Greening: BASF to invest EUR4 bn to cut emissions by 25% by 2030; Evonik to generate sales of EUR350 mn by 2030 through circular plastics
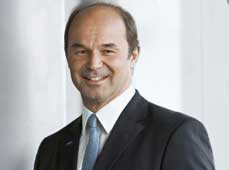
German chemical firm BASF says it is setting itself even more ambitious goals on its journey to climate neutrality and wants to achieve net zero emissions by 2050. It plans to invest up to EUR1 billion by 2025 to reach its new climate target and a further EUR2 billion to EUR3 billion by 2030.
Based on the most recent progress in developing low-emission and CO2-free technologies, the company is also significantly raising its medium-term 2030 target for reductions in greenhouse gas emissions: BASF now wants to reduce its greenhouse gas emissions worldwide by 25% compared with 2018 – and to achieve this despite targeted growth and the construction of a large Verbund site in South China. Excluding the effects of the planned growth, this means cutting CO2 emissions in half in the current business by the end of this decade.
In 2018, BASF Group’s worldwide emissions amounted to 21.9 million metric tons of CO2 equivalents. In 1990, this figure was roughly twice as high. The new 2030 emissions goal represents a reduction of approximately 60% compared to 1990 levels, which exceeds the European Union’s target of minus 55%.
“The new climate goals underscore our determination and BASF’s commitment to the Paris Climate Agreement. Climate change is the greatest challenge of the 21st century. In response, we must adapt our processes and our product portfolio. We need to accelerate this transformation now. We must first concentrate on the initial steps of this journey, not the final ones. That is why BASF will increase its use of renewable energies. And we will accelerate the development and deployment of new CO2-free processes for the production of chemicals. With transparency and offerings to systematically and incrementally reduce the carbon footprint of BASF products throughout the entire value chain, we help our customers in all industries to reduce the carbon footprint of their own products,” said Dr. Martin Brudermüller, Chairman of the Board of Executive Directors of BASF SE.
At the heart of the long-term transition toward net zero CO2 emissions by 2050 is the use of new technologies, which will replace fossil fuels such as natural gas with electricity from renewable sources. Most of these technologies are being pioneered by BASF in collaboration with partners and are currently in a pilot stage. Broad scaleup of these technologies will only be fully realisable after 2030.
One of the most important new technologies that BASF is currently developing are electrically heated steam crackers for the production of basic chemicals such as ethylene, propylene and butadiene. These chemicals are building blocks for numerous value chains and are essential for chemical production. Hydrogen is another important feedstock for many chemical production processes. To achieve CO2-free production of hydrogen, BASF is pursuing two processes in parallel: the commercially available water electrolysis and methane pyrolysis, for which BASF has developed a new process technology. Another important lever to increase energy efficiency is the use of electrical heat pumps to produce CO2-free steam from waste heat. BASF’s goal is to work with Siemens Energy to gradually ramp up this technology to industrial scale and use it for waste heat recovery at entire sites.
It also expects that this switch to climate-neutral production processes will lead to a sharp increase in electricity demand at the group’s major sites, including the largest production site in Ludwigshafen, in the coming decade. From around 2035, the group’s electricity demand is expected to be more than three times higher than it is today.
In addition to the planned investments in renewable energies, BASF is pursuing a number of specific flagship projects:
- Together with Sabic and Linde, BASF is working on the realization of a pilot furnace for the world’s first electrically heated steam cracker. Compared to conventional crackers, this would enable nearly CO2-free production of basic chemicals. If the necessary funding is granted, start-up of the pilot plant is slated to begin as early as 2023.
- BASF is developing methane pyrolysis technology for the CO2-free production of hydrogen from natural gas. Compared to other processes for emission-free hydrogen production, methane pyrolysis requires only around one-fifth as much electrical energy. A pilot reactor has been constructed in Ludwigshafen and is being started up. Funding for this project was provided by the German Federal Ministry of Education and Research.
