Tie-ups: FKuR/SKYi jv to produce biobased plastics in India; Toyo Ink/Itochu to partner in recycling scheme for multilayer packaging

After a decade of collaboration between Germany’s FKuR Kunststoff GmbH and India's SKYi Innovations, acting as distributors of the FKuR bioplastics range, both companies established SKYi FKuR Biopolymers Pvt Ltd joint venture at the end of 2019 to further strengthen their cooperation. Now, the companies have started local production of biodegradable, partially biobased plastics.
The production site is located within a special industrial zone in Chakan in the Pune district of the state of Maharashtra. This zone accommodates over 2,000 large and small companies.
The joint venture produces a significant part of the Bio-Flex product range for local demand as well as for distribution to neighbouring regions in Southeast Asia, including Thailand, Sri Lanka, Indonesia, Malaysia and Vietnam, as well as in Middle Eastern countries such as Dubai, Oman and Qatar. This makes the jv the first dedicated manufacturer of compostable biopolymer compounds in India.
Patrick Zimmermann, member of the executive board of FKuR Group explains this strategic step: "After our participation at Plastindia 2012, it was clear to us that the Indian continent is a strategically important bridgehead and a hub for our products in Asia and Africa as well."
The company also said the demand for compostable plastics is growing in these regions, with a focus on packaging and catering applications, as well as agribusiness, adding that compostable plastics can make a positive contribution to waste management in India, “as setting up organic recycling is infinitely easier and less costly compared to other disposal options (such as mechanical recycling or thermal recovery)."
The plant built for this purpose will employ up to 40 people in the first expansion phase. A modern compounding line is run on three shifts. In the company's own testing laboratory, which contains a small blown film line along with other equipment, the qualities of the incoming raw materials and the end products are monitored according to German standards.
Bio-Flex is a family of flexible bioplastics for a wide range of processing methods. They are fully biodegradable or compostable (according to EN 13432) and are based entirely or partly on natural raw materials. Main applications are flexible films, including agricultural, household and hygiene, as well as thermoformed and injection molded products.

In other news, Japan’s Toyo Ink SC Holdings, the parent company of the specialty chemicals manufacturing conglomerate Toyo Ink Group, and trading house Itochu Corporation have entered into a cooperative agreement to establish a plastic recycling scheme for the recovery and reuse of multilayer film packaging materials. Specifically, by using their respective technologies and business networks, the two firms will develop the materials technology needed to create real circularity of multilayer flexible packaging by making currently unrecyclable multilayer plastic packaging into a recyclable material by 2022. The collective goal is to boost the plastic material recycling rate to more than 40% in Japan and abroad. At present, the recycling rate in Japan is about 27%.
Recently, the waste problem of single-use plastics has been attracting global attention. In Japan, while about 16% of plastic waste is simply burned, buried, or otherwise processed without being reused, about 56% relies on incineration methods, such as the thermal recycling and heat reclaiming. Currently, large amounts of plastic are not recycled.

To address the plastic waste issue, in 2019, Toyo Ink, in cooperation with a leading environmental solutions provider, developed an innovative plastic recovery technology for multilayer flexible packaging, where a deinking coating agent and a delaminating adhesive are applied to the plastic film surrounding the ink layers. After use, the packaging waste is subjected to an alkaline treatment in which the coating agent, adhesive and interlaying ink layers are cleanly released from the film substrate. This results in the recovery of high-quality plastic material that can then be reused to create products of new value. A pilot plant based on this plastic recovery process is currently being built in Japan and is set to become operational later this year.
Under the agreement, Itochu will widely promote environmental solutions to food and daily necessities manufacturers, retailers and brand owners, by encouraging the development of packaging structures that use of this recycling technology and by promoting eco packaging design. In addition, Itochu will acquire exclusive marketing rights in Japan and preferential negotiation rights in Asia and Europe related to major product materials related to this recycling technology.
·(PRA)
Subscribe to Get the Latest Updates from PRA Please click here
©2021 Plastics and Rubber Asia. All rights reserved.
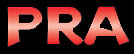
©2020 Plastics and Rubber Asia. All rights reserved.
Home Terms & Conditions Privacy Policy Webmail Site Map About Us