Green materials: Asahi Kasei partners Genomatica to trial biobased PA66; BASF closes EPS recycling loop with EPS containing recycled material
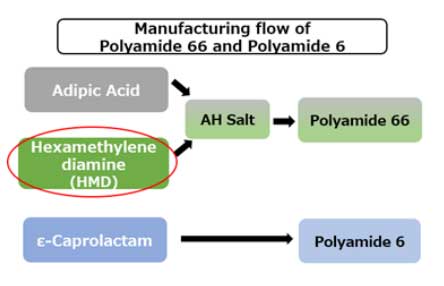
Materials company Asahi Kasei has formed a strategic partnership with US-based Genomatica regarding hexamethylenediamine (HMD) based on biomass-derived raw materials (bio-HMD).
Asahi Kasei currently uses fossil fuel–derived HMD as an intermediate to manufacture Leona polyamide 66 (PA66), an engineering plastic with heat resistance and rigidity.
PA66 is used for plastic parts in automotive and electronics applications, as well as yarn for airbag fabric. Demand is expected to increase worldwide. As the world moves toward carbon neutrality, attention is increasingly focused on solutions for reducing greenhouse gas emissions from chemical products derived from fossil fuels.
The strategic alliance with Genomatica provides Asahi Kasei with preferential rights to access the early volume of bio-HMD to evaluate the possibility as a feedstock of PA66, enabling Asahi Kasei to accelerate trials of PA66 made using biomass-derived intermediate. Genomatica has an established track record of commercialising manufacturing technology for various chemical products using biotechnology. By using this bio-HMD with its own PA66 polymerisation technology, Asahi Kasei aims to support its goal to be first-to-market with more sustainable PA66 made using biomass-derived intermediate for the automotive and electronics application of plastics components and industrial fibre.
Asahi Kasei moreover expects that this use of biotechnology will contribute to reaching its goal of becoming carbon neutral by 2050, while also alleviating the environmental burden throughout the life cycle of customers’ products. It adds that it continue to strive for adoption of biomass-derived intermediates for its engineering plastics in addition to PA66, while proactively utilizing recycled material, aiming to be a global sustainable partner for its customers.
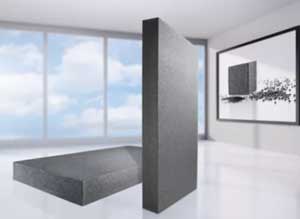
Meanwhile, in other news, Germany’s BASF has expanded its portfolio of graphitic expandable polystyrene (EPS) granulate. Neopor F 5 McycledTM contains 10% recycled material and is suitable for numerous applications in buildings, particularly facade insulation. The new raw material is produced using the extrusion process and offers the same proven mechanical properties and optimised insulation performance as Neopor F 5200 Plus.
BASF has developed the new raw material together with Karl Bachl GmbH & Co KG and turned it into a market-ready product. The quality of the recycled material used plays a pivotal role in meeting the exacting product demands in the various construction applications. This high quality standard is one of the keys to the success of the cooperation between BASF and Bachl. Both the recycled material used and the insulation raw material are REDcert2-certified. The recycled material comes from mechanically recycled EPS waste. Currently (Conversio study from 2019), at least 42 % of the EPS packaging waste in Germany is recycled.
The ambitious climate targets cannot be achieved without energy-efficient building envelopes. In both new construction and renovation projects, insulation materials made of Neopor are now standard in facade insulation. During their decades of use, they significantly reduce CO2 emissions from buildings.
“Closing material loops and reducing CO2 emissions are two of the priorities of current climate policy. Our sustainable Neopor insulation raw materials contribute directly to these efforts. With Neopor F 5 Mcycled, BASF can offer an insulation raw material with a closed EPS recycling loop for the first time. At the moment, high-quality recycled EPS material is still in limited supply. In the coming years, we want to work with our European partners to increase EPS recycling along the entire value-added chain and expand it to other waste streams. This will pave the way for more widespread use of mechanically recycled EPS in high-quality applications,” says Klaus Ries, Vice President Business Management Styrenics Europe at BASF.
With Neopor F 5 Mcycled, BASF adds it is expanding its EPS portfolio with an improved sustainability profile. The new raw material complements the mass-balanced products Styropor Ccycled and Neopor BMB, which are produced from alternative raw materials. For the production of Styropor Ccycled, fossil raw materials are replaced by pyrolysis oil, which is obtained from chemically recycled plastic waste. The pyrolysis oil is allocated to the subsequent end product via the mass balance approach. Styropor Ccycled has a significantly improved carbon footprint and contributes to the circular economy. In the production of the insulation raw material Neopor BMB, fossil raw materials are replaced by renewable feedstock using the biomass balance method (BMB). This reduces the carbon footprint of the insulation raw material by up to 90% in the production phase alone, compared with traditionally produced Neopor. At the same time, the insulation material retains all its proven product properties.
(PRA)
Subscribe to Get the Latest Updates from PRA Please click here
©2022 Plastics and Rubber Asia. All rights reserved.
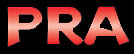
©2022 Plastics and Rubber Asia. All rights reserved.
Home Terms & Conditions Privacy Policy Webmail Site Map About Us