Plastics compounding: analysing major trends and opportunities
The world of plastics is rapidly changing and evolving, and so are trends in the global plastics compounding industry. As plastics replace conventionally used materials in key applications such as automotive, construction, consumer goods, and electronics, the industry is constantly witnessing new technological advances and developments.
Plastics compounding, alternatively known as polymer compounding, is an effective method for altering the fundamental properties of engineered thermoplastics and enhancing their thermal, electrical, physical, or aesthetic characteristics. The final end-product is usually a blend of plastics and various additives.
It is estimated that the global plastic compounding market size will be worth over US$169 billion by the year 2026, with new applications constantly emerging across numerous industry verticals.
Aurora Plastics, BASF SE, Solvay, Lanxess AG, Chevron Phillips Chemical Company, LyondellBasell Industries, The Dow Chemical Company, Foster Corporation, PolyOne Corporation, and A. Schulman are some of the prominent names in the industry.
Let’s dive into some of the technology trends and developments, key challenges caused by the ongoing Covid-19 pandemic, and opportunities that these companies will witness over the next few years.
Ongoing developments and innovations
Both plastics compounding companies and research institutes have been at the forefront of leading innovation in the plastic processing space as they aim to develop more advanced and versatile materials.
In October 2020, German engineered plastics producer Romira had developed the Romiloy EXP3008, a high performance PC/PBT blend with superior impact strength, UV stability, and reduced warping tendency. The product is suitable for both indoor and outdoor applications in areas such as electronics, healthcare, and consumer goods.

During the same year in June, a team of innovators from UK’s Purdue University had developed a new compounding technology for nanocellulose composites that could enhance their sustainability in applications including automotive, food packaging, and consumer goods. Normally for processing nanocellulose, solvents or dispersants are added to improve its dispersion in polymers. However, these techniques can be expensive for manufacturers who also need to implement additional machinery and processes in order to comply with the latest emission standards.
The team created a new technique that involves the blending of nanocellulose in additives for polymers, and then compounding the mixture into the finished product instead of mixing them directly. It allows the nanocellulose to be easily injection molded or extruded into final products that are more sustainable and possess better properties.
This technology could be applicable to a wide range of polymers, including polyamides (PAs) used in automotive applications and polylactic acid (PLA) used in food packaging.
Need for capacity expansion to meet the growing demand
Plastics are dominating virtually every industry vertical and constantly finding their way into new applications as they evolve. In order to keep up with the demand for highperformance materials across different industries, plastic manufacturers worldwide are looking to ramp up the production of compounded plastics.
In February 2019, for instance, Aurora Plastics had finished the upgrading and expansion of its Texas-based plastic production and compounding facility. The new 60,000 sq ft facility includes upgrades in automation and control systems, compound blending, and a new research centre with improved product testing capabilities.

Last year in June, Mitsui Chemicals Inc. along with its subsidiary Prime Polymers began operations at the Mitsui Prime Advanced Composites Europe B.V. (ACE) located within Netherland’s Chemelot Industrial Park. Mitsui’s first PP compounding facility in the European region, the new plant has a capacity of nearly 30,000 tonnes/year.
Over the years, the Mitsui Chemicals Group has managed to boost its global PP compounding capacity to more than 1.12 million tonnes/year. Currently, the company operates production units in eight key markets around the world including the US, Europe, Brazil, Mexico, India, China, Japan, and Thailand.
Emerging markets in the Asia Pacific region with rapid population and economic growth are constantly attracting the attention of major automotive and electronics manufacturers in America and Europe. These factors are likely to stimulate the regional demand for high-quality polymers and advanced materials, encouraging local players to boost their production capacity. In February 2018, Japan’s Teijin had invested over US$13 million to set up a new polymer compounding facility in Thailand with a capacity of approximately 10,000 tonnes/year.
Recent notable acquisitions and collaborations
The plastics compounding market has witnessed several major acquisitions and collaborations over the past few years as manufacturers look to expand their market position. Back in August 2018, LyondellBasell had acquired A. Schulman for US$2.25 billion, allowing the company to nearly double the size of its Houston-based compounding business. Another major company based in Houston, Texas, Ascent Performance Materials has been picking up compounding companies based in the European region. In January, the company acquired France-based compounder Eurostar Engineering Plastics, followed by the acquisition of Italian compounding and masterbatch firms Poliblend and Esseti Plast GD from the D’Ottavio Group in February.
Meanwhile, many companies are collaborating with other manufacturers to develop high-performance materials for various applications.
In May last year, German materials firm Covestro had announced that it is collaborating with plastics compounder Teknor Apex for developing compounded thermoplastic polyurethane, a highly versatile plastic material that finds application in a wide range of industries.
Citing another instance, in November, US-based Eastman Chemical Company had collaborated with Italy’s Gruppo Maip to develop new sustainable polymer solutions for automotive interior applications. The companies aim to use Eastman’s Advanced Circular Recycling technology to formulate a range of molecular recycled and biobased solutions.
See report page here
Read more...
(PRA) Subscribe to Get the Latest Updates from PRA Please click here
©2021 Plastics and Rubber Asia. All rights reserved.
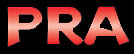
©2020 Plastics and Rubber Asia. All rights reserved.
Home Terms & Conditions Privacy Policy Webmail Site Map About Us