
The new technology also lowers environmental load compared to conventional recycling. The technology produces recycled materials equivalent to petroleum-derived polyester raw materials. Using a new depolymerisation catalyst for the conventional bis (2-hydroxyethyl) terephthalate (BHET) method, spent polyester is chemically decomposed and purified back into BHET intermediate raw material before being repolymerised into polyester.
The production process is simpler than using dimethyl terephthalate (DMT) and ethylene glycol in a transesterification reaction, so recycling is achieved with less energy consumption. Also, the new technology reuses resources such as wastewater, waste liquid and depolymerization catalysts.
Teijin Frontier will launch a pilot facility at its Matsuyama Plant and proceed with verification tests.
It adds it is also working to establish a mechanism for sustainable fibre-to-fibre recycling of polyester in cooperation with partner companies and consortiums both in Japan and global.
Compared to material recycling, which melts and moulds used products including PET bottles, DMT-based chemical recycling results in less deterioration of quality due to recycling, but its energy consumption is high.
The BHET method is often used when recycling from colourless and transparent PET bottles as new PET bottles, and also its energy consumption is lower compared to the DMT method, but there were difficulties in producing high-quality recycled polyester raw material because foreign substances, such as dyes used for coloured polyester fibres, could not be completely removed, resulting in discoloured recycled raw material.
(PRA)
Subscribe to Get the Latest Updates from PRA Please click here
©2022 Plastics and Rubber Asia. All rights reserved.
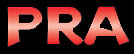
©2022 Plastics and Rubber Asia. All rights reserved.
Home Terms & Conditions Privacy Policy Webmail Site Map About Us