- In collaboration with Siemens Energy, BASF is currently investigating possibilities for the construction of a PEM (proton exchange membrane) water electrolysis system with a capacity of 50 MW for CO2-free production of hydrogen from water and electricity at the Ludwigshafen site. This CO2-free hydrogen would be primarily used as a raw material in the Verbund but would also be used to a limited extent to support the launch of the mobility market in the Rhine-Neckar metropolitan region.
- At the Antwerp site, BASF is planning to invest in one of the largest carbon capture and storage (CCS) projects under the North Sea. Together with partners in the Antwerp@C consortium, this creates the opportunity to avoid more than 1 million metric tons of CO2 emissions per year from the production of basic chemicals. A final investment decision is targeted for 2022.
BASF adds it is trying to secure funding from European and national programs such as IPCEI (Important Projects of Common European Interest).
“We are convinced that ultimately all players involved will work together to make this once-in-a-century transformation economically successful. This also includes consumers accepting higher prices for CO2-free products throughout the value chain to offset higher operating costs and additional investments. To achieve this, we need new cooperation between industry and policymakers that leads to positive, outcome-oriented regulations and preserves our international competitiveness,” said Brudermüller.
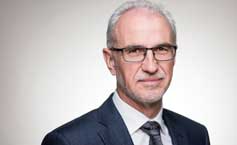
Meanwhile in other news, German chemical firm Evonik says it is pooling its activities for circular plastics in a global program. As part of the transition to a circular economy, the company offers its customers solutions for all stages in the polymer value chain. Additives and technologies from Evonik make mechanical and chemical recycling more efficient thus improving the availability of circular plastics. Evonik will also increase the use of sustainable raw materials from circular sources in its own production processes. Overall, the company expects its global circular plastics program to generate additional sales of more than EUR350 million a year by 2030.
“The careful use of resources and protection of the climate leads us down the path towards a circular economy,” said Harald Schwager, Deputy Chairman of Evonik's executive board, who is responsible for innovation. “We have the innovative capability to create new materials cycles with fewer fossil-based feedstocks and more circular ones. We intend to utilise that potential.”
More than 350 million tonnes/year of plastics are produced worldwide. However, only a small fraction of that amount is recycled. Evonik can facilitate the transformation to a circular economy for sustainable plastics applications with its additives and solutions, and that at competitive cost and quality.
“We are working closely with partners along the entire polymer value chain to make this happen,” said Lauren Kjeldsen, who is responsible for Evonik's global circular plastics program. “Innovations are the key to success.”
In mechanical recycling, plastics are sorted, prepared and washed, before being melted and granulated into a recyclate. This procedure is used mainly for thermoplastics and in a similar process for old tires. Evonik experts are working to help recyclers significantly improve the efficiency and quality of the processes. For example, customised surfactants are used to make sure labels can be removed quickly without leaving residues, while defoamers simplify washing processes and dewatering agents save energy and time in subsequent drying. Another focus is minimising the odour of the recyclate. Specialty additives from Evonik can increase the amount of high-quality re-usable recyclate obtained by about 5%. Evonik aims to offer such solutions for about 400,000 tonnes of recyclable plastics by 2025.
Evonik is also working on various chemical recycling technologies for plastic waste that cannot be recycled mechanically. Here, the polymer chains are split to obtain building blocks for the production of new plastics. For example, Evonik is currently developing a process to facilitate recycling of heavily contaminated polyethylene terephthalate (PET) waste. New molecules for high-end applications can be obtained via methanolysis.
Another method of chemical recycling is controlled incineration of plastic waste to produce pyrolysis oils or synthesis gases. Evonik offers modern technologies that play a part in making these processes more efficient. Examples are additives, catalysts, and membranes for the treatment of gas. These pyrolysis oils and synthesis gases can be used as raw materials for the production of plastics.
(PRA)
Subscribe to Get the Latest Updates from PRA Please click here
©2021 Plastics and Rubber Asia. All rights reserved.
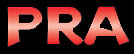
©2020 Plastics and Rubber Asia. All rights reserved.
Home Terms & Conditions Privacy Policy Webmail Site Map About Us