Extrusion Machinery: Davis-Standard encompasses total solution
Davis-Standard, headquartered in Pawcatuck, Conn., is a global leader in the design, development and distribution of extrusion and converting technology. Davis-Standard systems encompass over 11 product lines to support manufacturing applications and customers within every major industry. At the upcoming Chinaplas 2021 show, to be held 13-16 April in Shenzhen, China, Davis- Standard will market total solutions encompassing product capabilities and support services at Booth #R11, Hall 10.

After so many Covid-19 show cancellations, Chinaplas 2021 will be held in April, with Davis-Standard being one of the many machinery firms that look forward to reconnecting with customers and the greater plastics community. Global aftermarket services and equipment technology for sheet, foam, blown film, thermoforming, pipe, profile and tubing, cast film, extrusion coating and liquid coating will be promoted by the US firm.
Davis-Standard (Suzhou) Machinery is central to the company’s customer focus and expansion in Asia. Developments in the areas of machine building and assembly, inventory and aftermarket services, field service engineering, and installation at customer sites have been essential to supporting customers.

The Suzhou site sits on a workshop and office space of 7,500 sq m. This was increased in 2019 by 3,300 sq m, to house control panel assembly and provide additional warehousing.
PRA finds out more on the machinery and company activities in this interview with Jim Murphy, President/CEO of Davis-Standard.
PRA: Please tell us more about the new technology being displayed at Chinaplas
Jim: The newest item we are showing is our dsX flex-pack™ 300S line. This single station extrusion and lamination line is a collaboration between Davis- Standard’s design teams in the US, Germany and China, and is built at the Suzhou facility to meet the requirements of the Asian flexible packaging market.

It is advantageous for converters as it accommodates the value, machine footprint, output, and key technical attributes demanded by Asian customers. The 300S can support web widths from 650 to 1,350 mm, and is engineered for processing rates up to 300 m/minute for paper, film and aluminum foils with direct gravure primer coating and coextrusion lamination stations. Hallmarks of the line include consistent endproduct quality, greater uptime and productivity, reduced waste and application versatility.
PRA: How has the Suzhou plant operated during the pandemic lockdown and what was the biggest challenge D-S had to contend with/overcome during the pandemic?
Jim: Suzhou has adapted well to serving customers throughout Asia using the safety protocols we have put in place worldwide to protect employees and customers, while ensuring efficient delivery of the spare parts, equipment and services they need.
The biggest challenge faced by Davis- Standard was and is the safety of our employees, customers and business partners. The pandemic has influenced all aspects of our business. We’ve been primarily focused on creating processes to safely interact with customers and provide them with the products and services they need to meet their production demands.
PRA: Smart factory solutions will also be presented at Chinaplas. How do you think the Smart factory solutions can help manufacturers in their recovery journey towards the postpandemic years
Jim: As plants worldwide move toward greater efficiency, Davis-Standard will present the Smart factory solutions at Chinaplas.
Any technology that delivers greater efficiency and supports profitability will help manufacturers in their recovery. An example of smart technology from Davis-Standard is our DS Activ-Check™ system, which builds on our knowledge of machinery and processes.
DS Activ-Check™ harnesses the interconnectivity and functionality of the Industrial Internet of Things (IIoT) to analyse real-time KPIs (key performance indicators) and enable alarms or action prompts using an integrated machine control system. This system monitors key parameters of an extrusion or converting line to provide early notifications of potential failures allowing operators to avoid unscheduled downtime and providing valuable data for process improvement using configurable dashboards.
PRA: What can we look forward to from D-S in the new normal?
Jim: We have long supported customers in their pursuit of better processing, including sustainability and recycling all types and forms of plastic materials. These include in-line recycling of trim generated during the production process and specialised equipment to recycle postconsumer plastic materials of all shapes and sizes.
PRA: Has the pandemic affected D-S’s previous acquisitions (Deacro Industries, Brampton Engineering, Maillefer, TSL)?
Jim: All operations within Davis-Standard have been recognised as essential manufacturing businesses, so we have functioned nonstop throughout the pandemic. This includes our recent acquisitions, which continue to grow and serve customers across multiple industries.
In fact booth visitors at Chinaplas can expect to find information on every Davis-Standard product line, including equipment technology from recent acquisitions. Maillefer has delivered wire and cable and pipe and tubing equipment on a global level, complementing the FPVC medical tubing and coextrusion applications supported by the Suzhou location. This includes pipe and tube systems for automotive, heating and plumbing, irrigation, medical, micro-duct, off-shore and custom lines.
Adding Brampton Engineering has further supported regional infrastructure for blown film applications.
Thermoforming Systems (TSL) has enabled Davis-Standard to offer solutions in sheet extrusion, tooling, automation, and granulating to support thermoforming applications, such as cold drink cups/lids, fast food takeout containers, clamshells and noodle bowls, fruit punnets and coffee pods.
Most recently, the addition of Deacro Industries has increased equipment options with high-performance slitting, rewinding and roll handling equipment for the converting process of paper, film and foil materials.
PRA: Do you still view Asia as competitive as it was before the pandemic?
Jim: The Asian and Southeast Asian markets have been an important part of the strong order growth we saw in the second half of 2020. These markets are growing faster than other parts of the world. They continue to be a focus for Davis-Standard as many customers in the region look for leading technology to serve these fast-growing markets. We also anticipate that pent-up consumer demand will drive a stronger market this year in Asia and elsewhere.
PRA: What projections/expectations do you have for the automotive, medical devices and packaging markets? Will you be introducing new technologies anytime soon and will there be new expansions and capacities, as well as mergers/acquisitions for D-S?
Jim: We have seen robust market demand in automotive, medical and packaging markets. Specific to Asia, our high-output systems for medical tubing, cast film, blown film and extrusion coating have been essential to medical and packaging applications.
Read more...
(PRA) Subscribe to Get the Latest Updates from PRA Please click here
©2021 Plastics and Rubber Asia. All rights reserved.
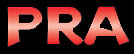
©2020 Plastics and Rubber Asia. All rights reserved.
Home Terms & Conditions Privacy Policy Webmail Site Map About Us