Engel to showcase new digital products for its machine
How can consistently high product quality be maintained in the face of fluctuations in raw material? How can high machine availability and productivity be ensured even in the face of travel restrictions? Austrian machine firm Engel says it will be providing answers to these burning questions during Chinaplas. “Covid-19 has accelerated digitalisation in the plastics industry,” says Gero Willmeroth, President East Asia and Oceania at Engel. “Smart service and intelligent assistance have become even more prominent in the last 12 months.” Thus, Engel’s exhibit of an all-electric and tie-bar-less e-motion 80 TL machine will be equipped with many digital products from its inject 4.0 programme.
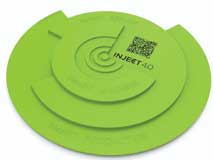
During the four days of the show, fluctuating process conditions can be simulated on the CC300 control unit of the e-motion 80 TL machine in order to track automatic readjustment by the smart assistance systems on the machine display. For example, iQ weight control keeps the injected melt volume consistent throughout the process, while iQ clamp control determines the optimum clamping force based on mould breathing.
The latest products to be presented in Shenzhen include iQ process observer and iQ melt control. Where smart assistance systems have so far been able to optimise individual steps in the moulding process, the new iQ process observer continually analyses several hundred process parameters across all four phases of the process – plasticising, injection, cooling and part removal – in order to automatically detect drifts. In the form of plain text messages, the system points out unfavourable process settings and conditions as well as the possible causes of them.
The goal of iQ melt control is to conserve both the material to be processed and the mechanical components of the plasticising unit. In practice, plasticising often occurs faster than the cycle requires, which can have an impact on product quality, but also on the service life of the screw. iQ melt control therefore determines the optimum plasticising time. Instead of plasticising at the maximum possible speed, the system makes full use of the part’s in-mould cooling time for plasticising, ensuring very good melt homogeneity.
Another new feature is sim link, a joint development by Engel and Autodesk, the provider of the Moldflow simulation software. With the support of the software, both the parameters optimised by Moldflow can now be converted into a process settings data set and used directly on the machine, and conversely, process parameters and measurement results from the machine can also be imported into Autodesk’s simulation programme.
(PRA)
Subscribe to Get the Latest Updates from PRA Please click here
©2021 Plastics and Rubber Asia. All rights reserved.
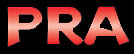
©2020 Plastics and Rubber Asia. All rights reserved.
Home Terms & Conditions Privacy Policy Webmail Site Map About Us